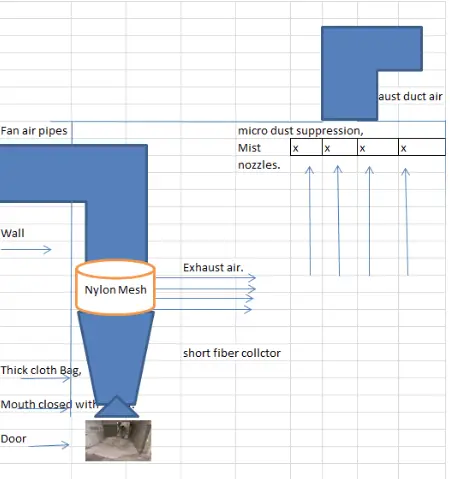
Energy Saving in Blow Room and Carding Rotary Filter: A Cost-Effective Solution for Spinning Mills
Energy Saving in Blow Room and Carding Rotary Filter: A Cost-Effective Solution for Spinning Mills
Energy conservation and cost reduction are paramount concerns for every spinning mill. Among various energy-consuming processes, the blow room and carding operations stand out as major consumers. In this blog, we will explore a practical approach to save energy in the blow room’s rotary filter system and discuss the potential cost savings it can bring to the spinning mill.
The Rotary Filter System
A rotary filter system is an essential component in a spinning mill’s blow room. Its primary function is to extract dropping wastes, dusty air from the multimixer, and air from condensers, B-11, and Dustex fans. While these fans perform various tasks, not all of them require radial fan suction; some only need to expel clean air that passes through a filter media.
Energy Saving Solution
The key to achieving energy savings lies in optimizing the filter load and reducing unnecessary fan suction. By diverting the exhaust air from all air-throwing fans away from the rotary filter, we can significantly reduce the load on the system.
Here’s how the energy-saving solution works:
- Separate Room for Exhaust Air Pipes: Create a separate room where all the exhaust air pipes from Dustex, condensers, B-11, and other components are directed. These pipes will expel their air into dust bags for collecting short fibers.
- Collecting Short Fibers and Dust: The separate dust bags will efficiently collect the short fibers and dust, preventing them from clogging the filter media.
- Cleaned Air through Nylon Mesh: After the short fibers and dust are collected, the cleaned air will pass through a nylon mesh, ensuring that only purified air is released.
- Natural Air Discharge: Since the air would now be expelled with its own pressure, there’s no need for additional suction fans, resulting in energy savings.
- The cleaned air is passed under a dust separation system installed at the end of exhaust dust to drop micro dust and other particulate matter.
Benefits and Cost Savings
By implementing this energy-saving solution, the spinning mill can reap various benefits, including:
- Reduced Power Consumption: The current rotary filter system consumes approximately 20 kW of power. With the proposed changes, the load on the filter will be significantly reduced, leading to substantial energy savings.
- Motor Shutdown: Pre-filter and dust collector motors can be stopped, further conserving energy and reducing operating costs.
- Monthly Savings: Considering the spinning mill operates 22 hours per day and the cost per kWh is Rs. 20, the estimated monthly savings can amount to a considerable Rs. 22,400.
Energy saving is crucial for the sustainability and profitability of spinning mills. By optimizing the blow room’s rotary filter system and implementing the proposed changes, mills can achieve substantial energy savings and cost reductions. Moreover, this eco-friendly approach promotes efficient waste management, contributing to a cleaner environment.
Investing in energy-saving measures not only benefits the mill’s financial bottom line but also demonstrates a commitment to responsible resource utilization. As the textile industry moves towards greater sustainability, embracing such energy-saving initiatives becomes a vital step for spinning mills to thrive in a competitive market while reducing their environmental impact.
(Note: The energy-saving figures mentioned in this article are based on the data provided and may vary depending on individual mill operations and energy tariffs.)
(143)