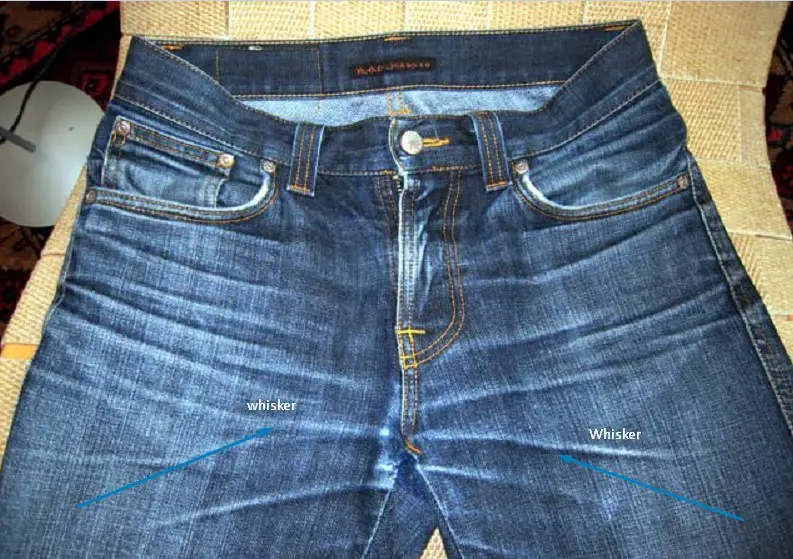
Denim Dry Processes – Whiskering , Laser Whiskering , Hand Scraping, Grinding, Destroy, 3D Crinkle
Denim Dry Processes – Whiskering , Laser Whiskering , Hand Scraping, Grinding, Destroy, Overall Crinkle , 3D Crinkle
Denim Dry Processes :
Denim dry process comes before wet process and it changes the visual appearance by mechanical abrasion without altering the construction and properties. The garment gets a nice look after dry process and also it adds value to the product. Fashionable garments are produced by the dry process.
Process sequence of denim dry process is given below :
Process sequence of denim dry process
Raw Garments
Whiskering
Hand Scraping
Tagging
Washing → Normal , Enzyme & Acid wash etc
Hydro-extracting
Drying
Destroy
P.P. Spray
Grinding
Washing Neutralization
Softening
Hydro-extraction
Drying
Finishing
Machines / Apparatus used in Denim Dry process :
- Abrasive paper
- Hand Scraping machine
- Whiskering pattern
- Grinding machine
- Destroying machine
- 3D Crinkle machine
- Normal Crinkle machine
- Pen grinding machine
- Tagging machine
- Oven dryer
- Heat setting machine
- Conveyer oven
- P. Spray Cabin
- Sprayer
- Laser machine
- Ozone washing machine
- Crown heat gun
- Air dummy – horizontal
- Air dummy – vertical
- Tie ( Net, Socks , Rope , Cable etc. )
- Chalk
- Pensil
- Rotating Brush
- Quality table with light box etc.
Different dry processes :
1 . Whiskering : Whiskering is the first process and one of the most important process in denim dry process. Different whiskering pattern is developed according to the design and the garment is scrabbed over the prepared pattern with abrasive paper or emery paper to get the whiskered effect or fading effect.
Whisker can be made in different ways. But the top most ways are as follows.
- By whiskering pattern
- By Manual hand scrap.
- By using laser Machine.
A . By whiskering pattern : Different process can be used to make whiskering pattern . One process is given below :
- At first the design is selected then a white poly is placed on the the garment.
- Marking the design with marker with seam line
- Taking a rubber board and replace the marked poly on the rubber board
- Engaving the marked rubber board area of whiskering by cutter or blade
- Whiskering pattern is made
- The pattern then inserted into the denim garments
- Scrape over the engraved area and the whiskered design is created.
After making the whiskering pattern , the board is placed inside the denim garments and the emery paper or abrasive paper is scrabbed over the engraved pattern.
B . Manual Hand Scraping : Manual process is also used to bring the whiskering pattern design on the denim garments. Apparatus is used for hand scraping is given below :
- Pattern
- Emeri paper or abrasive paper
- Chalk powder
- P – 400 ( very rough surface for hard fabric )
- P – 800 ( medium rough surface for medium hard fabric )
- P – 1000 ( less rough surface for soft fabric )
As the number increases the power of abrasive paper decreases.
Manual hand scraping process is given below :
- First the design is observed then draw the design with a chalk on the denim garments carefully
- Scrape on the drawn line of the design by the abrasive paper thus the design is created.
C . Using Laser Machine : Laser machine is used to make whiskering or burning effect on the denim garments. This process is done after the washing process. Different intensity of light is used to get the desired design. Laser is produced by the combination of co2 and DC current.
The process is given below :
- First, the whiskering design is made by photoshop or illustrator
- Design is transferred to laser machine
- The intensity of laser light is selected
- Laser light is imposed on the denim garments to get the design
- After the wash the burned indigo is removed and the whisker is visible
Operating flow path of Easy mark supervisor software is given below :
Open —> Import image —> Open file for insert diagram —> Image Size —> Selection —> Tools —> Pointer Online —> Pointer Online off —> Print.
Configure —> Advance Configure —> Enable Automatic Selection —> Ok.
Configure —> Massage Table —> Add (front right, back right, front back right) —> After Adding OK —> Print.
Laser whiskering is done by this processes.
2 . Hand Scraping / Sanding : This dry process is applied after whiskering to remove the color or fade specific area of the garments and become very important now a days. Abrasive paper , Air dummy ( horizontal ) , gum tape and Hand is used . This process is more used as sand blasting process is banned due to hazadous to health.Hand scraping process is given below :
- First the garments is mounted on the air dummy and fitted into two M.S. pipe
- Both end of each pipe covered with rubber tube and tightened by suitable clamping
- After inserting the garments then the dummy is filled with compressed air as per required pressure
- While scraping with hand , Pressure should be uniform
- Then sent to washing to get the desired efffect
3 . Grinding : Grinding is the destruction of edges or the worn out effect on the edge of the garments. If the garments has two time wash that time we will wash it after first wash to avoid the damages of garments. It is often done on hem, pocket edge, west belt , pocket opening and pocket pluf of the garments. It brings old look appearance and creates high fashion garments. Grinding machine is used to destroy the edges . For grinding small size stones are used in the grinding machine.
4 . Destroy : Destroy is the most popular distressing method which is done by pen grinding machine with different size stones. It look like holes and worn out white yarns which make garments unique and fashionable.
Different types of apparatus and requirements :
- Grinding machine
- Grinding wheel
- Different size stones
- Niddle
- Knife
- Electricity
- Safety accessories
Destroy process by grinding machine :
- First mark the place to be destroyed by the grinding machine
- Slightly attach the machine with the garment and slowly remove the cellulose
- After washing it will get the desired effect
Destroy process by niddle and knife :
- This is manually done by cutting the warp yarn or making holes by knife
- Having 3-5 small holes are enough but too many holes are not preffered
- Keeping the weft yarn to show the white thread
- Knife is run along the warp direction 10 times or more in a certain area
- The area around the destruction done is worn out
- After wash it will show the desired effect
After the destroying process the white yarn losses strength and to strengthen those yarns acetic si-sealant could be used which may prevent the breakout and tearing of those yarns.
Or , To reinforce the newly created holes , turn the garment inside out and place and adequate patch or cut piece of fabric around it and sew it
Safety measurements are taken during the destroy process by wearing masks and gloves.
5. Overall Crinkle : The full garments is washed with resin and after hydro-extacting the full garments is dryed then special effect is produced. For the effect , the garment is tied with thread or net or rope which resin treatment. Overall crinkle is done the all types of fabrics like denim , twill , canvas , poplin , knit , viscose , nylon etc. This is done after all types of dry and wet process. This is very popular and widely used in denims now a days.
Resin solution prepared :
- Resin 20%
- Water 80%
Machine / Apparatus / Requirements for overall crinkle process :
- Washing machine
- Trolley
- Hydroextractor
- Curing machine
- Tie , rope , thread
Overall Crinkle process is given below :
- Garments are tied with rope, tie , thread
- Then, garments are loaded into the washing machine with solution
- Let, temparature is 50 oc and keep the machine running for 10-15 minutes.
- Then , unload the garments from washing machine to trolley and start hydroextracting
- Untie or cut the threads, ropes
- Put those garments into curing machine and set the machine at 140- 160 oc for 40-60 minutes
- When the time exceeds , machine automatically becomes off
- Then , all the garments are hanged by hanger for 10-15 minutes for cooling
After those processes the garments are checked for quality and delivered.
6 . 3D Crinkle : It is one of the important finishing treatment on denim garment which is applied after wet process. Bringing 3D effect on denim garments by treating with resins are called 3D crinkle. This process is done manually or semi autometically using resins like low formaldihyde or DMDHEU type resins which make crosslinks between cellulosic bonds and when the fabric deforms or folds or losses its normal orientation , those chemicals prevents the transformation to normal position and that causes wrinkles or creases. Various supporting auxilliaries are used for better penetration of resins and softeners used for softness.
Techniques for 3D Crinkle finish :
- By 3D crinkle machine
- By Heat setting machine
- By Spray and chemical application cabinet with conveyer
- By 3D wire crinkle machine
- By 3D bendable leg or air dummy
- By using clip
- By garment crushing machine
- By tying garments with air
Solution :
- Water
- Resin
- Supporting auxilliaries
Control parameters :
- Temparature
- Time
- Concentration of solution
The process of 3D crinkle is given below :
By 3D crinkle machine :
- The machine consist of 6 heads and changeable leg distance .
- Both legs can work simultanously.
- It requires no chemicals for crinkle effect on denim.
By Heat setting machine :
- This machine give permanent creases
- First , spraying resins on specific area of the garments
- Then , pressing with heat bring permanent crease in the garments.
By Spray and chemical application cabinet with conveyer :
- First , the resin solution is sprayed on the garments where needed
- Then , cliping the area to get desired effect
- Sending those garment into the chemical application cabinet
- This cabinet has specific temparature for curing , normally 140-160 oc
- A converyer belt moves all the garments to the initial position to final position
- Time is given when it is needed to be off
- This machine operates automatically after giving instruction
By 3D wire crinkle machine:
- There are 3 operation heads and 3 stations.
- The operation time is around 30 seconds.
- 1 person can control and work with this machine.
- Desired effect can be easily and quickly made by this sytem
By 3D bendable leg :
- This machine consist 1 head and 1 hanger
- It brings crinkle effect only using air
- It gives natural crinkle effect on denim
By using clip :
- First , resin is sprayed on garments
- Then, the area is folded or creased by clip
- Finally , the garment is sent to the oven for curing
By garments Crushing machine :
- It a crushing machine of steam system which brings creases all over the garments
- Effects can be adjusted using steam , pressure level and chemical level
By tying with thread :
- First , garments is soaked into resin solution
- Then , thread is used to bend or fold or pleat where effect is desired
- Finally , garments sent to oven for curing
Precautions for 3D crinkle effect when resin is applied :
- If more resin is applied in a specific area , the garment may tear
- If resin applied more than one time , garment may tear
- If oven time is more , tear can occur
- If exposure time is more, tear may occur
- For more resins , garments can be so hard
- Unwanted spots can appear
- If more resin applied in pocket area ,then pocket may damage
Denim Dry Processes part 2 – P.P. Spray, Tagging, Ozone wash
(15408)