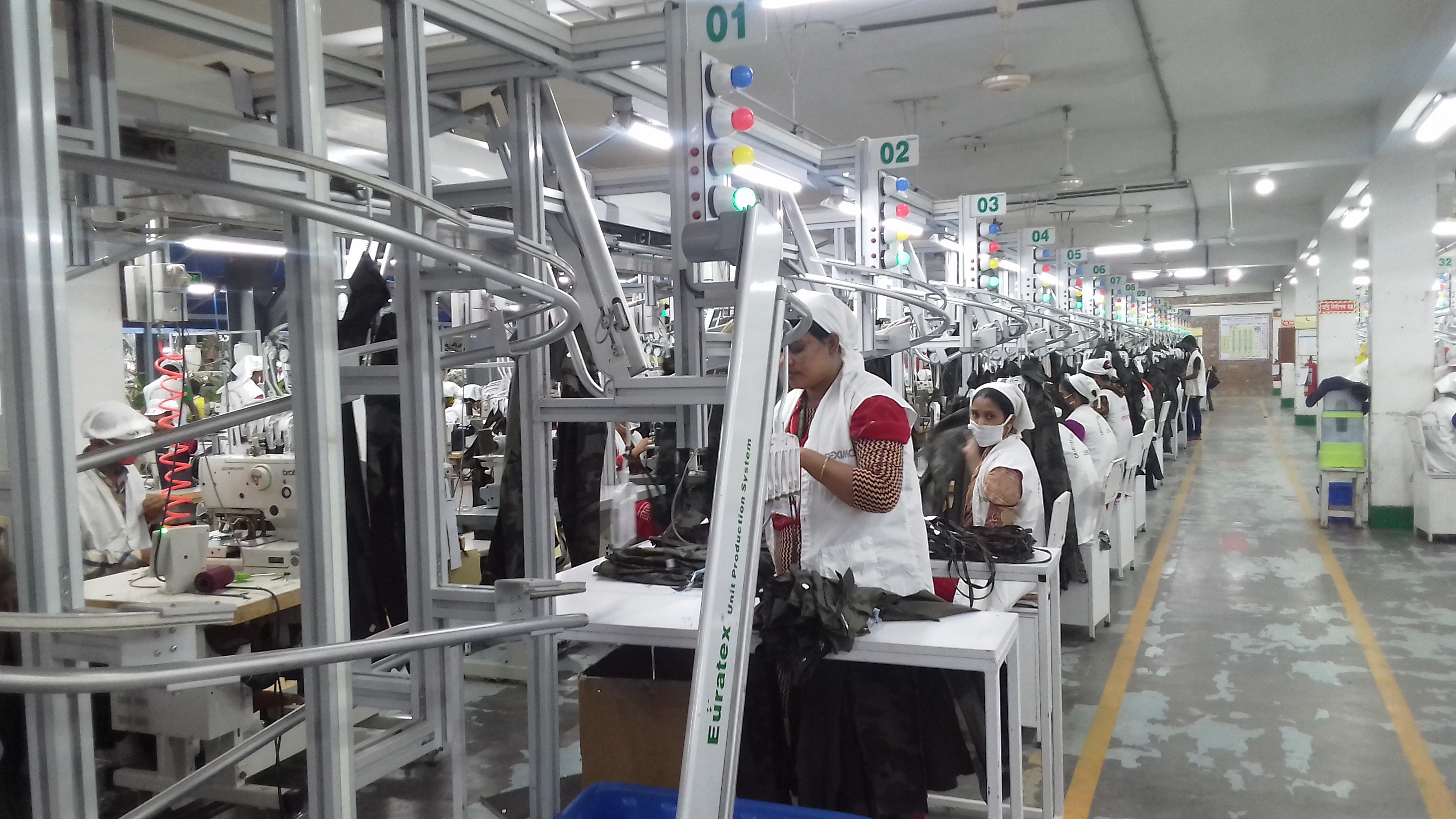
Unit Production System | Overhead Production System | Hanger Production System
Part 1: Garment Production System | Apparel Production System
Part 2: Progressive Bundle System
Part 3: Unit Production System | Overhead Production System | Hanger Production System
Part 4: Modular Production System | Cellular Garment Manufacturing | Toyota Sewing System
Unit Production System | Overhead Production System | Hanger Production System
The unit production system (UPS) for apparel industries is a flexible material handling system that requires a computerized overhead transportation system to move the garment components automatically from one workstation to the next according to a pre-determined sequence. It replaces the traditional garment production system of handing, bundling, tying and untying, and manually moving garment parts. It provides uninterrupted workflow to the workers and helps to improve work efficiency and product quality. In the fast-moving fashion and apparel industry, this is highly essential.
Fig: Unit Production System (Euratex)
Fig: Unit Production System (INA)
Features of a Unit Production System
This system concerned with a single garment and not bundles.
Layout design can be U, L, J, S and E shaped.
This system is entirely computer controlled.
It uses an overhead transportation system that automatically routes and deliver the cut pieces to each sewing station.
Some Manufacturer applies the ethernet communication mode that can communicate by point-to-point.
Even if one station does not work, the whole system still works normally.
The system can identify whether the atmospheric pressure is normal and will auto-alarm when the air pressure is below the system requirements.
It has been ergonomically designed to reduce the amount of handling of the garment.
The UPS is expensive (800-2000 USD/Station) to install, but it allows manufacturers to respond quality to the demand of suppliers.
This system is capable for rework easily. Because each garment is tracked within the system and any problems to with quality control can be traced back automatically to the operator to be corrected.
This system also records all data in each workstation within the line and compute them for Management Planning & Control.
The workstations are constructed as close as possible to the operator. So, the components are sewn without removing from the hanger in most of the cases.
Sewing operators concentrate on sewing without worrying where workpieces are coming from and should go to.
The system is highly flexible and can rapidly be modified to changes in the production line or the need for expansion.
Up to 40 garment styles can be produced concurrently on this system.
It is possible to produce multiple designs, colors and sizes at the same time in the same production line.
It can be widely used in garment factories, especially for knitted/woven, trousers/shirts and other clothes.
Operational Principles of Unit Production System
This system is designed based on the following principles
- An operator set the process in the control station.
- Worker loads the cut pieces in a hanger from the loading station
- The hanger routes to the next workstation automatically according to the predetermined process in the control station.
- Product is put together at every stage at each subsequent sewing station
- Product gets checked at the quality & control station (in line)
- Product continues to be pieced together at the next subsequent stations
- Final product gets checked and approved
- Approved product lands at the unloading station
- The empty hanger returns to the loading station.
Components of Unit Production System
UPS consists of different types of element, such as
- Computer with Software
- Hanger with Microchips
- Overhead Conveyor with solid and strong structure
- Easy Push Button
- LCD Control Panel
- LED Screen
A computer with software is set up in the front of the production line for tracking production and automatic balancing of workflow. It also provides information like inventory data, immediate track of style, amount of time operator works, time spent on the individual unit, operator who works on each unit, piece rate earned for each unit, employee information, production report, wage report, efficiency report, QC report, costing and performance data. So, real-time production control can be done.
Hanger with Microchip
All parts of one garment can get loaded on one single hanger. Each hanger has a six-finger clip with sawtooth which is used to prevent cutting pieces from falling off. For smaller cut panels that can’t be gripped by hanger frame like bra, underwear and hats etc. are placed in Baskets. An RFID/microchip is also placed on each garment hanger which ensures to monitor each hanger in the process of production. All parts of one garment can get loaded on one single hanger. When the system is out of power or other special cases, the racks can’t enter the station normally. But when the system restarts. They can navigate to the designated routes again. Workpieces travel on an overhead conveyor, by a hanger which holds then on a finger like rubber padding.
Overhead Conveyor with accumulating rails
The unit production system consists of the main conveyor and accumulating rails for each workstation of garments. The overhead conveyor operates much like a railroad track. Hangers are moved along the main conveyor and switched to an accumulating rail at the workstation where an operation is to be performed. At the completion of an operation, the operator presses a button and the carrier move on to the next operation.
When one operator finished the operation on one hanger, a push button at the side of the sewing machine is gently pressed, the suspension system will automatically transfer the hanger to the main conveyor line.
LCD Control Panel
LCD display at every station controls personal’s log-in, reveals production quantity and production efficiency. At the same time can distribute the racks automatically according to the worker efficiency. Therefore, it can promote the worker motivation and make full use of resources.
LED Screen
The Unit production system is equipped with LED Screen, on which production target and current production rate are displayed continuously. This is to improve real-time management and increase corporate image. Below the LED Screen display that, “Euratex Hanger Systems EMBEE WELCOME YOU! The goal of 634020 is 2800 pieces and has completed 1219 pieces, Completion rate is 43.54%.”
Fig: LED Screen
Different Work Station of Unit Production System
Basically, UPS has a workstation up to 35-45. These workstations categorized by the following way-
- System Control Station
- Hanger Storage Station
- Loading Station
- Sewing Station
- Inline Inspection Station
- Thread Sucking Station
- Final Inspection Station
- Unloading Station
System Control Station
UPS has a Computer control center in which a powerful software is installed in a computer for routing and automatic balancing of workflow which minimizes the bottlenecks and stoppages. An operator operates the computer according to the product design. Sitting in this station operator can able to show the problem where it is occurring and takes necessary steps to solve this. The computerized control system also provides real-time data related to the which allows the management to be consistently on top problems.
Normally, upright rails are interconnected to a computerized control system that routes and tracks production and provides the real-time data related to the production. The automatic control of the work flow sorts work and balances the line.
Hanger Storage Station
After removing the finished garments from the hangers in the unloading station, the hangers are stored in this station for several times. 60-80 hangers can be stored at this station.
Loading Station
When the hanger comes from the hanger storage station, one operator loads the cut pieces of the garments from different bundles. When the operator gently presses the button, the hanger is passed to the next process through the conveyor. The operator will responsible for shade matching of bundles.
Sewing Station
In this station, there are many types of sewing machine is placed for performing a different type of job. When possible, operation is performed without removing the cut panels or sewed parts from the hanger. After completion of the job, the operator gently press push button and suspension system will automatically transfer the hanger to the next workstation. In case of adding trims on the garments, trims are stored on the workstation before but not supplied by hanger as cut panels.
In-Line Inspection Station
Before assembling the front and back part of the garment, these parts are carefully checked to find out the problem. If the operator finds any kind of defect, he/she marks the problem and send to the operator who is responsible for that by typing the operator ID number on the LCD control panel. When the defective garments will come to the sewing operator, he/she will repair the defect correctly and send it to the in-line inspection station by typing QC person’s ID number on the LCD control panel.
Thread Sucking Station
After sewing and trimming, extra thread will be sucked from the surface of the garments. Thread sucking could be automatic or manual.
Final Inspection Station
Some necessary information like measurement sheet, trim card, counter sample etc. are kept on this station for matching the requirement of the buyer. The operator checks the finished garments to find out the defect and placed stickers on the defective areas. Then the defective garment will be passed right back to the sewing operator who is responsible for that.
Unloading Station
After completion of the final inspection, the garment is removed from the hanger and kept in a carrier which will be sent for the further process.
Advantages of Unit Production System
No need to replace the sewing machine.
Bundle handling completely eliminated.
UPS increase production efficiency 15-30%.
Decreased work in process (WIP), improved space utilization, and increased productivity are but a few of the systems benefits.
Support multi-order, multi-style and small batches production.
Reduce production cycle.
Improve the machine utilization, reduce the handling and increase the moving time of needles.Generate real-time performance report.
Create a clean and tidy work environment.
Easy and efficient staff assignment with minimum human resources.
Improved lead timeless work in process.
Improved space utilization.
Better handling of garment without touching the floor.
No chance of serial and sequence mistakes.
Output is automatically recorded, eliminates the operator to register the work.
Increase enterprise image.
Rework can be done easily.
Labor costs reduced by elimination of bundle handling and employee attendance improved.
Less rejection and automatic counting of the finished product.
Required minimum ironing due to the hanging of garment pieces.
Disadvantages of Unit Production System
Huge amount of cost, installing a UPS include costs of buying equipment.
Special training required for the system and for the employees.
Downtime is a potential problem with any of the systems.
Proper planning is required to be effective.
The payback period of the investment takes a long time.
Variety of styles & less quantity are not effective in this system.
Shuttle operators and utility operators needed in every batch to balance the line effectively.
Proper maintenance of equipment and machinery is needed.
Part 1: Garment Production System | Apparel Production System
Part 2: Progressive Bundle System
Part 3: Unit Production System | Overhead Production System | Hanger Production System
Part 4: Modular Production System | Cellular Garment Manufacturing | Toyota Sewing System
(8335)