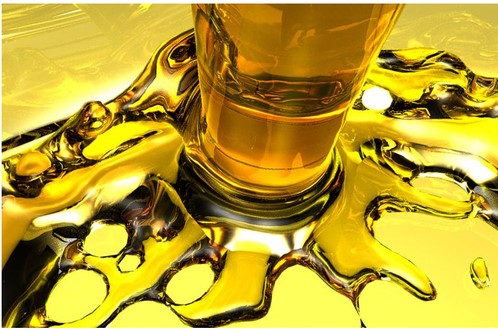
Spin Finishes , Sizes and Grease
Spin Finishes , Sizes and Grease
Spin finish:
A spin finish is a preparation applied by the manufacturer of MMF to staple fibers . It is used in the form of a water- based emulsion and contains anti-static agents, emulsifiers and lubricants.
Size:
Sizes are applied by the spinner of MMF to filament yarns ( smooth and texturized, textile and technical). They are mostly used in the form of water based emulsion but can also be applied in a solvent free form (neat oil) or in an organic solvent-base. In absence of water, they have fluid consistency and contain mainly lubricating products.
Greases:
The concept of grease is mostly connected to animal fibers but also in connection with dyed (synthetic) flocks or sliver. These are considered as secondary finish. They are applied as water based emulsion.
Spin Finishes , Sizes and Grease Features :
1 . They have a common characteristics, all of them act as lubricants in manufacturing and processing of fibers , filament, and resulting yarn.
2 . Processing can not be done adequately without the application of lubricants. The significance is analogues to lubrication oil in motor.
3 . The only function is not lubricating or influencing frictional properties but influence other properties such as anti-static, thread connections, openability and protection of the material.
4 . It not only provides advantages but also creates some problems such as sticky smears, cause swelling of fibers or fiber guiding elements, create fumes, decomposes to heat etc.
So the best practice is to use optimal range of finishes which will balance between benefits and problems.
Why spin finishes are required : purpose / necessity ?
1 . Natural fibers have inherent lubricating compound( natural wax ore grease) needed for textile processing. This is true, for example, of cotton( after it has been freed of seeds and dirt particles in an expensive process stage). It is also true of wool, although this fiber usually has to be greased during processing.
2 . MMF have smooth surfaces, and contains low moisture content, and have high frictional coefficient. So it is necessary to apply spin finish to correct this coefficient of friction, and to eliminate static electrical charge.
3 . Necessity during spinning: It is used to impart sliding characteristics, give adequate thread joining properties and prevent building electric charge. A size develops its properties in the presence of applied moisture. During spinning , the filaments are coiled into cans, these cans are then grouped and fed to the drawing stage.
4 . Necessity during drawing: In this process filaments pass through many drawing and guiding elements. So it is necessary to give them some sliding so that they can slide easily over guiding elements while preventing slippage. Further more adherence of oligomers must be prevented.
Why final spin finish is applied
- To lubricate the fiber surface in order to give optimal fiber to fiber, fiber to foreign body friction characteristics. Foreign bodies are of various kinds and regarded as surface roughness (metal, ceramic, rubber, plastic).
- To protect against electrical charge. Electric charge arises from high friction and low electrical-conductivity properties of synthetic fibers.
- To assist opening .This effect, and with it the subsequently mentioned fiber adherence, is achieved by optimal interplay with the set crimp of fibers.
- To impart coherence to a fiber strand ( fiber adherence in the card web, D/F sliver and yarn). It is a contradiction to opening mentioned above.
- To assist in avoiding the formation of laps. Lap formation is caused by building up of spin finish on the thread guide. Lap formation can also arise from electrostatic attraction in absence of adequate spin finish.
- To reduce fly. Fly is generated due to inadequate fiber adherence.
- To lubricate properly so that fiber shortening does not occur.
Requirements to be fulfilled by spin finish: summary of the spin finish
1 . No disadvantageous effect on the yarn or machines.
2 . Easily washed out.
3 . No diminution of dye fastness
4 . No influence on dye affinity
5 . Even distribution on the fibers.( otherwise non lubricated parts are subject to friction)
6 . High adherence to the fiber surface.
7 . Good storability( resistant to ageing, i.e. resistant to migration or bacterial attack)
8 . No gluing effect
9 . No flaking when rubbed.
10 . Either resistant to heat. Or sublimated without leaving any residue.
11. Insensitive to rubbing(wear)
12 . Environmentally friendly and Non-toxic: must be biodegradable and easily eliminated and less toxic to fish .
What are the components of spin finish ?
Lubricants :
Lubricants improve sliding properties. They include mineral oils, waxes and oils of esters. Esters oils have higher resistance to temperature change and lower reduction in viscosity at higher temp. than mineral oils, waxes. Mainly polymeric lubricants such as polyalkenylene oxide, polyalkenylene and silicon oils etc. are used.
Emulsifiers :
It improves emulsifying properties but also enable spin finish to be washed out. These emulsifiers are tensides(surfactants) of anionic or nonionic substances. They include ethers and soaps of fatty acid, ethers of fatty alcohol, fatty amino ethers, sulphates, amino acid substance. Cationic and amphoteric ethers are now used solely on acrylic fibers.
Antistatic agents :
The main Antistatic Agents are :
1 . Ester salts or phosphoric acid
2 . Metal salts of fatty acid
3 . Anionic and cationic emulsifiers.
In processing due to friction electrostatic charge is generated on fiber surface- this problem can be reduced by using anti-static components of spin finish.
Fiber adhering substance :
These substances ensure lateral coherence of fiber strands and prevents splitting out of individual fibers. This includes:
1 . Sarcosides
2 . Sulphosuccinates
3 . Sulphated oils
4 . Colloidal silicic acid.
Additives :
This includes:
1 . Antioxidant( steroid inhibited phenols)
2 . Bactericides ( silver colloids, Cl- formaldehayde release)
3 . Corrosion inhibitors ( Sarcosides, metal salts of fattyacid)
4 . wetting agents (emulsifiers)
Spin-finish composition :
1 . Lubricant concentration between 20-70%
2 . Up to 80% proportion of surface active products(emulsifiers, antistatic agents)
3 . Less then 5% additives.
Problems arises due to spin finish ?
1 . Spin finish combines with dust and forms hard coating on machine parts. Which disturbs processing such as in the card clothing’s (specially in T-in), in the sliver guide passages ( of card and D/F), in the flyer( on roving frame), and on the rotor and opener roller ( on rotor spinning). This adds additional cost as these parts must be cleaned periodically.
2 . Inadequate distribution of spin finish can cause fiber flaking and lead to increase in ends breakage and also accumulation of static charge.
3 . If spin finish penetrates into machine components such as rollers and aprons when the M/C is not running. It can cause swelling or cracking creating drafting problems.
4 . Fiber treated with TiO2 as delustrant shows lower drafting resistance but simultaneously higher wear on fiber guide elements.
5 . Besides TiO2 other spin finish can also cause wear on m/c components, cationic substances are suspected in this connection.
6 . Wear occurs on travellers and on opening rollers of rotor spinning machines leads to spinning problems and degrading yarn characteristics.
(2407)