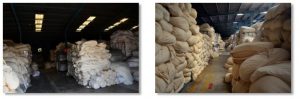
Batching in Textiles
Batching in Textiles
Batching, a process monitored and supervised by the dyeing manager, is carried out in the batching section. It involves preparing a batch for dyeing according to machine capacity (so that equal amounts of fabric is passed through each nozzle of a dyeing machine), order and priority basis. Grey fabric from grey fabric storage or knitting section is collected in order to dye a particular shade of color.
Objectives of batching:
- To make a batch from the same fabric material
- Prepare the fabric batch for dyeing according to the following criteria –
- Order sheet (received from buyer)
- Dyeing shade (light, medium, deep shade or white)
- Machine capacity
- Machine availability
- Type of fabric to process (100% cotton, CVC, PC, fleece, rib etc.)
- Weight the fabric correctly and accurately for creating a correct recipe and avoid dye and chemical wastage along with shade mismatched shades
- Receive grey fabrics from grey storage or knitting section
- Make a batch plan manually, keeping in mind the process losses which would take place along production route (e.g. dyeing process loss, cutting loss etc.)
- Prepare a batch card having necessary information about the batch, such as color to dyed, grey fabric parameters, finishing parameters etc.
- Arrange the fabric for dyeing according to quantity, fiber type, fabric structure and shade
- Gradually reduce grey fabric inventory (which is replenished as production proceeds)
- Reduce idle time of a dyeing machine
- Keep the floor free from extra material
- Turn the fabric when required using a turning machine.
Factors for batch preparation:
Key factors that are to be considered to prepare a batch are:
- Type of yarn
- Structure of fabric
- GSM of fabric
- Amount of fabric
- Rope length/Cycle turnover time
- Machine type
- Machine capacity
- Machine availability
- Shade of dyeing
- Priority of work Etc.
Target of batching:
- Minimize or optimize the number of batches
- Create batches so that different knitted fabric rolls can be distinguished from one another
- Utilize maximum capacity of a dyeing machine, creating batches accordingly
- Keep the number of batches as less as possible for the same shade
- Stick with a particular dyeing machine when dyeing a shade
Fig : Grey Fabric in Store
Procedure of batch preparation :
Making a suitable dyeing plan according to the order sheets, as per priority and availability of dyeing machines
↓
Preparing a batch card in which all the parameters of the required fabric is noted
↓
Receiving required quantity of body fabric according to the machine capacity from the fabric store
↓
Taking required quantity of collar/cuff fabric
↓
Sending the grey fabric to the dyeing section by trolley with the respective batch card
Detailed Flow Chart of Batch Preparation for Dyeing :
After Getting direction from from Grey In-charge :
Taking batch card
↓
Make the priority as per dyeing plan
↓
Take one specific Batch card.
↓
Read the Batch Card for own understanding
↓
Check the availability of fabric
↓
Take required quantity of body fabric from warehouse.
↓
Make required no. of Rope maintaining equal length.
↓
Take collar/cuff as per size, keep the total weight.
↓
Distribute the collar /cuff or Rib in each rope equally unsure equal length
↓
Stitch the fabric
↓
Write down the weight against roll no. in the back side of the Batch Card.
↓
Write the total weight in Batch Card.
↓
Put signature & date.
↓
Fill up the production report form.
↓
Send for the Production
Turning the fabric :
Knit fabrics in which face side and back side are different, needs turning to protect the
face side of the fabric from dirt, dust, spot, color, machine corrosion or any visual or
physical disturbance. Air turning machine is used to turn the fabric face side down.
Fig: Fabric turning machine
(157)