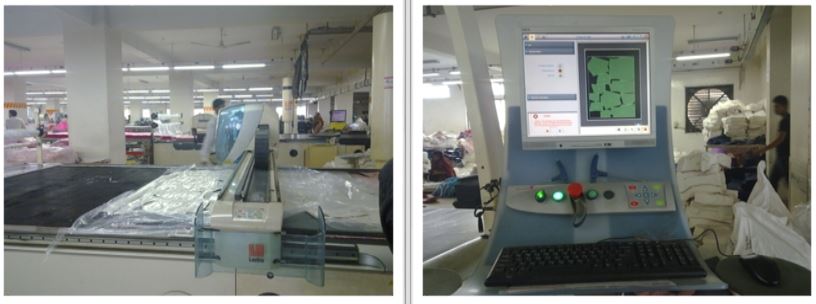
Cutting Section in Apparel Industry | Cutting Room Terminology
Cutting Section in Apparel Industry | Cutting Room Terminology
Cutting Section
To cut out pattern pieces of garment component as per exact dimension of the pattern from a fabric lay is called fabric cutting. It is totally different from general cutting in which exact dimension is not taken into account.
Apparel production starts with the cutting process. In this process, fabric is being cut into components (shapes or patterns of different
garment parts, i.e. front, back, sleeve, collar shapes etc.). In mass production multiple layers of fabrics are laid on a table and large
number of apparels is being cut at a time. The laid fabric stack is called as lay.
The cutting process includes number of sub-processes and flow of the processes is as following :
- Pattern / Marker Making
- Cut Ratio Receiving
- Fabric Receiving
- Fabric Relaxation
- Spreading ( Fabric Layering )
- Marker Making
- Cutting
- Numbering
- Sorting
- Bundling
List of Machines Used in Cutting Room in Apparel Industry :
- Automatic spreading machine
- Automatic cutting machine
- Manual cutting with straight knife
- Round knife cutting machine
- Band knife cutting machine
- Die Cutting machine
- Computerized automatic cutting machine
The term fabric cutting is only applicable for garments manufacturing technology.
Factors affecting the cutting processes :
- Nature of fabric ( grain line shade, twill etc.)
- Thickness of fabric.
- Design characteristics of finished garment.
- Machines and tables used.
Cutting Room Terminology
- Band knife: An endless blade vertical knife, around which work piece is moved over the large cutting table.
- Bias: ‘Cut on the Bias’ – cut at an angle to both the warp and the weft of the cloth, at 45 degree.
- Baker’s trolley: A wheeled rack used to transport sections of the lay from the cutting table to the band knife and from the band
knife to the sorting operations. - Block cutting or blocking out: Cutting roughly around a part which is subsequently cut very precisely, by various means. Also for splitting the lay, to assist handling to the band knife.
- Bowing: A fault in woven cloth in which the weft is not straight across the piece but has curve.
- Clicker press: Used for parts of intricate nature and repetitive, also for parts requiring a high degree of accuracy.
- Cross: ‘Cut on the cross’ – Cut at right angles to the grain of the cloth (On bias).
- Damage: A fabric fault. It may be generated during handling fabric inside factory or faulty fabric sent the fabric supplier.
- Die cutting: Used where accuracy is important and there is enough repetition.
- End loss: The cloth at the end of the lay that is not covered by the marker.
- Face one way spreading: The face side of each ply faces the same way (up or down)
- Face to face spreading: Method of spreading in which the cloth is alternately facing up or down, as a result of continuous to and
fro movement of the roll over the lay. - Face to face one way spreading: Used for directional fabric where the pile (direction) is required to lie in the same direction to the plies.
- Layout (pattern layout): The geometrical layout of the pattern pieces in a garment, which is cut around to produce the parts of the garment.
- Marker: A man who prepares the pattern layout and/or who marks the layout onto the lay or
onto a paper or a cloth. A piece of paper, cloth etc. representing the layout. - Notch: A small cut into the part, which aids the location during assembly by indicating to the operator some requirement for matching with other notches or positions in the garment.
- On the fold: Method of finishing the cloth so that it is folded to half of its width.
- Shading: Means color in cloth. It is commonly used to imply that a particular bit/roll of cloth is different in shade from
another bit. - Shade Numbering : Process of numbering parts to ensure they are of same shade.
- Slub: A local thick place in the yarn in a cloth usually caused by error but in some cloths it is introduced purposely
Operation flow chart of Cutting department :
OTT (On Time Tracking)
⇓
Fabric Receive (from FG store)
⇓
Pilot Cut at least 120 pcs
⇓
Test part sending/receiving Embellishment
⇓
Sending to pilot line for test
⇓
Technical Department
⇓
Receive test report & PP meeting
⇓
PCD (Plan Cut Date)
⇓
Fabric spreading (for bulk)
⇓
Marker making (manual)
Spreading M/C Specification (Lectra):
Fig: Automatic Spreading M/C
M/c name |
Automatic spreading m/c |
Brand |
Lectra |
Origin |
French |
Spreading speed |
(8—10)m/min |
Spreading width |
Max 90” |
Table length |
22m |
Operating system |
Manual button/ automatic |
Service |
Aamra |
Cutting machine Specification (Manual) :
Cutting is done by straight knife cutting m/c. ( For Example )
M/c name |
Straight knife cutting m/c |
Brand |
KM Mack |
Origin |
Japan |
Blade length |
(8-9)inch |
Blade width |
.8 inch |
Cutting height |
6inch |
Blade sharper |
sharper belt |
Motor RPM |
(3000-3600) |
Current |
2.7A |
Have a pressure foot to press fabric during cutting.
Cutting machine specification (Automatic) :
Pattern developing, marker making, and cutting are done fully automatic system. Cutting is done by computerize straight knife cutting m/c
Fig: Automatic Cutting M/C
Vector MAX Fashion m/c specification: Computerize straight knife cutting m/c. ( For Example )
Brand :Lectra
Origin :France
Softer :Pilot V1R1
Blade :
- width: 2.4cm
- Length: 8.5cm
- Model: Lectra HQ F8301 (MR6, MH, MX m/c
Blade sharper:
- Max sharing belt.
- Duration: 1pair 1hr
- Sharpe distance: (2.5—3cm) depend on ply height.
Cutting speed:
- Max 100m/min then min 10m/min (normal fabric, s/j, d/j, finely, fleece)
- Max 20m/min then min 2/m/min (critical fabric, Lycra, rib)
Vacuum pressure:
- (0—100) mbar
- 30mbar—–low ply&GSM
- 70, 80, 100mbar —- higher ply &GSM
Max cutting width: 85”
{Note: -180-220GSM:-120ply may cut
-20-above 90:-100 ply may cut
-Fleece 300 GSM:-60—70 ply may cut}
Vector VT 7000 Fashion m/c specification:
Computerize straight knife cutting m/c. ( For Example )
Brand : Lectra
Origin : French
Softer : Vector Pilot
Blade :
- width: 2.4cm
- Length: 8.5cm
Cutting speed : 50m/min & 100m/min (2 point fix)
Vacuum pressure : (50-100)mbar
Blade sharper : Grande stone (3 pcs) stone change one by one,
Blade duration : 3 day
Note:
- cutting speed 30m/min for s/j
- cutting speed 20m/min for s/j lycra
- cutting speed 15m/min for Fleece + Terry}
Organogram of a typical cutting section :
(685)