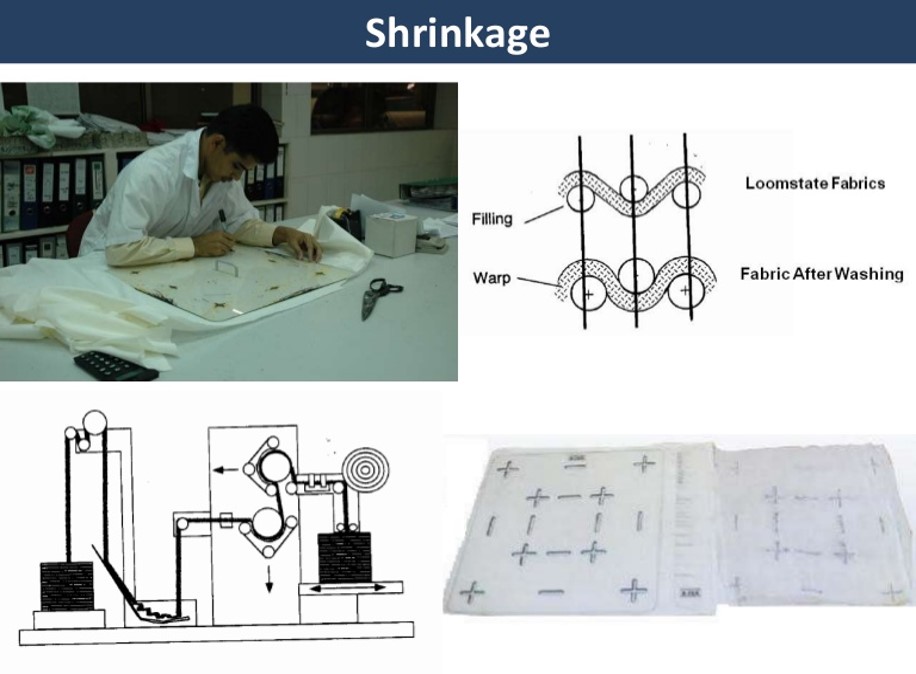
Fabric Shrinkage Test | Types Of Shrinkage | Causes And Influencing Factors Of Shrinkage
Fabric Shrinkage Test | Types Of Shrinkage | Causes And Influencing Factors Of Shrinkage | Measurement Of Fabric Shrinkage
Shrinkage :
The dimensional stability of a fabric is a measure of the extent to which it keeps its original dimensions to its manufacture. Shrinkage is a problem that hampers the dimensional stability of a fabric. A recent survey of manufacturers rated shrinkage as one of the ten leading quality problems.
Fabric shrinkage can cause problems in two main areas-
- During garment manufacture
- During subsequent laundering by the ultimate customer.
Shrinkage Types :
There are twol types of Fabric Shrinkage :
- Relaxation Shrinkage
- Progressive Shrinkage
Relaxation Shrinkage :
This occurs because the fibers and yarns are under tension when the fabrics are made. Later when the fabric is wet in a tension less condition , relaxation occurs.
Progressive Shrinkage :
This occurs each time a fabric is laundered. Unlike relaxation shrinkage which occurs only once, Progressive shrinkage continues and the fabric shrinks a bit more with each laundering of the major fibers , only wool and viscose rayon are subject to progressive shrinkage.
Types of Shrinkage:
Relaxation Shrinkage:
Relaxation shrinkage is the irreversible dimensional change accompanying the release of fibre strains imparted during manufacture which have been set by the combined effects of time, finishing treatments, and physical restraints within the structure.
Swelling Shrinkage:
Swelling shrinkage results from the swelling and de-swelling of the constituent fibres of a fabric due to the absorption and desorption of water.
For example: Viscose fibres increase in length by about 5% and in diameter by 30% to 40% when wet. Because of the fibre swelling, the yarns made from them increase in diameter which means that, a warp thread has to take a longer path around the swollen weft threads i.e. an increase in the length of the path the yarn must take if the fibre centers remain the same.
In swelling shrinkage, in a fabric the warp yarn must either increase in length or the weft threads must move closer together.
Felting Shrinkage:
Felting shrinkage results from the frictional properties of the component fibres and it causes them to migrate within the structure. This behavior is normally considered for fibres having scales on their surface such as wool.
Wool can be made shrink resistant by treatment to reduce the effect of the scales on friction. Chlorine treatments tend to remove the scales. Resin treatments are used to mask the scales.
Figure: The scale on wool fibre
Causes and Influencing factors of Shrinkage :
Causes :
Shrinkage is mainly due to yarn swelling and the resulting crimp increase during washing of cotton fabrics.Yarn swelling percentage is more in polyester cotton blending yarn.
Fabric Shrinkage Factors :
- Yarn Twist – Twist Shrinkage
- Knitting Tension
- Fabric GSM – GSM Shrinkage
Influencing Factors :
- Twist factor : If the Twist factor increases so the shrinkage will be increased
- Stitch Length : If the Stitch Length increases so the shrinkage will be increased
- GSM : If the GSM increases so the shrinkage will be increased
- Elasticity of yarn
Measurement of fabric shrinkage :
Step-1: Marking out samples
Step-2: Preparation of the specimen:
The general procedures for preparing and marking out of samples are given in the British Standard. For critical work the recommended sample size is 500mm X 500mm and for routine work a minimum sample size of 300mm X 300mm is considered sufficient. The samples are marked with three sets of marks in each direction, a minimum of 350mm apart and at least 50mm from all edges as shown in Figure. In the case of the smaller sample the marks are made 250 mm apart and at a distance of 25 mm from the edge.
For critical work it is recommended that the samples are preconditioned at a temperature not greater than 5O0C with a relative humidity of between 10% and 25%.All samples are then conditioned in the standard atmosphere.
Step-3: Washing
After measurement the samples are washed in the suitable washing solution in a washing machine conforming to certain specification. After the specified time has passed away the sample is rinsed.
Step-4: Drying
After rinsing the surplus water is removed by centrifuge or by hand squeezing, rubber–cover roller wringer, or rolling in toweling. drying is completed by means of a flat handed press or a heated flat iron.
Step-5: Conditioning and re-measuring
After drying, the specimen is conditioned in a standard testing atmosphere and the distances between the markings re-measured.
The percentage dimensional change calculated. The mean dimensional change and direction is reported:
(710)