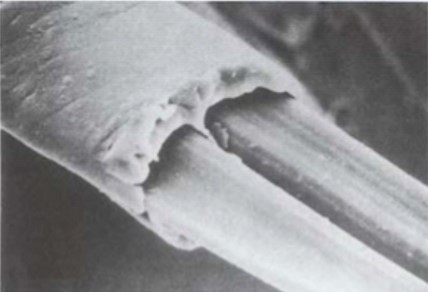
Degumming of Silk
Degumming of Silk
Objective :
Degumming or boiling-off is the process employed to remove the silk gum (sericin) enveloping the two raw silk threads (fibrion) . During the spinning process of silk by silkworms the two filaments are made into one by means of proteinious gummy substance called sericin.
The gum content of silk varies according to quality and origin. Bombyx mori or Mulbery silks have about 20-30% gum and Tussah 5-15%. The gum is not completely removed in every case. The extent of degumming gives rise to different varieties of silk . ‘Ecru silk’ (crude, bast silk) is rarely degummed, quite hard and without lustre. The degumming loss is maximum 4%, since mostly only grease, wax and resin substances are removed. This type of silk is mainly used as warp threads. ‘Half-boiled silk (souple, soft, matt silk) is partially degummed. The degumming loss is approximately 6-12%. ‘Cuite silk’ (lustre silk) with nearly 18-30% gum loss can be classified as a completely degummed variety with a soft handle and high lustre.
Apart from sericin, other impurities present in silk are lubricants and softeners added during throwing or in preparation for weaving or knitting, dirt and oils picked up incidentally during processing and undesirable natural colors. The component of fats and oils is around 0.5-1% and that of natural pigments 1.0-1.4%. During the degumming process soil, stain, oil and fats sticking to the material will also be removed. Thus degumming is synonymous with the scouring process normally used for the purification of cotton and wool. Silk warp is not subjected to sizing before weaving like cotton. However, grey silk fabric and its blended fabrics are subjected to singeing prior to degumming. Degumming can be carried out by physical or chemical means on silk in the form of hank and also on fabrics which are subsequently taken for dyeing. The choice of degumming conditions depends on the type of silk product (yam, twist, fabrics of different densities). Wild silk fabric is more difficult to degum than Mulbery silk. Tussah silk contains higher quantities of calcium salt. Loss in weight of silk by degumming process is also accompanied by a loss in strength of approximately 20%. The loss of weight and volume can be completely or partially compensated by the subsequent weighting process. Degumming is effected by careful treatment of silk with high pressure water, acids, alkalies, soaps and synthetic detergents. Chemical dissolution of sericin is obtained partly by hydrolysis and partly by dispersion, independent of the method used. Soap works mainly by dispersion whilst alkalies have a strong hydrolytic effect .
METHODS OF DEGUMMING :
Degumming of Silk in Water :
Cultivated varieties of silk can be degummed by extraction with water at 120 deg celcius for about 2 h and repeating the process three to four times. In this case degradation of silk is minimum, but use of pressure equipment is essential. However, some modification of the protein molecule does take place.
Degumming of Silk With Alkali and Acid :
Silk degumming in aqueous solutions of acids and alkalies is greatly influenced by pH and temperature. An alkaline reaction at a pH > 9 and acid reaction at pH < 2.5 ensure a rapid elimination of sericin completely after 30 min of treatment. The temperature should not exceed 95 deg celcius to avoid weakening of the fibre. The degree of hydrolysis of fibrion also depends on pH of the bath.
Degumming of Silk With Soap :
Degumming is effected by careful boiling-off in soap baths which should be slightly alkaline. The fibre is treated with soap solution to give a pH around 10.0 at 90-95 deg celcius for 1.5-2 h. In order to avoid lien soap deposits and resulting stains, the water should be properly softened. Sequestering agent may be added in the bath to correct the hardness of water. In case of white and delicate varieties a two bath method may be employed. The second degumming bath will consist of 50% quantity of soap taken for the first degumming bath and the duration of treatment may be divided equally between 40-45 min for each bath. Neutral soap like Merseille soap or olive oil soap have no degumming property as the free alkali present in them are very negligible. However, Merseille soap (8 g/l) can be used in presence of non-ionic tenside (fatty alcohol polyglycol ether) (1-3 g/l), polyphosphate (1-3 g/l) (for softening the water) and soda (1 g/l) at 95 deg celcius for 1-2 h with a material to liquor ratio of 1:30. Here also a two bath method can be resorted to. Non-ionic tenside accelerates the degumming process and facilitates rinsing out the soap. Tussah silk is usually prewetted with boiling water before degumming and then degummed in strong alkaline bath .
Drawbacks of Degumming with Soap :
The main drawbacks are soap is expensive, great quantity of soap is required and longer treatment time.
Degumming of Silk With Synthetic Detergents:
A large number of synthetic detergents are available in the market and their selection is very important particularly on the requirement of soft feel as that achieved with soap. Non-ionic product like nonyl phenol ethoxylated com- pound in the pH range of 11.2-11.5 for a treatment time of 40 min at 95 deg celcius is found to remove the gum and maintain the strength of the yarn .
Enzymatic Degumming of Silk :
Enzyme which can hydrolyze the sericin is classified as proteolytic enzymes . The proteolytic enzymes cleave the peptide/amide linkages and convert them into amino acid. Mainly there are three types of proteolytic enzymes such as zinc protease (e.g. carboxy peptidase A), serine protease (Chymotrypsin, Trypsin, Thrombin) and thiol protease (acts as cystine residue in the protein). The function of proteolytic enzymes in their degree of degumming depends on the pH of the bath and the optimum activity is found to be different at different pH for different enzymes. Usually enzymatic desizing of silk is a two stage process. In pre degumming stage, the cloth is treated with a solution containing soda-ash (1 g/l) at 95 deg celcius for 20 min at a liquor ratio of 30. In the second stage, further degumming is carried out by treatment in a solution containing protein enzyme (0.06-0.1 g/l), non-ionic detergent (1 g/l) for 30 min at 55 to 60 deg celcius .It is usually impossible to achieve full degumming of silk by enzymes. A short-time treatment in a third bath containing soda-ash or soap may be given for the removal of the remaining sericin.
Foam Degumming :
The degumming of silk can also be carried out by foam method. The silk skiens are subjected to the action of foam from a boiling soap bath. Skiens are actually hung above the soap solution and the foam action has a tendency to dissolve and eliminate sericin. This method, however, is not popularly adopted.
Partial Degumming of Silk :
Before partial degumming the silk is degreased in moderately warm (30-40 deg celcius) and slightly alkaline soap baths. The actual degumming is then taken place in a bath containing acid salts or acids. The sericin is not released as much in an acid medium as it is in a neutral or alkaline bath, thus only partial degumming results. Acid degumming has also a positive effect on the strength and handle. The actual degumming bath can have various compositions :
- – Sulphuric acid and magnesium sulphate,
- – Sulphuric acid and soap,
- – Sulphuric acid and tartar,
- – 4% strength soap solution,
- – NaHSO 3 solution.
Depending on the nature of silk, it is treated for 1-3 h at boiling temperature. The weight loss with half boiled silk lies in the range of 6-12% on the original raw weight.
Washing of Degummed Silk :
After boiling-off, the silk is thoroughly washed with lot of water at 50-60 deg celcius containing 1ml / 1 ammonia for 15-20 min. This is then followed by 1 to 2 cold rinsing baths. Half-boiled silk should not be subjected to hot soap baths and alkaline liquors over 30 deg celcius because this would act on the silk gum still present. Following washing and drying silk is given further mechanical treatment in the form of stretching, beating or glossing. Scroop is imparted to the silk fabric by treatment with 2-5 g/1 of 30% acetic acid at room temperature for 15-30 min. When silk is delivered in dyed condition, scrooping is done after dyeing. Both degumming and partial degumming are only suitable for reeled silk .
Comparative Assessment of Different Degumming Methods:
Given below is a table which shows comparative assessment of different degumming methods. Different methods have been evaluated on the basis of weight and strength loss after degumming. The values with soap have been taken as the basis. It can be seen that soap, alkali and acidic degumming give the highest gum removal. However, alkali and acid both cause significant strength loss which points to silk damage. On the other hand amines seem to be good at degumming as well as retaining strength. Enzymes while good at retaining strength are not able to remove the sericin very effectively. This is a limitation especially with fabrics where due to their large molecular size enzymes molecules are unable to enter the interstices of the fabric. Hence enzymatic degumming may be preferred for yarns rather than fabrics.
ASSESSMENT OF DEGUMMING:
The simplest method to assess degumming is based on weight loss. However, in this case initial rapid weight loss may be followed by attack on fibroin. UV absorption at 280 nm has also been used to assess extent of degumming. Absorption is due to tyrosine and tryptophan.
(2357)