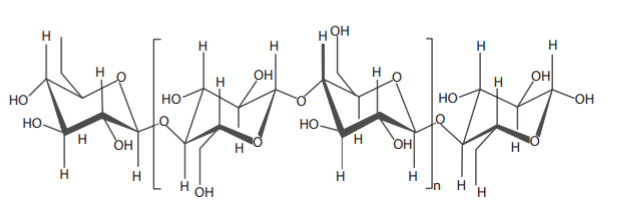
Introduction to Desizing of Warp Yarns
Introduction to Desizing of Warp Yarns
Desizing :
Desizing is the process in which the size applied to the warp yarn before weaving is removed to facilitate the penetration of dyes and chemicals in the subsequent wet processing operations. In the process of desizing, not only sizing agents, but also some natural impurities are eliminated from fibres. In desizing, the starches and polymers that are applied which are insoluble, are converted into water soluble compound to ease of their removal.
Methods of Desizing :
Desizing of cotton fabric can be accomplished by physical, chemical or combination of physical and chemical mechanism, namely rot steeping, acid steeping, treatment with enzyme and oxidising agents.
Rot Steeping :
In this method grey cotton fabric is steeped in water in suitable box at a temperature of about 30-40 oC. During the storage micro organisms develop excreting enzymes which attack the starch. The swollen and hydrolyzed starch is thus partially converted into soluble state which are then removed from the fabric by normal washing with water.
Acid Desizing :
In this method cotton fabric is treated with dilute sulfuric acid with a concentration of 5-10 g/1 at a temperature of about 40oC for 3-4 hrs. Dilute acid attacks the polymer chain of starch and due to chain cleavage of starch molecule short water soluble or dispersible chain segments are formed. The degraded starch is removed from the fabric by normal washing treatment.
Enzymatic Desizing :
Enzymes are organic bio catalysts highly specific both in the reaction catalyzed and choice of reactants. Physically enzymes are colloidal nature and chemically they are of the nature of protein. Enzymes are complex and have high molecular weights.
Enzymes are named after the compound they break down, for example, Amylase breaks down amylose and amylopectin, Maltase breaks down maltose and Cellulase breaks down cellulose. For desizing starch, amylase and maltase are used. Cellulase, on the other hand, is used for finishing cotton fabrics. This will be discussed in later chapters. Amylase will degrade starch into maltose, a water soluble disaccharide and Maltase will convert maltose into glucose, a simple sugar.
There are two types of amylase enzymes, Alpha and Beta. Alpha amylase attacks the chain at random points. The molecular weight of the starch is rapidly reduced facilitating complete removal. Beta amylase, on the other hand, starts at a chain end removing one maltose unit at a time. The molecular weight is gradually reduced thereby taking a longer time to complete breakdown. In addition, the action of beta amylase is stopped at the 1,6 branch glucosidic linkage found in amylopectin leaving relatively high molecular fractions.
Desizing with oxidising agents :
Sodium hypochlorite, sodium hypobromite and sodium or potassium persulfate will also degrade starch. The reaction opens anhydroglucose rings at the 2,3- hydroxyls, converting them into carboxylic acid groups. This method is not used much either because it too degrades cellulose fibers. Hypochlorite is used for bleaching however.
Evaluation of Desizing efficiency:
Identification of sizes :
Starches are hydrolysed by acids, alkalies or by enzymes during desizing process. Acid hydrolysis of starches yield mixtures of saccharides or glucose. Enzymatic (β-amylase) hydrolysis of starches yield maltose and amyloglucosidase yields D-glucose. All these products give different coloured residues on treatment with iodine. Because of the hydroxyl content of the cellulose, reaction can occur with many different compounds. Starch apparently contains two fractions, a soluble amylose (10-20%) and an insoluble residue, amylopectin (80- 90%), account for the violet colour and blue colour that are yielded on treatment with iodine. Amylose gives the blue colour and amylopectin gives the violet to red-violet colour.
In enzyme hydrolysis of starch, amylose is completely hydrolysed to amylase , whereas only 60% of amylopectin can be hydrolysed. Poor removal of size during desizing may effect in warp stripeness, stains during dyeing and printing, uneven mercerization and uneven absorbency.
Percentage of size by ordinary method :
The weighed cloth is first washed in water and then boiled in caustic soda solution (2%) for about 30 to 40 rain. The sample is washed again in water and boiled for 60 rain in a solution of hydrochloric acid (1%), adding water as it evaporates. The sample is washed, dried slowly and weighed. The difference in weight indicates the loss of sizing material. In normal practice allowance of 1 to 2% for weight lo88 by removing natural impurities is allowed during the boiling.
Estimation of total size by soxhlet method :
5 g of accurately weighed sample is extracted with chloroform in a Soxhlet extractor for about 1 hr at a minimum rate of 100 drops per min. The sample is then dried in air and washed in hot water several times and then rinsed by hand 12 times. The material is then treated in 0.5% diastase solution (20 to 30 times the weight of cotton) at 70~ for l hr and then washed in hot running water, dried at 110 deg and weighed. Side by side a sample is also tested for moisture determination.
a = dry weight of sample,
b = weight of desized sample, and
k = desizing blank
SIZES |
REAGENTS |
PROCRDURE |
REACTION |
NOTES |
Starch |
iodine/potassium iodide solution. |
1. apply solution dropwise, 2. rub in gently, 3. assess colour reaction.
|
Colourless = no starch , Blue violet = Starch present , Brown = modified starch or mixture with PVA present |
Cool material and test ; neutralise alkaline goods with acetic acid . |
Polyvinyl Alcohol (PVA)
|
Iodine/potassium Iodide solution , Boric acid solution |
1.apply iodine/potassium iodide solution dropwise 2.Apply boric acid solution dropwise to the same spot as the iodine/potassium iodide. |
Colourless = no PVA Blue = PVA present |
Colour intensity depends on amount of size. |
Polyvinyl acetate |
Iodine/potassium iodide solution. |
1.spot with iodine / potassium iodide solution . |
Deep reddish brown = polyvinyl acetate present ,
|
Colour intensity increase on hot washing . |
Starch+PVA |
Iodine/potassium iodide solution , borax . |
1.treated with warm water ( 70 deg cel ), 2.Aqueous extract is tested with iodine/borax. |
Blue solution or precipitate = PVA |
Colour intensity depends on PVA. |
CMC+ Acrylate |
Copper-2-sulphate solution |
1.cut up the sample. 2.Add water at ratio 40:1, 3.Boil up for 10 mins, 4.Filter off liquor and cool, 5.Add 5 drops solution to the liquor, 6.Assess reaction . |
Clear liquor = no CMC or acrylate present , White turbidity/precipitation = CMC or acrylate present .
|
Distinguish between CMC and acrylate by adding 2-3 drops acetic acid 80 % to the liquor, Reaction : precipitate dissolves = CMC, Precipitate undissolved = acrylate . |
In the absence of unsized control, k may be taken as 3% of the desized and dried sample. No correction is required for bleached and dyed cloth. For total size content the ash content (%) of the desized sample is to be added.
Assesment of starch size on desizing:
Category |
Extraction content (water extract ) |
TEGEWA Violet scale |
Grey state fabric |
6-10 % |
1 |
Pre-treatment , good |
0.1-0.4 % |
6-9 |
Pre-treatment , poor |
More than 0.5 % |
2-5 |
From the above table desizing efficiency will be estimated.
(1243)