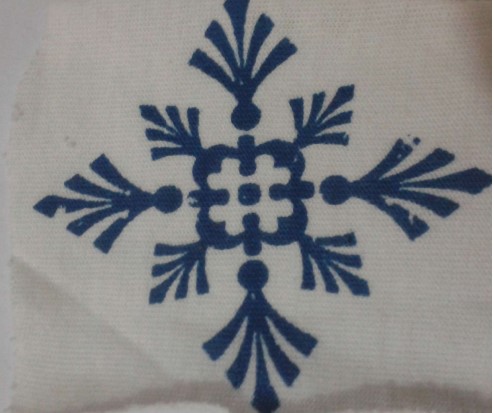
Printing of cotton fabric with reactive dyes (Screen printing method)
Printing of cotton fabric with reactive dyes (Screen printing method)
Objectives :
- To dye a material practically.
- To observe the practical advantages and disadvantages of this dye.
- To compare the theoretical idea with practical experiment.
Introduction :
Reactive dyes forms covalent bond with fibre polymer and thus attach itself with fibre. It is now a days mostly used for dyeing cotton yarn and fabric. It is a cationic dye. Hot brand reactive dyes have low reactivity.
By the term textile printing we mean the localized application of dyes or pigment and chemical by any method, which can produce particular effect of color on the fabric according to the design. In this practical we print cotton fabric with cold brand reactive dyes in block and screen-printing methods in combination method.
A dye, which is capable of reacting chemically with a substrate to form a covalent dye substrate linkage, is known as reactive dye. The dye contains a reactive group and this reactive group makes covalent bond with the fibre polymer and act as an integral part of fibre. Reactive dyes forms covalent bond with fibre polymer and thus attach itself with fibre. It is now a days mostly used for dyeing and printing of cotton yarn and fabric. It is a cationic dye. Cold brand reactive dyes have higher reactivity.
Block printing method is the oldest printing method. It is used mostly in sarees, handkerchiefs etc. in this printing method we use blocks of different designs.
In screen printing a very little screen made by glass fibre is used. There are many types of screen-printing, but we have done in our experiment was hand screen-printing. Hand screen-printing is mostly used for sarees to 14-16 colors in on pattern can be produced at a time.
Reaction :
Style of printing : Direct style.
Method of printing : Screen printing method.
Sample :
One piece of square size bleached, scoured cotton fabric (small) and one piece of square size bleached, scoured cotton fabric (bigger)
Recipe :
Reactive dye = 2 gm
Urea = 5 gm
Boiled water = 10 gm
Glycerine = 8 gm
Fine gum = 60 gm
Soda ash = 5 gm
————————————-
Total 100 gm
Preparation of thickener :
- 16 gm of starch and 200cc water are taken in bowl.
- Heat is applied and solution is stirred continuously until a thick viscose solution is obtained.
- By continuous stirring and boiling a specific viscosity is obtained.
- The heat application is stopped otherwise viscosity falls down. So temperature is maintained strictly.
Preparation of printing paste :
- At first we take required amount of dyestuffs in a bath.
- Then little amount of water is added into the bath for mixing these dyes. And start stirring for mixing the three types of dye.
- Then required amount of urea is added into the dye bath.
- After then required amount of thickener is added
- Then continuous stirring is done for few minutes for mixing all the ingredients of print paste.
- After mixing finally required amount of alkali is added to the dye bath and mix them with the help of stirring.
Printing process :
Screen printing method :
- The fabric is placed on the printing table of flat screen-printing machine. The table is made of soft by laying on it.
- Then the screen is placed on the sample fabric.
- The printing paste is taken on the screen perforation.
- Thus we can find the printed fabric with a smooth wooden strike the paste is spread over the screen with slight pressure.
- So that the dye particles can penetrate through the screen perforation.
- Thus we get printed fabric.
After treatment :
- Steaming for 7-12 minutes (1050-1100C)
- Dry heat treatment at 1400-1600C for 6 to 4 min
- Soaping with 0.5-1 g/L soap with repeated wash to remove unfixed dye and the thickener film.
Conclusion :
Printing of cotton fabric with reactive dyes has excellent build up property and maximum fixation. Shade is also bright. By this experiment we have acquire knowledge about process of printing cotton fibres with cold brand reactive dyes in combination shade. The shade of printed fabric is moderately good, as we required. Special thanks to our teacher and his assistants for grate cooperation.
(6041)