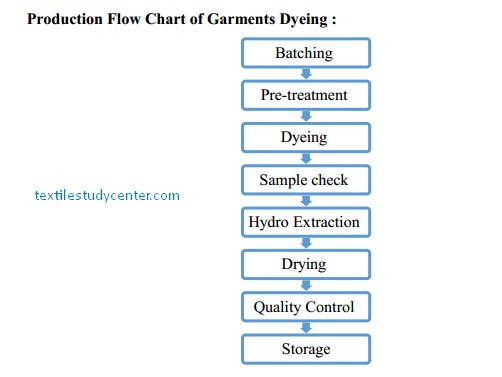
Garments Dyeing | Garments Dyeing Process
Garments Dyeing | Garments Dyeing Types and Processes
Garments Dyeing : The process of dyeing fully made apparel product like t-shirts , pants , trousers , shirts , jackets, tops, pullovers , dresses and bottoms is called garments dyeing. In Conventional method , Garments are made with pre-dyed fabrics and then cutting and sewing. But now grey fabrics are dyed in required color after manufacturing. It has become popular in recent days due to cost saving and fashion trends. Also it is capable to react much closer to actual market demand if the apparel is post dyed which reduces lead time and increases forecasting accuracy.
Advantages of garments dyeing :
- Lower cost needed
- Less time needed
- Less shade variations occurs
- Flexible lot size
- Old garments can be redyed
- Lower initial investment
- Lower liquor ratio
- Desizing , Scouring , Bleaching can be done in same machine
- Capable to react with fast changing market trends
- Fancy effects can be obtained
- Lower inventory
- Comparatively lower rejection rate
Disadvantages of garments dyeing :
- High cost of processing
- More material handling
- Special care for selection of interlining
- Higher seconds rate in production
- Labor intensive process
- Requries full checking of all pieces
Garments Dyeing Machines :
- Pedal Garments dyeing machine
- Rotary garments dyeing machine
Types of garment dyeing:
- Reactive dye
- Direct dye
- Sulphar dye
- Pigment dye
- Dischargable dye etc.
Production Flow Chart of Garments Dyeing :
Batching
Pre-treatment
Dyeing
Sample check
Hydro Extraction
Drying
Quality Control
Storage
Garments Dyeing Using Different Dyes :
Reactive dye : Reactive dye is only dye that reacts with the textile fibre & makes covalent with fibre. Under the suitable condition it reacts with –OH or –NH2 fibre & form covalent dye substrate linkage.
DYE-SO2-CH2-OSO3Na + HO-Cell —— D-SO2-CH2-CH2-O-Cell + NaHSO3
This is mostly used in garments dyeing. To produce light shade on garments , Dye added to the solution first then salt is added but if dark shade needed then salt is added first then dye added into the solution.If 5% or more dye is used into the solution then caustic is added into the solution.
Process flow chart of reactive dyeing :
Raw garments loading
Water added ( M:L = 1:40 )
Desizing ( detergent 1 g/L) 60oc , 10 min
Rinse 1X
Adding sequestering agent ( 1 g/L ) Room temp. , 5min
Adding leveling agent ( 1 g/L ) Room temp. , 5min
Adding globar salt ( 45 g/L ) Room temp. , 5min
Adding Reactive dye
( reactoband orange .60% , Reactoband black 8% ) 60oc , 5 min
Adding soda ash ( 20 g/L ) 60oc ,10 min
Adding caustic soda ( .5 g/L ) 60oc , 50 min
Rinse 1X
Neutralization ( Citric Acid 1 g/L )
Rinse 1X
Adding Fixing agent ( 5 g/L )
Drain
Acid Enzyme wash
( Ph 4.5 , acetic acid .5 g/L , 45oc, 15 min )
Rinse 2x
Softening ( 10 g/L ) 10 min
Hydroextraction
Drying
Direct dye : Direct dye is mosly used because it reacts directly with the fibre and it can be done on both hot and cool process. Washfastness of those color is less that why is done when washing is done after dyeing.
Process flow chart of reactive dyeing :
Raw garments loading
Water added ( M:L = 1:40 )
Desizing ( detergent 1 g/L) 60oc , 10 min
Rinse 1X
Acid Enzyme wash
( Ph 4.5 , acetic acid .5 g/L , 45oc, 15 min )
Rinse 2X
Adding Direct dye ,60oc , 5 min
Adding Globar salt ( 10 g/L ) 60oc ,10 min
Rinse 2X
Adding Fixing agent ( 5 g/L )
Drain
Softening ( 10 g/L ) 5 min
Hydro-extraction
Drying
Sulphar Dye : Sulpher dyes are complex heterocyclic molecules or mixtures formed by melting or boiling organic compounds containing amino or nitro groups with Na-polysulphide and Sulpher. Sulpher dyes are so called as they all contain Sulpher linkage within their molecules. Sulpher dyes are highly coloured, water insoluble compounds and have to be converted in to water soluble substantive forms (lucoforms) before application to the textile materials.
Process flow chart of Sulphar dyeing :
Raw garments loading
Water added ( M:L = 1:40 )
Desizing ( detergent 1 g/L) 60oc , 10 min
Rinse 2X
Adding Na-sulphide ,1000c. , 10 min
Adding globar salt ( 45 g/L ) 20 min
Adding Sulphar black , 100oc , 10 min
Rinse 2X
Adding Fixing agent ( H2O2 + Acetic acid 1g/L )
Rinse 2x
Softening ( 10 g/L ) 50oc , 5 min
Hydro extraction
Drying
: This is a kind of direct dye which is easily dischargable and it brings fashionable appearance. After dyeing various dry process like whisker , hand crapping , pp spray and others can be applied. For bringing seam abration , this type of dye is specially recommended. Color fastness is average and also has more brighter shades and attraction than other direct dyes .
Process flow chart of Dischargable direct dyeing :
Raw garments loading
Water added ( M:L = 1:40 )
Desizing ( detergent 1 g/L) 60oc , 10 min
Rinse 1X
Cationization
( caustic soda 2 g/L , 50oc, 10 min , ph 10-11 , catanizer 4% )
Rinse 2X
Adding leveling agent ( 1g/L , 5 mins , room temp )
Adding Dischargable dye ,60oc , 5 min
( Asudel yellow GL .11% , Asudel red GNL .0153 %, Asudel Brown AGL .162% )
Adding Globar salt ( 10 g/L ) 60oc ,5 min
Rinse 2X
Acid Enzyme wash
( Ph 4.5 , acetic acid .5 g/L , 45oc, 15 min )
Rinse 2x
Softening ( 10 g/L ) 10 min
Hydroextraction
Drying
Pigment dye : Pigment dyeing is not dyeing in the real sense as the pigment sticks on the fabric because of the binders. The pigments are insoluble in the water. It create very bright shades on the garments .
Process flow chart of Pigment dyeing :
Raw garments loading
Water added ( M:L = 1:40 )
Desizing ( detergent 1 g/L) 60oc , 10 min
Rinse 1X
Cationization
( caustic soda 2 g/L , 50oc, 10 min , ph = 8.5 , catanizer 4% – prefix k , 10 , min )
Rinse 2X
Adding Pigment dye ,65oc , 30 min
( orange 1% , Red 3% )
Adding Binder ( 3 g/L ) 60oc ,5 min
Rinse 1X
Hydro extraction
Drying
Precautions to be taken before garments dyeing :
- Design should be made engineering point of view
- Dyeing should be done after pre-treatment to reduce problems
- Grey fabric should be made from same lots or sources
- Seams should not be too tight or loose
- For mixed fibres , dye should be taken carefully
- Poor quality metal shouldn’t be used
- Proper interlining should be used
- Sewing threads from same fibres as garments
(9283)