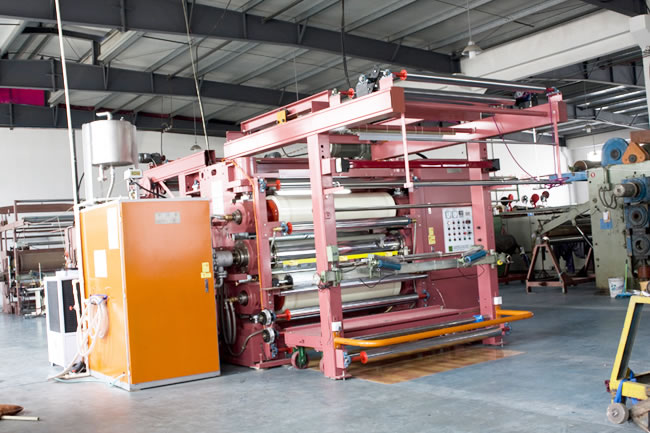
Industrial Problems During Calendering & Troubleshooting
Industrial Problems During Calendering & Troubleshooting
Calendering
Calendaring is a process where fabric is compressed by passing it between two or more rolls under controlled conditions of time, temperature and pressure.
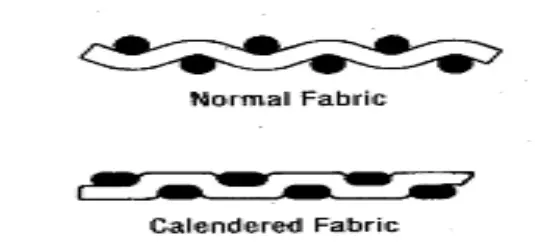
Industrial problems during Calendering & it’s troubleshooting :
During calendaring ,heat transfer problems are very common in the industry.
The following points have been noted during previous installations and appear to be the most common installation troubles.
Troubleshooting guide for heat transfer machine small bore rolls :
Lack of circulation and/or temperature control. Readings rising and falling over wide spread ranges.
- Improper piping hookups, a condition which will cause an apparent lack of circulation or lack of control, and can be due to piping name tags being located incorrectly or being incorrectly interpreted. Trace the piping system through the heat transfer unit out to the load and back to make sure it is correct.
- Caused by lack of circulation due to vapor binding of the system, restriction in the system or improper piping. Please refer to the original piping and system design instructions and double check all points concerning air venting and pipe sizing. Air vents are required at all high points.
- Pump rotation incorrect. Note that a centrifugal pump will develop some flow regardless of its rotational direction. It will, however, develop proper flow only in the right direction. Check for proper rotation by observing shafts or motor fan. Another method is to use a discharge pressure gauge in conjunction with the suction pressure gauge supplied on the heat transfer unit to determine which direction provides the higher discharge pressure.
- No water flow regardless of pump rotation. If the impeller has come loose from the shaft. Remount the impeller replacing the key or locknut. If the pump impeller is damaged. Replace the impeller.
Heat transfer unit will not heat up properly even though heating indicating light is on, heating contractor is known to be closed and the heater is checked for proper operation.
- Check to see that the steam valve is on, and that all condensate has had a chance to evacuate through the steam trap.
- Check to see that condensate line flows to atmospheric pressure area such as to floor drain or to zero in heat exchanger in dryer drainage system.
- Trouble could be caused by the solenoid cooling valve being stuck in the open position due to dirt or foreign matter. You can check this by looking at the drain and noting a flow of water at all times during the unit operation. This flow will continue even after the unit is electrically turned off. Another way to check is to close the cooler manual flow control valve for the zone in question and note if this causes the flow of water to practically stop. The cure is to clean the solenoid valve so that it resets properly.
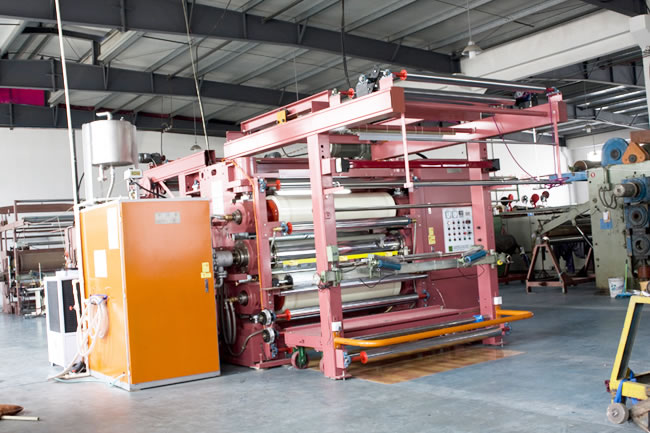
Some heating takes place even though the system is not calling for heat.
- Check the steam solenoid valve. Clean or replace.
Steam shows up at tell-tale valve.
- Check the steam trap. Clean or replace.
Water discharge pressure raises dramatically each time steam solenoid valve turns on.
- Check steam heat exchanger tube bundle for leaks.
Note: some increase in discharge pressure can be expected whenever water is heated in a closed loop.
Machine shuts off even though water pressure seems to be high enough.
- This happens if air in line reaches safety pressure switch. Roll loop line must be vented of all air. If necessary add more air vents so that every high point in the line is vented. Use automatic air vents, if available – this greatly speeds up the venting procedure.
Calendering | Factors Effecting Calendering | Calendering Machine Construction
Types of Calenders in Textiles
Industrial Problems During Calendering & Troubleshooting
(94)