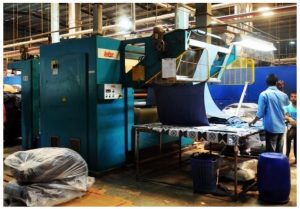
Textile Finishing | Compactor Machine in Textile
Textile Finishing | Compactor Machine in Textile
Compactor
The objective of compacting is to prevent shrinkage of knitted fabric. Compacting can be done with both open width fabric and tubular fabric. Residual shrinkage of the fabrics can be brought down to 3% to a maximum of 0.Along with residual shrinkage, GSM is controlled as well.
Compactors are of two types:
- Open width compactors
- Tube compactors
1 . Open width compacting machine:
Open width compactor is suitable for open width knit fabrics to achieve exact dimensional stability and a soft feel. The machine generally consists of a feeding frame with centering device and driven scroll rollers, an equalizing stenter frame with over-feed roller and brush pinning arrangement. The compacting zone involves the use of steam heated cylinders (140°C) being pressed against a stretched felt type blanker. On this machine, there is a tenter frame where width can be adjusted easily before the fabric enters the compacting zone. This is aided by steam relaxation. This way widthwise shrinkage is gotten. Lengthwise shrinkage is controlled by the felt blankets tension against the fabric. There is a steam box under the tenter frame and before the entry of the compacting zone, which helps with fabric relaxation and shrinkage upon entering the compacting zone. Overfeed of up to 100% can be given. Underfeed being 50%.GSM and shrinkage of the fabric after compaction is measured. It is customary to measure the weight and shrinkage after compaction of a 85 fabric roll at the start in order to determine the settings that need to be adjusted afterwards to give the required values with repeatability.
Fig : Schematic diagram of an open width compactor
Fig : Open width compactor
2 . Tube compactors :
In the shoe type Tube-Tex compactor, lengthwise shrinkage is prevented by exerting an overfeed of up to a maximum of 25%. The feed roller moves faster than the retarding roller which helps to compress the fabric at the point of compaction between the two shoes. Fabric widths processed are 16” to 58” maximum. There is a spreader, similar to the steam setting machine, to control the tubular fabric width. A constant steam supply and steam heated rollers (90 – 110°C) ensure fabric relaxation and swelling shrinkage. Highest shoe pressure is 60 psi. Pressure is exerted on both sides of the steam heated rollers. Shoe gap is adjusted between 0.0 to 1.4 mm. The lower shoe is fixed and upper shoe is movable or adjustable. A cooling net for fabric cooling and spring loaded delivery place follow the exit. Note that rib fabrics are easier to compact than interlock and polo pique fabrics, due to their tight structure and less elasticity like rib fabrics. Also, interlock fabrics are difficult to grip by the shoes. The shoe position can be changed manually by a wheel. Pressures between heated rollers and shoe pressure are all indicated on individual pressure gauges on the side of the machine and the information mentioned along with fabric speed and overfeed (%) are shown on the control monitor.
Fig : Schematic diagram of Tube-Tex compactor
Fig : Tube-tex compactor
(112)