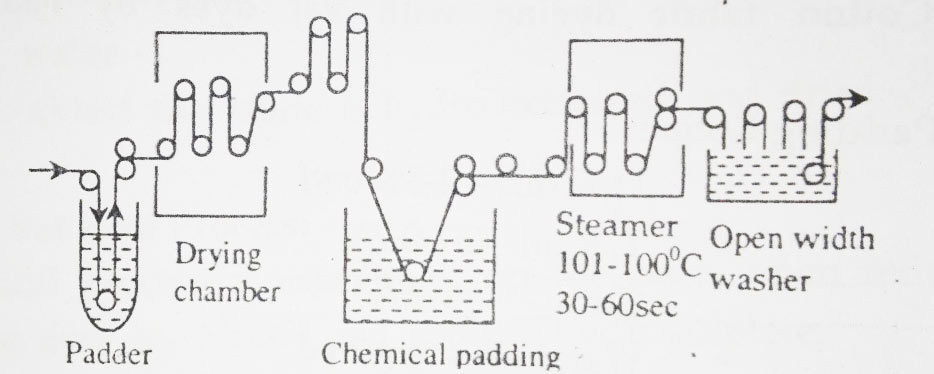
Dyeing Auxiliaries | Function of Auxiliaries | Dyeing Method of Vat Dye | part 02
Dyeing Auxiliaries :
- Sodium dithionite, thiourea dioxide and sulphoxilic acid derivatives as reducing agents
- Caustic soda used as solubilising agent
- Sodium sulphate, or Sodium Chloride used as electrolyte
- Polyacrylates and alginates as anti-migration agents in padding processes
- Formaldehyde condensation products with naphthalenesulphonic acid and ligninsulphonates as dispersing agents
- surfactants (including ethoxylated fatty amines) and other components such as betaines, polyalkylenamines, polyvinylpyrrolidone as levelling agents
- Hydrogen peroxide, perborate, 3-nitrobenzenesulphonic acid as oxidants
- soap.
Function of auxiliaries:
Reducing agent
- Sodium dithionite Na2S2O4.2H2O. generally it is called hydrosulphite or hydrose. It is used as reducing agent.
- It turns the insoluble dye to produce weak acidic leuco form.
- It is sensitive to atmospheric oxygen.
- It decompose during vatting & dyeing.
- Decomposition increases with temperature.
Na2S2O4 +H2O 2NaHSO3+ 2[H]
Limits of sodium dithionite
- Sodium dithionite is consumed by reduction of the dye and also by reaction with atmospheric oxygen, therefore an excess of reducing agent has to be used and various techniques have been proposed to reduce these losses.
- In addition sodium dithionite cannot be used for high temperature or pad-steam dyeing processes because over-reduction can occur
Alkyli
- NaOH is used as a solubilising agent.
- Salt produced by neutralizing their hydroxide to give a water soluble product.
- Maintain reduced dye in water soluble form.
Electrolyte
- Most commonly NaCl OR Na2SO4 is used.
- They help dye exhution.
Wetting agent
- Helps in wetting of fabric during dyeing
- Assist dye penetration.
Anionic detergent
- It is used during soaping.
- It helps to remove unfixed dye from the surface.
Fastness:
The wash fastness rating of vat dyes is about 4 – 5 .The excellent wash fastness of textile material. Vat dyes molecule as well as its aqueous insolubility. The large vat dye molecule is trapped within the polymer system of the fiber because of its size and aqueous insolubility and it is absorbed within the fiber system by van-dar- wals forces. Fastness to light & washing is excellent but poor rubbing fastness.
Trade name |
Company |
Country |
Artex vat |
Rainbow Texdyes CO |
India |
Benzanthrene |
Chemiequip ltd |
India |
Calconoid |
American Cyanamid Co |
USA |
Cibanone |
ICI |
UK |
Indanthrene |
Farbenfabriken Bayer AG |
Germany |
Meta vat |
Universal Dyestuff Indus |
India |
Caledon |
ICI |
UK |
Sandothrene |
Francolor |
France |
Dyeing method of vat dye:
Pre-Pigmentation Dyeing Methods
The pigment form, however, has no substantivity for cotton at all. The pre-pigmentation dyeing methods are simple processes in which a fine dispersion of the vat pigment is uniformly circulated through the goods that are then treated with alkaline hydros solution to cause reduction.
Dyeing takes place around each original pigment particle with almost no migration. The dyeing is subsequently oxidised and soaped as before. Either of the two operations, the initial pigmentation or the reduction, may be batch or continuous processes. This leads to a variety of possible dyeing methods, some of which are described below.
1. Pre- and semi-pigmentation batch dyeing methods
In the pre-pigmentation method, a fine dispersion of the vat dye pigment is first circulated through the goods.
In the second step, reduction to the leuco dye is carried out using NaOH and hydros.The latter may be added all at once or gradually.
This method is useful for light and medium shades where levelling and penetration may be a problem in dyeing with a fully reduced vat dye. It is, however, less suitable for compact forms of material.
In package dyeing, the pigment dispersion must not be filtered out in the packages but rather gradually deposited into the package by salt addition that causes the particles to slowly flocculate.
In the semi-pigmentation process, all the chemicals are circulated through the goods at room temperature before gradual heating to start reduction. The rate of vatting is very slow at the low starting temperature.
As in the pre-pigmentation method, a fine dispersion is required. The vat acid process is another alternative for package dyeing. After reduction of the vat pigment, in alkaline solution, the leuco vat acid is precipitated in the presence of a dispersing agent by acidification. This is then circulated in the goods and dyeing takes place by gradual addition of caustic soda to reform the soluble and substantive leuco form.
2. Semi-continuous processes
In semi-continuous vat dyeing processes, the fabric is pigmented by padding with the insoluble vat dye dispersion. Subsequent reduction to the leuco form is a batch operation using a jig or beam dyeing machine.
Some dye comes off the fabric during development with the alkaline hydros solution and some vatted dye liquor may be added to the bath in the machine beforehand. This prevents ending in jig dyeing. In some cases, an intermediate drying of the padded fabric may be included to minimise colour bleeding into the development bath.
3. The fully continuous pad–steam process
The pad–steam process for dyeing cellulosic materials with vat dyes is a particularly important process. It involves five stages:
- padding the fabric with the fine vat pigment dispersion containing a wetting and an anti-migration agent;
- drying of the padded fabric and cooling;
- padding of the dried, pigmented fabric with hydros and caustic soda solution;
- steaming in air-free steam at about 102–105 °C;
- rinsing, oxidation and soaping using a series of wash boxes.
Liquid forms of vat dyes are preferred for continuous dyeing as they give less migration on drying and are more convenient for preparing the large volumes of dye liquor required. The drying of the fabric after padding ensures a high pick-up of alkaline hydros solution from the chemical pad. Some dye invariably bleeds from the fabric into the alkaline hydros solution. This is less when padding a dried fabric, and an initial addition of some dye to the chemical pad solution minimises colour tailing.
Drying of the initially padded fabric is usually carried out in two steps involving a gentle pre-drying stage before the complete drying process. Predrying is to control migration of the pigment particles to the yarn surfaces where water is evaporating. The heating should be as uniform as possible.
It is also common practice to use an anti-migrant such as sodium alginate in the first padding solution. The anti-migrant causes flocculation and aggregation of pigment particles during drying thus limiting their movement within the fabric. Some anti migrant agents may also increase the solution viscosity. The ease of migration depends on the fibres and fabric, the solution pick-up and the pigment particle size
After the chemical pad, the fabric is steamed for 30–60 s in saturated, slightly superheated, air-free steam.It is essential to avoid condensation falling onto the fabric in the steamer as this causes a spotty colour. The steamer has a water seal at its exit with water flowing through the trough to maintain a temperature of not more than 40 °C.
After steaming the fabric is rinsed by spraying to remove alkali and hydros. This is followed by rinsing, oxidation, soaping, rinsing and neutralising in a series of wash boxes.
4. Wet-on-wet processing
The usual pad–steam process cannot be used for corduroy or terry cloth because of flattening of the pile and excessive migration during drying. A wet-on-wet dyeing process is used.
In this, the cloth is padded with the pigment dispersion and then, while still wet, it is padded again with the alkaline hydros solution. The solution pick-up at the chemical pad may go from values of around 70 up to 150–200%. The goods then go through the steamer and the usual aftertreatments.
Cotton fabric dye with vat dyes by pad-steam or continuous method
Pad steam process is a continuous process of vat dyeing . it is applied in large quantity of fabric. It is done in 2 machine
1.Pad thermosol
2.Chemical pad steam.
- At first fabric is padded in pad thermosol with vat pigment dispersion.
- Then it is dried & padded again in chemical pad steam with redusing liquor containing Na2S2O4.2H2O, NaOH, soda ash & glouber salt, dye is reduced by this chemicals.
- Then fabric is passed through the steam chamber for 30-60s for fixation.
- Then washed with detergent & lastly with acectic acid for neutralization.
Recipe
- Vat dye X%
- Hydrose 100g/L
- Caustic 80g/L
- Soda ash 20 g/L
- Salt 250g/L
Fig: Pad Steam Dyeing Method
(2903)