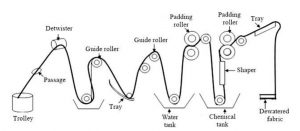
Textile Finishing | De-watering Machine | Slitting Machine | Dryers | Sueding Machine
Textile Finishing | De-watering Machine | Slitting Machine | Dryers | Sueding Machine
Textile Finishing
Finishing is the term used for a series of processes to which all bleached, dyed, printed and certain grey fabrics are subjected before they put on the market. Finishing is done to render textile goods fit for their purpose or end-use or serviceability of the fabric. It should be considered that every finishing process should improve the serviceability of the fabric like dimensional stability, fastness to washing, fastness to storage, wearing quality, resistance to fibre slippage, strength of the fabric, fabric handle etc. Cotton and polyester has different processes of finishing. Fabric that contains lycra needs another additional process done that is called heat setting.
The finishing processes are classified into two main streams:
- Mechanical finishing
- chemical finishing
Most of the finishes that are given to the fabric are mechanical finishes. Mechanical finishes are :
- Shearing
- Sueding
- Compacting
- Calendaring
- Steam/ Heat setting.
Chemical finishes includes bio-polishing and softening but bio-polishing is carried out with dyeing in exhaust method. Softening is done in exhaust method as well as in mechanical method.
The main procedures of softening can be divided into two segments:
- Open width finishing line for fabric of open form
- Tube width finishing line for fabric of tubular form
Machines Used in Finishing :
- De-watering Machine
- Dryer Machine
- Compactor Machine
- Stenter Machine
- Slitting Machine
- Sueding Machine
- Tumble Dryer Machine
1 . De-watering Machine : De-watering machines are used to reduce the excess water remaining on the wet fabric after dyeing. Softening chemicals and other finishing chemicals can be applied while de-watering as well. De-watering machines also help to keep in control the GSM of the fabric by maintain proper tension around the whole process. The padding rollers help to apply mixtures of finishing chemicals on the fabric surface. D-ewatering machines can remove from 40-50% of the water content of the fabric. The main parameters of a de-watering machine that are to be considered while operating are the followings:
- Machine speed (m/min)
- Padder pressure (bar)
- Wet stretching (%)
Fig : Path diagram of a dewatering machine
2 . Slitting Machine : This machine basically opens a tubular fabric into open form by slitting along the needle mark of the fabric to aid the slitting process. In addition to opening the fabric, it also untwists the fabric via. rope de-twister device, maintains the fabric width, mangles water from the fabric by extracting up to 60% prior to slitting. The slitting line of the tube fabric is monitored carefully to avoid unnecessary wastage of fabric. . The fabric is passed through a set of padders into a de-twister by which the rope fabric untwists and is spread out with the help of a spreader and the fabric is opened. The fabric is then passed through a few sets of rollers in order to create an even and crease-free surface for stentering.
Fig : Path diagram of a slitting machine
The main parameters of a slitting machine that are to be considered for operating based on the difference among the fabric types are:
- Feed %
- Padder pressure (bar)
- Machine speed (m/min)
Fig : Slitting Machine
4 . Dryers: De-watering and slitting processes of the fabric removes up to 60% of the water content of the fabric. But the dyed fabrics need to be dried completely before proceeding towards further processing. This is why dryers are used to remove water from the fabric without applying any tension. Another thing that the dryer does is controlling lengthwise shrinkage of the fabric which eventually leads to the controlling of the GSM of the fabric.
Dryers are of two types-
- Tube dryers for the tubular fabrics
- Chain dryers/relax dryers for the open fabrics.
Dryer have heating chambers with blowers that provides the necessary heat required to dry the fabric. A conveyer belt passes the fabric through the heat chambers. Temperature of the heat applied depends on the shade of the fabric. There are motors in the heating zone that controls and regulates the gas release of the machine. Chain dryers have a 100% overfeed system and an underfeed system up to 50%. The width of the fabric is controlled by sticking it widthwise to a pinned chain-rail that can be controlled manually. The fabric width is extended with the chain-rail before it enters the heating chambers, keeping the width still while the fabric dries. The receiving end of the machine has a to and fro plaiting system which leads the fabric to pile on easily having the same width.
Fig : Schematic diagram of a chain dryer
Setting parameters for different fabric type of knit fabric :
Fabric type |
Overfeed speed % |
Temperature (°C) |
Machine speed (m/min) |
|
Single jersey | White | 15-25 | 120-140 | 8-15 |
Dyed | 15-25 | 140-150 | 8-15 | |
Polo Pique |
White | 35-40 | 120-140 | 8-10 |
Dyed | 35-40 | 140-150 | 10-15 | |
Rib | White | 15-20 | 120-140 | 10-15 |
Dyed | 15-20 | 140-160 | 8-15 | |
Interlock | White | 20-25 | 120-140 | 15-20 |
Dyed | 20-25 | 140-160 | 15-20 | |
Lacoste | 30 | 140 | 20 |
6 . Sueding Machine :
Sueding involves creating peach skin like surface on the fabric which gives soft, smooth feel and provide more formal look while maintaining comfort and casual feel. Method of Application: Open width knitted fabric is passed over rotating high speed carbon brushes. There are a total of six rollers active, three rotating in the opposite direction of the fabric direction and the other three rotating along the fabric direction. By adjusting angle of
contact with the brushes, pressure against fabric and speed of fabric being sueded, the intensity of sueding can be varied.
Effect: Peaching softens fabric handle and gives a greater degree of warmth to the fabric. Surface hairs of the fabric are separated from each other, giving a sort piled surface. It however lightens the shade of a colored fabric and can give slight unevenness. Where grey fabric is emersed, the subsequent wet processing, that is dyeing and washing, may be used to remove the dust generated.
Factors affecting the degree of sueding–
- Number of rollers in operation
- Direction of rotation of the rollers against the fabric
- Fabric tension
- Fabric speed
- Wrapping angle on the roller
(75)