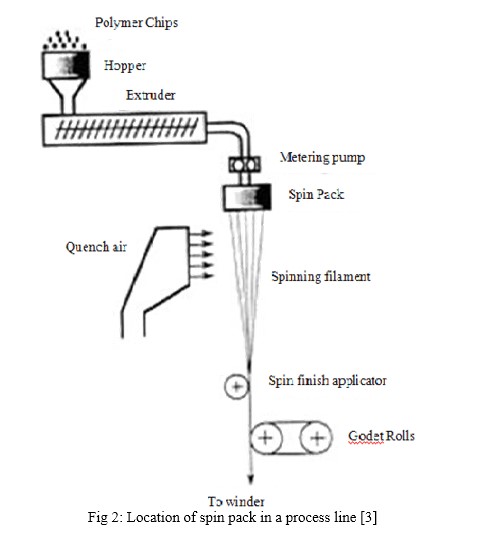
A Techno Commercial Study of Re-cycling of Metallic Powder Used in Polyester Industry as a Polymer Filtration Media
A Techno Commercial Study of Re-cycling of Metallic Powder Used in Polyester Industry as a Polymer Filtration Media
Dr. S. S. Bhattacharya1, D.K. Sullere2, R.K Dubey3
Professor, Textile Engg. Dept, Faculty of Engineering & Technology, M.S. university , Vadodara, Gujarat, India1.
M.Text, MBA, Principal, M.S. Polytechnic, Surat, Gujarat, India2
M.Text., General Manager Poy (C.P.Division), Garden Silk Mills Surat3
Abstract : Now a day’s recycling or reclamation of metallic powder becomes a necessity to make it more economically viable, reducing concerns over availability of virgin powder and elimination of disposal into landfills with associated regulatory issues. By operating an efficient and effective reclamation process, metallic powder can successfully be removed from polymer-encapsulated plugs for re-use without affecting the quality of the metal product and also it provides an environmentally responsible solution to disposal.
Keywords : Metallic powder, Spin pack, Spinneret, Metering pump, Quench air, Spin finish applicator.
A . INTRODUCTION
Spin pack is the heart of melt spinning process, in spin pack preparation, spinneret, distributor woven wire mesh and metal powder of various sizes (125 to 1000 microns) are used. The metal powder is used for filtration of polymer, shearing of gels etc. The metal powder is a costly consumable and its disposal is also becoming an environmental issue. This paper deals with technology and quality assurance of metal powder recycling.
Metallic Powder can be used as a filtration medium in the production of polyester and nylon fibre used in industries such as textile & carpet manufacturing. Reclamation process that successfully removes polyester and nylon from polymer-encapsulated metallic powder plugs provides the user improved product economics along with the creation of a sustainable process that eliminates landfill disposal. A successful reclamation process effectively cleans and puts the reclaimed metal into the desired specification for the user without adversely affecting the metal particles. This report discusses the benefits and process of metal reclamation. Each year, a typical polyester filament plant of south Gujarat producing 500 Metric tons per day may use as much as 19.8 Metric Tons of metal powder at a cost of 650 Rs/Kg costing Rs. 11.2 million, which is a substantial amount. The cost details of typical recycling process are given below.
It is forecasted that global polyester fibre market to grow by 8%[1] annually, particularly in India and China, since the majority of polyester fibre producers use metallic powder in their processes, a similar growth will become apparent for Metallic Powder. Unless reclamation processes are put into place, the resulting polymer encapsulated plugs of Metallic Powder are then destined to be land filled.
Metallic Powder, glass beads, sand, and screens are typical filtration media used in the production of synthetic fibre. Synthetic fibres are used in the production of textiles, carpets, tire cord, and a variety of other applications. The selected filtration medium or combination of media is put into a spin pack in some sort of configuration depending on the pack design the spin pack is then put into the user’s process line where molten polymer is allowed to flow through the spin pack and procedure fibre.
TABLE 1
S.S. POWDER CLEANING COST (80KG BATCH) |
|
|||||
SR NO. |
CONSUMABLE ITEMS |
UNIT |
RATE (Rs) |
REQUIREMENT(No.) |
TOTAL (Rs.) |
REMARKS |
1 |
CAUSTIC COST |
RS /KG |
26.00 |
4 Kg |
104 |
|
2 |
NITRIC ACID COST |
RS / KG |
19.00 |
4 Kg. |
76 |
|
4 |
POWER COST |
RS / UNIT |
6.00 |
630 Units |
3780 |
REFER ANNEXURE – 1 |
5 |
STEAM* |
RS / KG |
0.15 |
1800 Kg. |
270 |
REFER ANNEXURE – 2 |
8 |
D.M. WATER |
RS / M3 |
31.20 |
14.4m3 |
449 |
REFER ANNEXURE – 2 |
9 |
MANPOWER COST |
RS / PERSON |
500.00 |
3 No. |
1500 |
|
TOTAL COST |
6,179 |
|
||||
COST / KG |
77.23 |
|
*Steam from waste heat recovery boiler.
Details of the cost (shown in table 1) of chemicals, steam, D.M. water, units of power consumed and man power cost to recycles the batch size of 80Kg used metallic powder. Individual details are given in ANNEXURE – 1 and ANNEXURE – 2.
TABLE 2
ANNEXURE – 1 |
|||||
SR NO. |
EQUIPMENT DESCRIPTION |
CAPACITY IN KW |
ACTUAL POWER CONS. IN KW/H |
RUNNING IN HOURS |
TOTAL POWER CONS. IN KW/H |
1 |
HEATER(PACK FURNACE) |
60 |
45.00 |
12 |
540 |
2 |
EXHAUST BLOWER |
0.75 |
0.56 |
12 |
7 |
3 |
CIRCU. FAN MOTOR |
1.5 |
1.13 |
12 |
14 |
2 |
CONE DRYER MOTOR |
5.63 |
4.22 |
12 |
51 |
3 |
VIBRO SIEVE – 1 |
0.75 |
0.56 |
8 |
5 |
4 |
VIBRO SIEVE – 2 |
0.75 |
0.56 |
8 |
5 |
5 |
CIRCULATION PUMP |
1.13 |
0.85 |
12 |
10 |
|
TOTAL |
|
|
|
630 |
Details of power consumed (KW/H in table no 2, ANNEXURE 1) of Furnace, Exhaust blower, Circulation fan, Cone dryer, Sieve 1, Sieve 2 & Circulation pump to recycle a batch of 80Kg. Used metallic powder.
TABLE 3
ANNEXURE – 2 |
|||||
SR NO. |
EQUIPMENT DESCRIPTION |
CAPACITY |
ACTUAL CONS. |
RUNNING IN HOURS |
TOTAL CONS. |
1 |
STEAM |
350 Kg/HRS. |
150 Kg/HRS. |
12 |
1800 Kg. |
2 |
D.M. WATER |
1200 LTR/H |
1200 Kg/HRS. |
12 |
14,400 litres |
Details of the consumption of a steam in Kg and D.M. water in litres (shown in table no 3, ANNEXURE 2) to re-cycle a batch side of 80Kg of used metallic powder.
After use, the spin pack is disassembled for cleaning, whereby the polymer-encapsulated filtration medium is deposed of and replaced with virgin material. Sources of metallic Powder have historically been from global virgin metal suppliers who have proprietary processes, such as atomization, to convert base metal into metal powder. As the international market for mined metals fluctuates, so does the availability and pricing for the distribution and sale of metallic Powder.
Global economics and environmental mandates have begun to push manufacturing sites toward greener processes and reclamation instead of disposal. There are end-users who have in-house solvent and burnout processes to reclaim metal internal to their facility; however, reclamation using solvent chemistries produces waste water and waste solvent streams contaminated with metal that must be land filled, incinerated, or treated. Burnout processes alone do not provide clean metal and can also offer air emission and waste metal fines problems.
Some leading spinners have developed a non-destructive, effective, and environmentally responsible reclamation process for metallic powder. In the following sections, the reclamation and testing processes are described, along with basic fundamentals of why metallic powder is the filtration of choice for many fibre producers.
B . METHODOLOGY
In the reclamation, process, polymer-encapsulated metallic powder plugs from spinning equipment are placed on racks in ovens equipped with specialty temperature controls and after-burner exhaust features. The racks are designed to separate components of the plug during the heating process. Afterwards, bulk metal from depolymerised plugs goes through a washing/drying process including acid and alkali treatment followed by separation of metallic and non-metallic components. Once a cleaned stream of metal is produced, it goes through a sieving process to control particle size distribution per the users’ specifications. When the sieved metallic powder has been collected, samples per lot are tested to produce a test report. The report values must fall within the specifications for that grade of metal.
Tests used for reclaimed metal are the same as those used for virgin metal:
- % Carbon
To determine % carbon, the tare weight of sample of reclaimed metal is processed in an oven at 483 degree Celsius for 20 minutes. After cooling, the post-oven tare weight is determined and the % carbon calculated:
- Apparent Density
Apparent density is an indicator of void volume in a sample of metal. The apparent density is the value determined by Equation 2 when weighing a container of known volume that has been filled with metal powder. The device used to measure apparent density consists of a container of known volume and a special orifice that controls the flow of metal into the container so that “metal packing” is prevented.
AD=W/V ……… (Equation 2)
Where, AD = apparent density (g/cc), W = tare weight of metal, V = volume of the container.
- Sieve Analysis (Table 2)
The sieve analysis is determined by using a rotap equipped with proper screens for the specific grade of metal and the user’s specification. Once a sample of reclaimed metal has been processed through the rotap screens, the weight of metal captured on each screen is weighted and compared to the user’s specification.
The above shown machine is used to give chemical treatment and washing of used metallic powder. After properly drying this powder, the lot is transferred in a hopper below which sieving assembly is placed for proper size wise segregation of reclaim metallic powder ready for use against virgin metallic powder.
Homemade sieving machine on which segregation of reclaimed metallic powder is processed
TABLE 4 : Sieve Analysis [4]
Specification: |
Grade 30/60 |
|
Test report |
Mesh |
%Metal |
Mesh |
% Metal |
+30 |
<10% |
+30 |
4.59% |
+60 |
Bal |
+60 |
87.20% |
-60 |
<15% |
-60 |
8.12% |
-100 |
<1% |
-100 |
0.06% |
-325 |
Trace |
-325 |
0.03% |
|
|
Total |
100% |
AD |
1.60-2.00 |
AD |
1.72 |
%C |
0% |
%C |
0% |
C . DISCUSSION
Metal reclamation provides ‘a sustainable option’ for users greatly reducing concerns over the availability of virgin powder and the associated rising costs. Instead, the users can depend on the availability of metal and long-term pricing stability.
In terms of “re-usability” and sustainability, users report:
- The same or improved on-line performance
- Elimination of disposal into landfills
- Elimination of regulatory issues associated with land filling
- Competitive edge due to realized savings between the reclaimed and virgin metal. The reclamation process itself is environmentally responsible in terms of:
– Energy-use for reclamation – Per pound of metal reclaimed, energy usage is less than 7.8 kilowatts/Kg .
– Solid waste disposal/land filling is almost eliminated.
Recycling of shipping containers – Users will return empty shipping containers to be used for future shipments. In general, approximately 5 shipments/ container are possible before discarding the container or using it for other purposes. Recycling plastic-shipping containers also reduces the amount of material going to landfills.
Minimization of wastes going to landfill – Reclaimed Metallic Powder yields are -96% per batch of cleaned metal. As a result, reclamation eliminates land filling 100% of polymer and 96% of the Metallic Powder. The residual 4% of metal that cannot be reclaimed is generally metal fines due to attrition; however, other uses for the fines are being researched.
For the users’ process parameters, reclaimed metal must meet or exceed the on-line performance of virgin metal. To ensure a quality product, important characteristics of any grade of metal must be considered, such as:
- Metallurgy[2] – The user’s process conditions determine the metallurgical needs of the metal. For example, a high nickel content P-270 grade is more resistant to oxidation that a standard DPI grade [5]. As a result, when reclaiming a wide variety of in-coming metal streams, attention to metallurgy is important so as to not mix metals of similar grades but different metallurgies.
- Characteristics of metal edges[2] – The more irregularities and sharp edges on metal particles, the less packing that will result among the metal particles and the more void spacing will result. The amount of sharp edges also relates to the ability of the metal to lock when loaded and pressed into the spin pack. In terms of filtration, the sharp edges are important in removing gels and other contaminants
- Metal fines – A quantifiable small amounts of metal particles outside of the specified grade can lead to plugged spinneret capillaries and a difference in the filtration level of the pack. During the sieving part of the process, it is extremely important to determine the proper combination of screens and screening techniques to ensure the metal powder is put into proper specification with minimal fines.
- Cleanliness – Reclaimed metal should be free of carbon and organics. The removal of inorganic is important to reduce contamination issues.
- Specifications – A user desires metal that meets the specification of their filtration needs. When reclaiming Metallic Powder, it is extremely important to understand and use the proper sieving technology and techniques. Incorrect particle separation can produce quality and on-stream life process issues.
D . CASE STUDIES
A polyester fibre producer recently began using reclaimed Metallic Powder. Initial trials revealed no adverse process effects of reclaimed metal vs. virgin metal. After 12 months of using reclaimed metal, the on-stream performance is the same as virgin; however, there has been a savings of 11.2 million rupees on account of metal powder purchase and an additional savings on landfill disposal of 0.4 million rupees of polymer-encapsulated metal plugs.
Technical manager of the producer noted the following:
“We have been testing the reclaimed metal against the virgin metal that we use on a routine basis. All testing thus far confirms that the reclaimed metal meets all the standards for filtration and distribution as the virgin metal currently being used. The results of the fabric made with virgin and reclaimed metal was checked and found no difference. Management has accepted our proposal for implementing the use of reclaimed metal on a routine basis. Everything looks good so far and we fully expect to be able to take advantage of the cost savings and reducing impact on the environment.”
A polyester producer was required to dispose of the polymer-encapsulated Metallic Powder plugs as hazardous waste because of the Cr and Ni content in the metal. As a result, not only did the disposal costs increase but the additional waste- stream threatened to change the user’s waste generator status. Being able to reclaim the metal resulted in not only savings on disposal costs but kept the site from becoming a large quantity hazardous waste generator.
E . CONCLUSION
When operating an efficient and effective reclamation process, Metallic Powder can successfully be removed from polymer-encapsulated plugs for re-use without affecting the quality of the metal product.
Metallic Powder can be reclaimed utilizing various methods of de-polymerization, separating, and sieving. Reclamation process produces a product that:
- Has a lower concentration of fines as compared to virgin material
- Is more economical than virgin material
- Provides an environmentally responsible solution to disposal
REFERENCES
[2] Hoganas, “Stainless Steel Powders for Hot Polymer Filtration”, March 2010.
[3] Manufacutred fibre technology edited by V B gupta & VK Kothari edition 1997
[4] Ametec Tech. Briefs, Metal Powder Technology, AmetipTM Processed Polymer Filter Powders
[5] Morgan Campbell, “Reclamation of Metallic Powder Used in Filtration Applications”, AFS Conference, March 2011.
(1626)