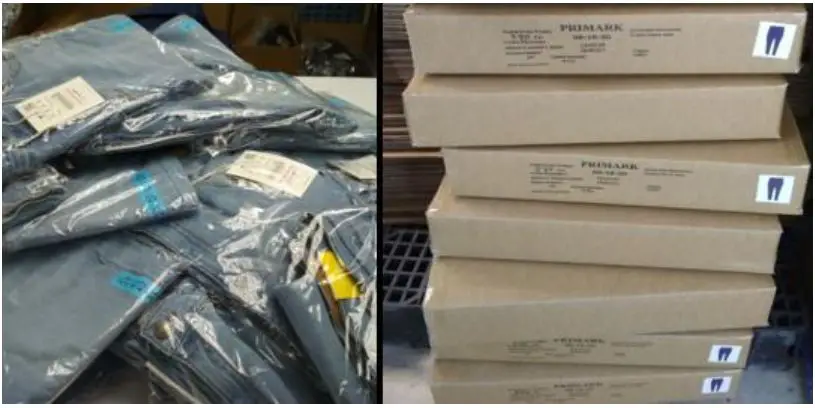
Garment Finishing | Pressing | Flow Chart of Garment Finishing
Garment Finishing | Pressing | Flow Chart of Garment Finishing | Equipment of Pressing | Folding | Types of Packing and Folding
Garment Finishing :
The finishing department is the department which comes after all the departments and it plays an equally important role in the final appearance of the garment. This department includes majorly of the following steps :
- Trimming
- Inspection
- Semi pressing
- Pressing
- Tagging
1 . Trimming: This involves the removal of the extra threads from the garment at the stitched areas.
2 . Inspection: The inspection carried out here is according to the AQL 2.5 system and sometimes it depends on the buyer also i.e., if the buyer emphasizes for a 100% inspection then the company has to do as specified.
3 . Semi pressing: This happens when a garment is difficult to inspect in the crushes manner as it comes from the washing department hence, they do a partial pressing for the garments and then inspect it and trim it and then send it to the complete pressing process.
4 . Pressing: The pressing is done after the garment has been completely inspected and the garments
are pressed on the basis of how they will be folded during packing.
5 . Tagging : Once the garments are been done with the inspection and complete pressing then they are sent for tagging the labels and the labels include the size labels, price tags and miscellaneous labels if any required by the buyer. Once the tagging is done the garments are folded according to the buyer’s specification.
The Principles of Pressing:
The process by which the unwanted creases and wrinkles are removed from the garments and the outlook of the garments is improved as well is termed as pressing. It is also known as ironing. In garments industries there is a separate section for ironing the products.It is generally done by heated plates and electric irons in moist condition of garments.
Objective of Pressing:
1 . Removal of unwanted creases and wrinkles : During garments manufacturing, creasing occurs in garments due to operator’s handling and for tying up garments tightly in boxes. To remove these creases and unwanted wrinkles pressing is to be done.
2 . Hiding imperfections: Pressing can hide a multitude (huge number) of garment’s imperfections and faults such as puckered seam and neps.
3 . To apply creases where necessary : Sometimes in garment we may need to apply some permanent creases such as pleats in shirts and for that purpose we have to apply creases or folds by pressing. Sometimes the pressing is done before sewing though after sewing it is also common.
4 . Shaping : Dart and seam are used to make garments properly fit with the shape of human body. To make these darts more attractive, pressing is applied which is known as The part of garment may have to be shrunk or stretched for shaping.
5 . Under pressing : For sewing easily and properly pressing is done on some parts of garments before sewing, which is called under pressing. Under pressing is done in manufacturing jackets,trousers,coats,etc. They also require final pressing.
6 . Final pressing : The pressing which is done before packing the garments is known as final pressing. By final pressing the garments become glossy (silky).
Process Flow Chart of Garment Finishing:
Finishing machine
⇓
Finishing input (style, color & size wise)
⇓
Initial quality check
⇓
Spot Removing
⇓
Ironing/Pressing
⇓
Inspection
⇓
Hang tag
⇓
Get up change
⇓
Folding
⇓
Poly
⇓
Bar code (buyer wise sticker)
⇓
Metal check
Equipment of Pressing:
Steam Iron:
In house hold operations, normal electric irons are extensively used. But today steam irons are used for industrial purposes. In stem irons, the iron is heated up by steam which is supplied from a central boiler or a mini boiler. The supply of steam is regulated by a hand regulated button. This steam is supplied to iron from the boiler through a pipe and let to come out through perforations under the iron. These irons are triangular in shape and their weight varies from 1 t 15 kg. For pressing this iron, ironing bed or table is required. With the bed there should be a provision of air suction system. After ironing, a foot regulated switch is pressed for air suctioning which removes the moisture and heat as well from the pressed garment quickly. To operate steam iron, skilled and experienced operator is required.
Steam Pressing Machine Process Flow Chart:
Steam from the BUCK is applied
⇓
The HEAD is locked to press the garment
⇓
Further steam may be applied from HEAD or BUCK
⇓
Head is released
⇓
Vacuum is applied to cool and dry the garment
Folding:
In garments industry, finishing is a process which consists of pressing or ironing, folding and packing of garments .Among them, by pressing were move unwanted crease or wrinkles from garments. Again folding is done by ironing. After pressing, the process used to fold the garment in a required size and shape is called folding.
Types of Packing and Folding:
There are four types of packing and folding for shirts, they are mentioned below:
- Stand up pack: In which collar is folded and kept at 900 angles with the body.
- Semi-stand up pack: In which collar is folded and kept at 450 angles with the body.
- Flat pack: In which collar is folded and completely laid flattened on the body.
- Hanger pack: In which shirt is supplied in box by hanging on a hanger.
Packaging :
The packing is always done in the carton boxes and there are several criteria for the packing of the garments they are as follows,
There are generally two kinds of packing the garment,
- The garment is individually packed/wrapped in the poly bag whose design will be specified by the buyer. i.e., either with the hanger attached or plain poly bag packing and then the entire garments (as per the packing criteria) is arranged in the carton box.
- The other method is that the garments are just folded and arranged in the carton boxes without putting them in the poly bag.
The packing criteria followed in each carton box as already mentioned is done in different ways which is as follows,
- Solid Packing
- Ratio Packing
- Mixed Packing
1 . Solid Packing: In this method of packing, the carton box will include garments of single colour and same
size. For example, 20 shirts of a similar colour say navy blue and the size say S will be
put in one carton box.
2 . Ratio Packing: In this method the carton box includes garments of same colour but of different sizes
according to the ratio.
For example, S : M : L : XL = 5 : 7 : 7 : 5.
3 . Mixed Packing: In this method the carton box includes garments of different colours but of same size or garments with different colours and different sizes in a particular ratio form. After the packing is done the garments are kept in the godown/stores until the buyer sends the buyer QC for the inspection purpose before delivering them and once the QC arrives, he will check them according to the 2.5 AQL level and then see if the garments has to be accepted or rejected.
(696)