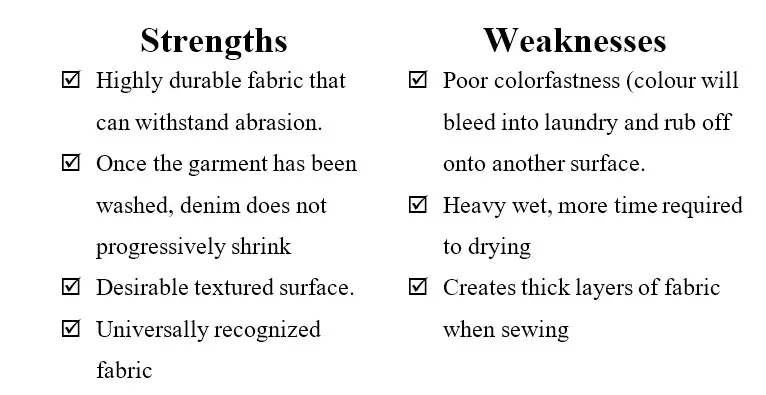
Denim Fabric | Denim Fabric Manufacturing
Denim Fabric | Denim Fabric Manufacturing
Denim fabric
Denim is a fabric which has a huge market demand all over the world both for casual wear as well as fashionable wear. It has been used extensively used by the people of all ages, classes and genders. Denim was born in a manufacturing center in the southern France where the fabric was used for upholstery in the nineteen centuries.
The manufacturing center was called Nimes, and the fabric was called “Serge de Nimes” or “the cloth of Nimes”.‘Serge de Nimes’ was a blend of silk and wool, but todays denim has always been made of cotton. There was another fabric, Italy was called jean, was a blend of linen and/or wool. By the eighteenth century, jean fabric was made completely of cotton which was used to make men’s clothing. The popularity of denim was also on the rise and it was stronger and more expensive than jean. Even though the two fabrics were very similar in other ways, they did have one major difference: denim was woven with one coloured thread (the warp) and the other white (the weft), while jean was woven with two yarns of the same colour.
Among all the textile products, jeans made from blue denim have been popular over a longer period. Washing plays an important role in denim manufacturing because of the countless effects on jeans that consumers so desire. Denim is a hard and durable warp faced 2/1 or 3/1 cotton twill-weave fabric with a dyed blue warp and raw white weft. Spandex yarn is added to denim to make the denim elastic. A 2–5% spandex blend with cotton will stretch the fabric over the body for a more comfortable fit.
Strengths and Weaknesses of Denim Fabric
Denim Fabric : How it is made
Step By Step Denim fabric Manufacturing flowchart :
Step 1 : Cotton bales are opened, cleaned and blended to ensure the greatest possible fibre uniformity. The fibers are separated and foreign matter removed.
Step 2 : Cotton is fed into carding machine, where the fibers re combed to make them parallel. They are then formed into card sliver.
Step 3 : The card sliver goes onto drawing frames, which further parallels the fibre. The sliver goes onto the roving frame where the diameter is reduced, and twisting into something like yarn takes place.
Step 4 : The spinning frame takes the roving, reduce it to the necessary size and then twists the fibers into proper yarn. The filling yarn goes to the denim looms and the warp yarns to the processing areas.
Step 5 : The spooler takes the warp yarn and transfers it to a package called “cheese”. Cheese are put into a warper. where they are wound on beams to be dyed. The warp yarns thus supply the indigo colour in the eventual fabric.
Step 6 : The warp beams are dyed on an indigo range.
Step 7 : The stored of dyed yarn are separated and wound onto a beam. These beams are combined at the slashers to from the warp, which goes to the loom. Warp are strengthened on slashers by coating them with a layer of starch called sizing.
Step 8 : The warp and filling yarns are ready for weaving on high speed automatic looms. The warp yarn runs length wise, the filling yarn crosswise in the fabric
Step 9 : Cloth inspected, finished, re-inspected and put in cartons or rolls for shipment.
(959)