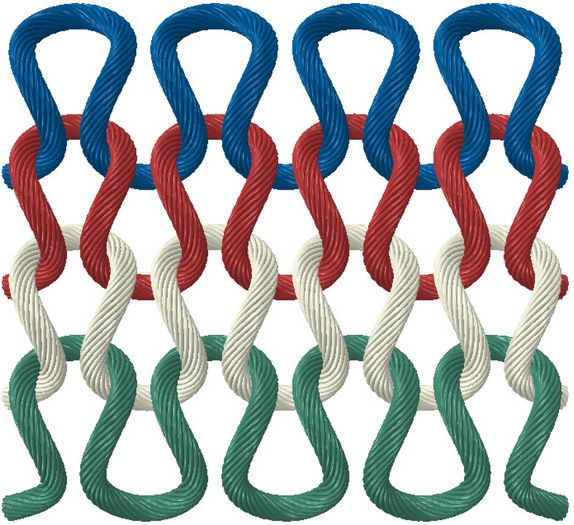
Knitting Terms and Definition
Knitting terms and definition
Fabric forming process
Weaving is the interlacement (Fig.a) of two sets of threads (i.e. warp and weft) at a right angle.
Interlooping (Fig.c) consists of forming yarn(s) into loops, each of which is only released after a succeeding loop has been formed and intermeshed with it.
Includes a number of techniques, such as braiding and knotting, where threads are caused to intertwine (Fig.c) with each other at right angles or some other angle.
Knitting :
Knitting is a technique to turn thread or yarn into a piece of cloth. Knitted fabric consists of horizontal parallel courses of yarn which is different from woven cloth. The courses of threads or yarn are joined to each other by interlocking loops in which a short loop of one course of yarn or thread is wrapped over the another course.
Definition
Knitting is a process of fabric forming by the intermeshing the loops of yarns. When one loop is drawn through another, loops are formed in horizontal or vertical direction.
Types of Knitting
There are two of knitting-
- Weft knitting
- Warp Knitting
Weft Knitting is a method of forming a fabric in which the loops are made in horizontal way from a single yarn and intermeshing of loops take place in a circular or flat form on across wise basis.
Warp Knitting is a method of forming a fabric in which the loops are made in vertical way along the length of the fabric from each warp yarns and intermeshing of loops take place in a flat form of length wise basis.
Course :
The series of loops those are connected horizontally, continuously are called as course.
The horizontal row of loops that are made by adjacent needles in the same knitting cycle.
Wales :
The series of loops that intermeshes vertically are known as Wales.
Vertical column of loops that are made from same needle in successive knitting cycle
Features of wales
When loop transfer occurs it is possible to transfer a wale of loops from one needle A to another B.
In warp knitting a wale can be produced from the same yarn if the same warp guide laps the same needle at successive knitting cycles.
Wales are connected together across the width of the fabric by sinker loops (weft knitting) or underlaps (warp knitting).
Wales show most clearly on the technical face and courses on the technical back of single needle bed fabric.
Parts of a loop
Each knit stitch (knit loop) is a basic unit for the knitted goods
H: Head or Crown or top arc
L: Side limbs or Legs
S: Bottom arc or Sinker loop
→Needle loop=H+2L
→A complete loop=Needle loop+Sinker loop
Needle loop:
Needle loop is the upper part of the loop produced by the needle drawing the yarn.
Sinker loop:
The lower part of the knitted loop is technically referred as sinker loop. It is the connection of two legs belonging to neighboring stitches lying laterally.
Open loop:
The open loop is one in which the loop forming yarns do not cross at the bottom of the loop.
Closed loop:
In closed loop the legs cross at the bottom, so that the loop closing takes place.
Face loop and technical face
Face loop:
During loop formation, when the new loop emerges through the old loop from back to the face side then it is termed as face loop or weft knitted loop.
Technical face:
The side of the fabric which contains all face loops or weft knit loops is known as technical face.
Back loop and Technical Back
Back loop:
During loop formation, when the new loop passes from the face side to the back of the previous loop then it is termed as back loop or purl loop.
Technical back:
The side of the fabric which contains all back loops or purl loops is known as technical back.
The knitted stitch is the basic unit of intermeshing. It usually consists of three or more intermeshed needle loops. The centre loop has been drawn through the head of the lower previously-formed loop and is, in turn, intermeshed through its head by the loop above it.
Notations
Knitting notation is a simple, easily-understood, symbolic representation of a knitting repeat sequence.
Its resultant fabric structure that eliminates the need for time-consuming and possibly confusing sketches and written descriptions.
Notations are used to express the knitted fabric structure and design.
Notations are of four types:
1.Verbal notation.
2.Line diagram/ Looping diagram
3.Diagrammatic notation/ Chain notation
4.Symbolic notation
The length of yarn required to produce a complete knitted loop (i.e Needle loop and sinker loop) is known as stitch length or loop length.
Stitch length is a length of yarn which includes the needle loop and half the sinker loop on either side of it.
Generally, the larger the stitch length, the more extensible and lighter the fabric and the poorer the cover and bursting strength.
A course length
In weft knitted fabrics, a course of loops is composed of a single length of yarn termed a course length.
Definition: The length of yarn required to produce a complete knitted course is known as course length.
Course length= No. of loops per course X Stitch length
Course length= No. of needles X Stitch length
Stitch density
Stitch density refers to the total number of loops in a measured area of fabric.
It is the total number of needle loops in a given area (such as a square inch
Stitch density= Wales density x Courses density
=Wales per inch X Courses per inch
= WPI X CPI
Unit: number of loops per square inch
Or, SD= CPC x WPC (cm scale)
Technically upright
A knitted fabric is technically upright when its courses run horizontally and its wales run vertically, with the heads of the needle loops facing towards the top of the fabric and the course knitted first situated at the bottom of the fabric.
Single jersey & Double jersey
Single jersey or plain fabric: The weft knitted fabric (Tubular/flat) which is produced by one set of needles.
Double jersey: The weft knitted fabric (Tubular/flat) which is produced by two sets of needles.
Fabric draw-off
The fabric loops are always drawn from the needles on the side remote from their hooks. When two sets of needles are employed, the fabric will be produced and drawn away in the gap between the two sets.
Needle bed or needle carrier
Needle bed or needle carrier is the place where the needles are located or mounted in a knitting machine. Needle moves up and down in the trick of a needle carrier.
Two types of needle carrier:
- Cylindrical or circular
- Flat
Cylinder and Dial
Cylinder:
Cylinder is a circular steel bed having grooves / tricks /cuts on it’s outer periphery into which the needles are mounted.
With reference to the tricks, the needles move vertically up and down by their butt being in contact with the cam track.
The diameter of the cylinder also varied based on the type and width of the fabric.
Maximum diameter of the cylinder: 46 inches.
Dial:
Dial is the upper steel bed used in double knit circular machines.
Into the grooves of the dial, the needles are mounted horizontally and are allowed to move radically in and out by their dial cams.
The number of grooves per unit space conforms with the cylinder gauge in most of the cases.
Machine gauge or Needle gauge
The number of needles present in one inch of a needle bed is called machine gauge. It is denoted by G or E.
Needle pitch:
The distance between two neighboring needles
Space required for each needle.
Feeders are the yarn guides placed close to the needles to the full circumference of the knitting zone.
The feeders feed the yarn into the needle hooks and control the needle latches in their open position while the needle attain their clearing position.
A selvedge fabric is one having a “self edge” to it and can only be produced on machines whose yarn reciprocates backwards and forwards across the needle bed so that a selvedge is formed as the yarn rises up to the next course at the edge of the fabric.
Cut edge fabric usually produced by slitting open a tube of fabric produced on a circular machine. A slit tube of fabric from a 30” diameter machine will have an open width of 94”(πd) at knitting & before relaxation.
Tubular Fabric
This may be produced in double faced or single faced structures on circular machine, or in a single faced from on a straight machines with two sets of needles provided each needle set only knits at alternate cycles and that the yarn only passed across from one needle bed to other at the two selvedge needles at each end, thus closing the edges of the tube by joining the two single faced fabrics produced on each needle set together.
Main features of a knitting machine
- The frame, normally free standing and either circular or rectilinear according to needle bed shape, provides the support for the majority of the machine’s mechanisms.
- The machine control and drive system co-ordinates the power for the drive of the devices and mechanisms.
- The yarn supply consists of the yarn package or beam accommodation, tensioning devices, yarn feed control and yarn feed carriers or guides.
- The knitting system includes the knitting elements, their housing, drive and control, as well as associated pattern selection and garment-length control device.
- The fabric take-away mechanism includes fabric tensioning, wind-up and accommodation devices.
- The quality control system includes stop motions, fault detectors, automatic oilers and lint removal systems.
How to write a machine specification?
Weft knitting machine
Circular:
→Single jersey circular knitting machine.
→Rib circular knitting machine.
→Interlock circular knitting machine
→Socks circular knitting machine.
→Double cylinder purl knitting machine
Flat:
→Flat knitting machine
→ V-bed flat knitting machine
→ Straight bar frame
knitting terms and definitions
Different types of Knitting needles
Different types of Sinkers
(42206)