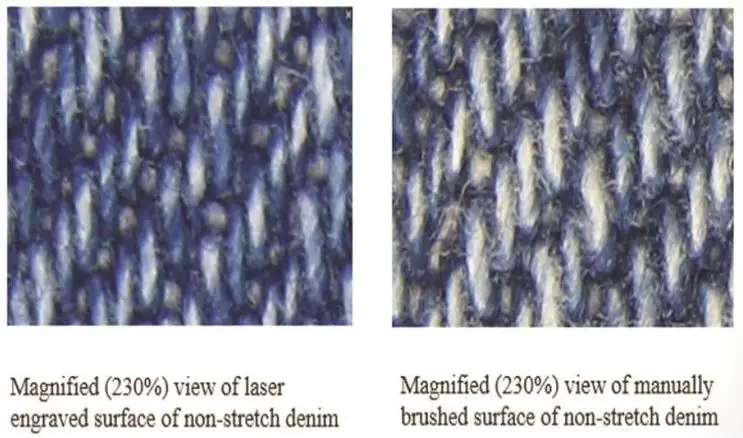
Laser in Denim Industry | Laser Finishing Method | Flow Chart Of Laser Finish
Laser in Denim Industry | Laser Finishing Method | Flow Chart Of Laser Finish | Process description of Laser Finishing | Operating flow path of Easy mark
Laser Finishing Method :
A simple laser-based finishing process is shown in Fig below. The laser beam is moved on the piece of material to be faded by a set of two computer-controlled scanning mirrors. The interaction of the laser beam with the colored material produces a fading in the irradiated area. The residual colorants are expelled by plasma-induced ablation from the material surface and absorbed by a filtered ventilation system.
The process has three steps:
- Computer generation map of the area which will be irradiated with different fluency level function of the desired pattern;
- Control of the laser system, scanning system and conveyor system;
- Laser-fading process.
The third one is the key step of this technology. We focus our attention on it.
The interaction laser beam-material depends on two kinds of parameters: laser beam parameters and material parameters. As laser beam parameters we took into account: energy per pulse, repetition rate, pulse duration, wavelength. The material parameters are thermal diffusivity, reflection coefficient, and heat of vaporization. For material removal from nonmetallic materials, the absorption at the laser wavelength is important. Thus, when one chooses a laser for material removal, it is important to consider the absorption characteristics of the material as a function of wavelength. Laser energy may be lost by reflection from the surface and, in our case, transmission through textile fibers. Depending on the pulse duration, wavelength and power density, various phenomena can occur. We can remove indigo from the textile by using four physical phenomena: vaporization, photoablation, plasma-induced ablation, and shock waves.
Fig : Simple setup for laser-based fading system
The dominant process in material removal by laser may often be simple vaporization, with absorption of the laser energy at a continually retreated surface. As the laser pulse energy increases, the material reaches vaporization conditions more rapidly and there is less time for thermal conduction. The vaporized material can simply diffuse away into the surrounding atmosphere, without further interaction with the beam. The energy balance model gives the upper limit for material removal in this process. The vaporization process is not so convenient to be used in denim fading process because of long interaction time between laser beam and denim. The laser energy has enough time to be absorbed in the textile fiber and starts to burn it.
The photoablation phenomenon means that the energy of the photon is absorbed by the bond within an organic polymer, the indigo in our case, which is primarily covalent. The lowest dissociation energy of indigo bonds is higher than 2.7 eV. The photon energy is 1.2 and 2.4 eV for Nd:YAG laser at fundamental and second harmonic, respectively. Only ultraviolet photons are able to produce photodissociation. The use of excimer lasers could be possible for denim laser fading but for practical reasons (maintenance, reliability in hard working conditions, costs) only CO2 (10.6 nm wavelength) and Nd:YAG laser working at 1.064 nm wavelength and its second harmonic are considered.
Flow Chart Of Laser Finish :
Create Design Pattern
↓
Convert the Pattern into .bmp format
↓
Input the Design into Laser System
↓
Set the Pixel Time
↓
Placing the Garments
↓
Location Identification
↓
Start
[ytp_video source=”RxtS0c2d8Jw”]
Process description of Laser Finishing :
- Create design pattern: Creation of a design pattern and development of pattern from captured photo or design made by computer software.
- Convert into, bmp format: Conversion into grey scale .bmp format (bitmap image format)
- Input the design into Laser system: Putting the design file into the computer attached with laser m/c
- Set the pixel time: Set the luminance of light that will placed on the garments.
- Placing the garments: Placing the garments on honey comb table
- Location identification: Marketing a red light on the garments where laser light fall to make sure garments in placed properly
- Start: run the m/c
Operating flow path of Easy mark supervisor software is given below :
- Open —> Import image —> Open file for insert diagram —> Image Size —> Selection —> Tools —> Pointer Online —> Pointer Online off —> Print.
- Configure —> Advance Configure —> Enable Automatic Selection —> Ok.
- Configure —> Massage Table —> Add (front right, back right, front back right) —> After Adding OK —> Print.
Comparison between the effects of Laser finish and manual Mechanical fading :
Fig : Laser Fading
Magnified view of laser faded surface and manually brushed surface to compare the hairiness :
You May Look on Below :
- Laser in Denim Industry | Classification of Laser Technology
- Laser in Denim Industry | Laser Finishing Method | Flow Chart Of Laser Finish
- Laser in Denim Industry | Advantages and Disadvantages of laser finish | Laser safety
- Laser in Denim Industry | Laser Finish is Safe | Lasers Are Sustainable
- Laser in Denim Industry | Laser Technology
(200)