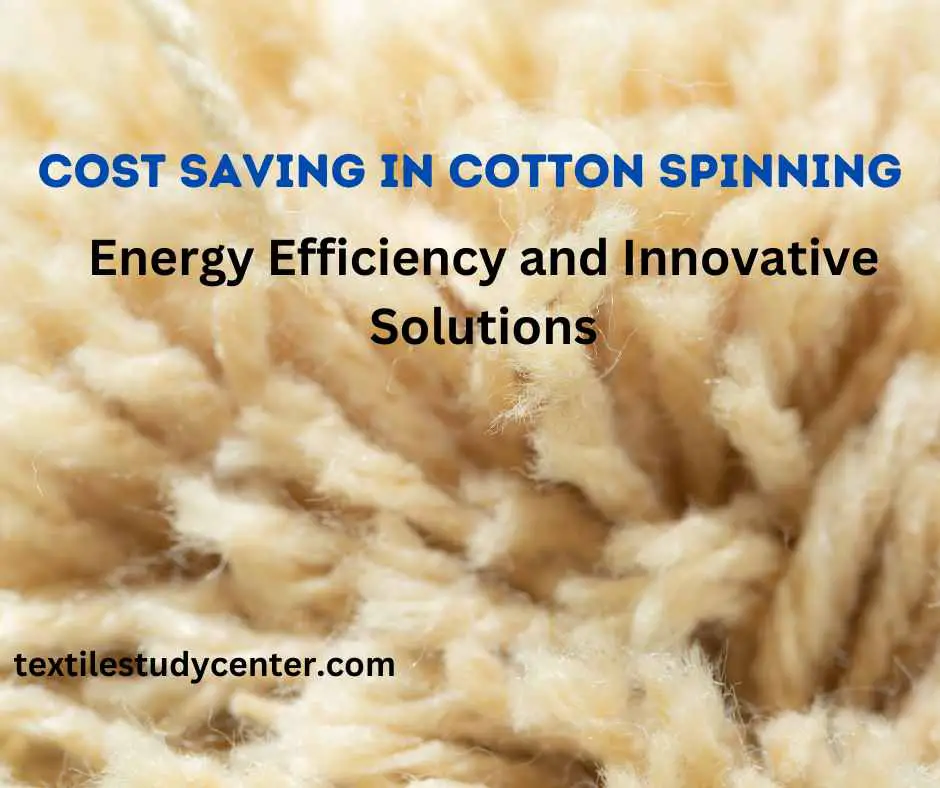
Cost Saving in Cotton Spinning: Energy Efficiency and Innovative Solutions
Cost Saving Opportunities in Cotton Spinning: Energy Efficiency and Innovative Solutions
In the cotton spinning process, reducing expenses is crucial for maximizing profitability and sustainability. This blog explores various cost-saving measures, focusing on electric power and water consumption, as well as alternative solutions for costly parts. By adopting these strategies, spinning mills can improve their operational efficiency while minimizing their environmental impact.
1 . Electrical Energy Saving in Humidification Plants
Humidification plants play a vital role in maintaining the right level of humidity in spinning mills, ensuring the quality of the cotton yarn. However, they can consume substantial electrical energy. Implementing the following technologies can significantly reduce energy consumption and maintenance costs:
A . Atomizing Water with Misting Nozzles: Atomization techniques, such as using high-pressure pumps (around 1000 psi) and fine misting nozzles (0.1 mm), can reduce the power consumption of evaporative cooling by approximately half. Though nozzle choking may be an issue, this method proves effective in conserving electrical energy.
B . Water Atomization with Compressed Air: This system utilizes fine misting nozzles without the need for pumps, inverters, MS headers, and numerous showering pipes and nozzles. By operating on line water and eliminating the need for water storage tanks, mills can save water and reduce the cost of chemicals required for water treatment. Additionally, the system ensures air washing of the department without the need for excessive water consumption.
It is essential to debunk the misconception that misting systems do not wash the air. The air passes through the water mist, carrying moisture, and maintaining the desired humidity level. Depending on the weather conditions, a substantial portion of the air can be passed through without the need for air washing, leading to significant energy and water savings.
Cost of Misting Systems: Misting nozzles vary in price, with options ranging from Rs. 5000 to Rs. 22000 based on their size. However, mills can further reduce costs by producing these nozzles in their workshops, cutting down expenses to Rs. 1500 to Rs. 3000 per nozzle. Many companies are already installing misting nozzles above machines in departments, demonstrating the effectiveness and popularity of this low-power technique.
2 . Electrical Energy Saving in Blow Room Carding Rotary Filters
The rotary filter system in the blow room and carding operations is another area where significant electrical energy can be saved. By optimizing the filter load and diverting exhaust air from unnecessary fans, mills can reduce power consumption. This can be achieved by creating a separate room for exhaust air pipes, directing the air into dust bags to collect short fibers and dust, and releasing the cleaned air through nylon mesh without the need for additional suction fans.
3 . Water Heating Cost Saving in Textile Processing
Incorporating solar water heating systems can lead to substantial cost savings for mills engaged in textile processing. With a remarkably short return on investment (ROI) of about 6 months to 1.5 years, these systems efficiently utilize solar energy to heat water used in air conditioning and other processes. By reducing reliance on traditional water heating methods, mills can reduce operating costs and their carbon footprint.
Concluding, Cost-saving opportunities in the cotton spinning process are abundant, and by focusing on electrical energy efficiency, water consumption, and innovative solutions, spinning mills can achieve significant improvements in their financial performance and environmental responsibility. Embracing these strategies not only helps mills thrive in a competitive market but also showcases their commitment to sustainability, making them attractive partners for environmentally-conscious consumers and stakeholders. By continuously exploring and implementing such initiatives, the cotton spinning industry can move towards a greener and more prosperous future.
(209)