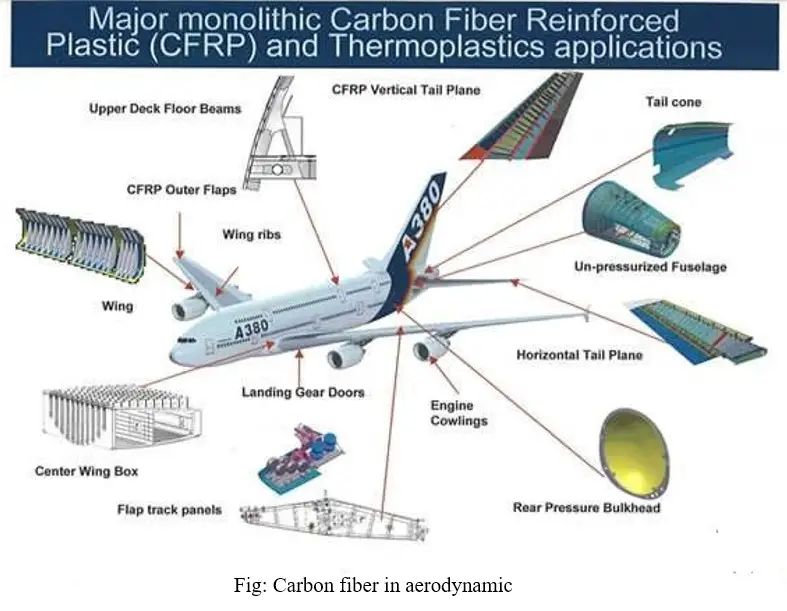
Potential of “CARBON FIBER” for being the Future Material in the Domain of Technical Application
Potential of “CARBON FIBER” for being the Future Material in the Domain of Technical Application
Ishmam Zahin Chowdhury, Bangladesh University of Textiles
Ahamed Hossain Bappy, Bangladesh University of Textiles
Carbon fiber, by far the most widely used technical fiber in high performance applications, is now paving its way to the previously metal dominated fields. This light weight material has incredible strength with a lot of desirable properties which make it most dominating material in the modern world. Having a specific structure makes it suitable for versatile use especially in the technical sector. Due to its versatility its popularity is increasing day by day.
“We didn’t leave the stone age because we ran out of new stones. We created new materials, and that’s what we are doing here. We are creating a future.”
-By Deborah Wince-Smith; President and CEO (Council on Competitiveness).
In order to create that future for technical textile, carbon fiber is introduced.
Carbon fiber is a fibrous material having micrographic crystal structure which is made by fibrillation of acrylic resin or from oil coal or pitch. In the production process controlled pyrolysis, removing oxygen, nitrogen and hydrogen gives improved mechanical properties by developing crystallinity and orientation in inner structure. Carbon fiber lacks any three dimensional order unlike graphite. In PAN based carbon fiber the inner chain structure is transformed to planer structure during stabilization and carbonization process. [1]
Carbon fiber consists of thin fibers ranging from .005 to .010 mm in diameter which is even less than a human hair. The carbon atoms are bonded together in microscopic crystals that are more or less parallel to the long axis of fiber making it incredibly strong for its size. Thousands of carbon fiber are bonded together to form yarn when combined with resin .It can be modeled to high strength to weight ratio. [2]
Carbon fiber has the potential to replace steel for being strong stiff and lightweight at the same time. Having one half of the weight of the aluminum with three times the strength make it versatile for application where stiffness and low weight is required simultaneously by allowing a designer virtually unlimited ability to build parts with stiffness and strength far exceeding aluminum, steel and even titanium. It raises its possibility to overthrow metal.
Carbon fiber has negative to very low (-1 to +8) coefficient of thermal expansion. This thermal stability gives carbon fiber increased manufacturing precision on other metal increase in size when heated. [2]
Its high electric conductivity and good EMI shedding property brings CFRP to field of EMI shielding. It has good x -ray permeability in addition to lightness and rigidity. In the field of medical equipment parts in CFRP is highly welcomed. Depending upon the manufacturing process and the raw material carbon fiber can be made into protective clothing for firefighting. Carbon fiber blanket is also used in welding protection. [2]
Applications:
Carbon fibers are now available in a wide range of useful form. The fibers are bundled woven shaped into thin sheets for construction purposes, supplied as cloth for molding or regular thread for filament winding.
Carbon fiber has made its mark as reinforcing materials for its use in concrete structures. The world’s first bridge made from reinforced concrete was erected in 2005 in Oschatz. Textile made from carbon fiber roving are particularly suitable for reinforcing concrete with a load bearing capacity of 3000 N/mm2 and approximately 1.8 g/cm3 makes it more efficient than connectional steel reinforced concrete. Now-a-days, research has been made in Japan to build architectural structure by using CFRC for earthquake protection. [3]
Next generation “carbon fiber” has capacity to reduce the passenger car weight by 50% and improve fuel efficiency by about 35% without compromising any aspect. This can save more than $500 in fuel over the life of the car at today’s gasoline prices. Due to their light weight and strength, carbon fiber is used to manufacture racing cars.
In aerospace field which demands materials of light weight and high rigidity, the aerospace antenna and satellites adopt CFRP parts.
The light weight and tensile strength properties of carbon fiber make it ideal for making lightweight and durable sports products like golf shafts, skis, snowboard, hockey-stick, fishing rod and bicycles.
High dimensional stability, low coefficient of thermal expansion and low abrasion properties of carbon fiber are helpful to build missiles, aerospace antenna support structures, large telescopes, optical benches, weave guides for stable high frequency precision measurement frames. Good vibration damping helps to make audio equipment, loudspeaker, pickup and robot arm. Chemical inertness and high corrosion resistance helps in nuclear field and other process plants. Biological inertness and x-ray permeability helps in medical applications like surgery tendon and ligament repair. Carbon fiber also can be woven into a fabric suitable for using in defense application. [2]
Carbon fiber is a great stuff when strength/weight ratio is primary concern. However high tensile strength of carbon fiber is not always very convenient. It has low compression on shear strength. In almost all engineering application, it requires composite material which makes carbon fiber harder to work with. The production cost of carbon fiber is very high making it highly priced material for consumers. To get the same production using carbon fiber costs 20 times higher than using the same amount of steel. The production process itself is not easy on the environment. Also recycling of carbon fiber is not eco-friendly and a lengthy process. [4]
Research:
In view of high performance features, researchers worldwide are working on using carbon fiber as environment-friendly carbon fiber reinforcing materials. The project of making carbon fiber reinforced concrete is being supported by the German government to establish Germany as the world’s leading provider of carbon fiber reinforced concrete in the construction industry. The federal ministry of education and research is funding this project cost roughly EUR 45 million via funds made available within the framework of the Zwanzing, 20% partnership for innovation project. Karl Mayer is also participating in this project. The project is to focus on the production of biaxial textile structures governing reinforced concrete components. These biaxial have a grid like construction in which fiber material is arranged at an angle 0 in yarn and at an angle 90 in weft yarn. This structure is fired by the measurement of knitted stitches.
Researches from the University of Colorado Boulder have found an eco-friendly and cost effective way of recycling carbon fiber composites. According to Wei Zhang, Associate Professor of Chemistry of the Colorado Boulder, recycling the carbon fiber composites simply requires soaking the composites in an organic solution at room temperature which is really energy efficient and eco-friendly. This technology is now patent pending. [5]
Oak Ridge National Laboratory (ORNL) is currently running its Department of Energy’s (DOE) initiative to develop disruptive technologies for producing low cost carbon fiber. The primary forces of ORNL’s carbon fiber research are disruptive cost reduction for industrial grade carbon fibers with modest performance penalty being acceptable. ORNL’s carbon fiber program does include a high performance element in which new performance levels are sought including cost as a secondary factor as part of ORNL’s DOE funded facility. The Carbon Fiber Technology Facility (CFTF) serves as a hub for public-private partnerships. The mission of these partnerships is to forge industry-government collaboration as to accelerate the development and deployment of lower cost carbon fiber materials. [6]
Future and Commercialization :
The future of carbon fiber is very bright with vast potential is many different industries: fuel efficient automobiles, high performance automobiles, light weight concrete based construction and earth quake protected infrastructure, alternate energy storage and transportation, oil exploration are some of the promising sectors for carbon fiber. [7]
Renowned car company BMW has begun volume production of CFRP components as early in 2003 and has been increasing its output ever since. In 2009, BMW and SGL group formed a joint venture called SGL automotive carbon fiber in order to combine their core competencies and industrialize the use of carbon fibers in the automotive sector.
MAI carbon fiber cluster management GMBH, a partner of BMW and Audi states that production costs for carbon fiber could soon be lowered by 90 percent. They have taken a $102 million research project backed by Germany’s federal government hoping to reduce carbon fiber production cost. [8]
Case file :
Indy Car driver Martin Plowman was hit with a flying debris from a crash during the 2014 Grand Prix in Indianapolis. Luckily he was saved as his helmet was equipped with carbon fiber composite strip. He was wearing a visor shield which was made of high-tech carbon fiber composites, which protected his eyes.
He sent out his tweet with a photo of his helmet after the race.
Fig: Post on twitter by Martin Plowman
In the present developing sector of technical textile, carbon fiber can define textile in a new way. To expand the empire of textile in the technical site is surely a great addition for world’s engineering civilization. Good engineering can work around to increase its viability and usability for making it a material of choice for the upcoming era. In the present “Earthquake issue” throughout the world, carbon fiber reinforced concrete can surely hold the candle.
References:
- https://en.wikipedia.org/wiki/Carbon_fibers.
- Raghavendra R. Hegde, Atul Dahiya, M. G. Kamathreleasescarbon fiber onApril, 2004. http://www.engr.utk.edu/mse/Textiles/CARBON%20FIBERS.htm.
- Japan Carbon fiber Manufacturing Association. http://www.carbonfiber.gr.jp/english/index.html&http://compositesmanufacturingmagazine.com/2016/01/carbon-fiber-composite-protects-japanese-building-from-earthquakes/.
- https://www.quora.com/What-are-the-advantages-and-disadvantages-of-using-carbon-fiber-in-place-of-fiber-glass.
- http://www.colorado.edu/news/releases/2016/02/15/cu-boulder-researchers-recycle-carbon-fiber-composites-new-equally-strong.
- http://blog.fibreglast.com/carbonfiber/oak-ridge/.
- http://zoltek.com/carbonfiber/the-future-of-carbon-fiber/.
- http://blog.caranddriver.com/weave-come-so-far-bmw-audi-and-german-consortium-developing-carbon-fiber-thats-90-percent-cheaper/.
(554)