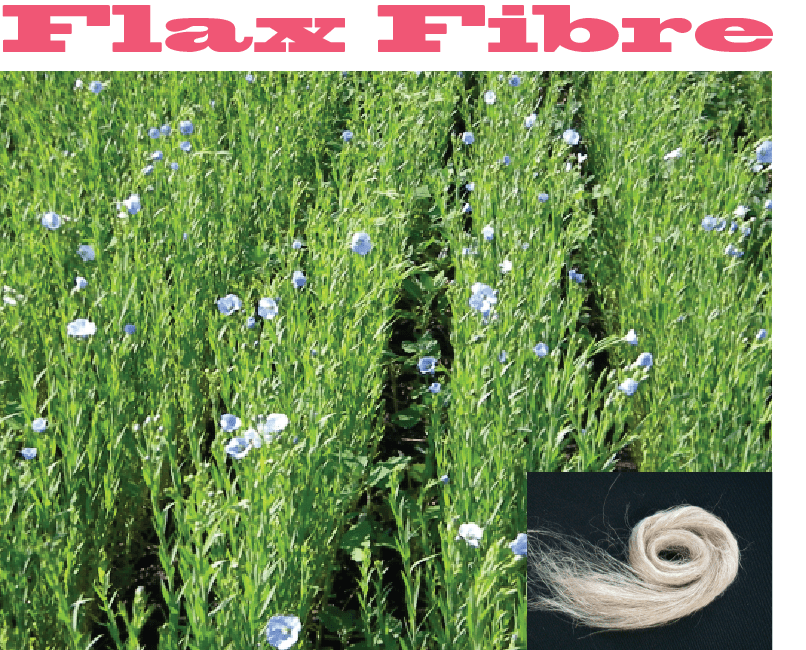
Flax Fiber: A Brief Discussion | Flax Fibre Cultivation | Flax Fibre Cultivation Process | Flax Fibre Cultivating Countries
Flax Fiber | Flax Fibre Cultivation | Flax Fibre Cultivation Process | Flax Fibre Cultivating Countries and Production
Flax Fiber
Art of producing Linen from flax plant was known earlier than 2500 BC, though flax production was introduced to the industry in 12th century. Flax fibers have been used for textile utilization such as woven, knitting and technical textiles for many centuries. Raw materials that we get from flax can be applied in bio-polymers, aerospace and automotive industries as well as for production of agro fine chemicals. In the last few years, new achievements have been made in the research field of bust fibers (especially flax). New varieties, new technology for processing and most importantly broadening the area of application of flax have been achieved.
Cultivation and Growth of Flax
Flax is a member of genus Linum in the family linaceae. The scientific name of the plant is Linum Usitatissimum. Flax is cultivated in cooler places of the world. The harvesting of flax requires special skill, operations and particular machines. The farmers require skills to figure out when the flax straw is sufficiently retted to turn and when to lift it before it is over retted. Flax is not usually vulnerable to pests and parasites. Flax has a fast growth rate, usually reaching maturity in 100 days. It is a good rotation crop. Fig: Flax seed pod
Flax plant growth has specifically five stages –
flower bud formation
flowering
fruit formation
fiber maturity
seed maturity
The ideal soil profile for flax is given in above figure.Flax requires little fertilizing. Excess fertilizing can cause ‘lodging’ of the crop. Flax requires only 10-45 kg of nitrogen, 60-65 kg of calcium and 100-120kg of potassium per hector. The depth for sowing should be at about 2 cm and the distribution rate should be at between 1800-2000 seeds per square meter. Normal sowing periods in Europe are from middle of March to middle of April and ‘pulling’ from and of July to the end of August.
Harvesting of Flax
Sequence of operations is carried out for harvesting of flax. Operations specific to harvesting are pulling of the stalks, retting (turning & lifting), drying, stalking.
1 . Pulling
Pulling is carried out when flax reach a certain level of maturity. Maturity is assessed by the color of the stalks and seed pods, which should be yellow brown and also by the degree of defoliation. Maturity requires approximately 1400 degrees’ Celsius day (sum of average daily temperatures after sowing).
During harvesting the pulling machine advances through the standing crops and the crops are pulled out a pair of endless belts. Flax pulling ensures that the entire length of fiber is harvested.
Fig: Pulling of flax
2 . Retting and Turning
Retting is a natural process for separating fibers from the stalk. Under suitable conditions bacteria and fungi colonize the stalks and their enzymes attack the pectic cements that bind the fiber bundle to the phloem of the stalks. Currently, two types of retting are in use; dew retting and water retting.
i) Dew retting
Dew retting is widely used in Europe as it is less labor intensive and does not have any adverse or negative environmental effects. The swathes laid on the ground and left there for approximately six weeks. The retting is influenced by heat and moisture which will be received from sunlight and rain or dew. When the stalks of the upper layers are sufficiently retted then it is turned for uniform retting. There is a self-propelled machine which carries out this turning operation. During this process, the crop is at risk due to weather conditions. Too much rain will cause partial retting of straw before retting is complete and will weaken the fibers. On the other hand, if there is less moisture the straw will not ret properly and fibers will be damaged during scotching.
Fig: Dew-retting of flax
ii) Water retting
In the water retting process, the pulled straw is tied into bundles and immersed in water, in either ponds or tanks. The retting period varies from 3 days to one week. When the retting is finished, the bales are removed and stalks are dried in the fields. The advantages of this process are that it is controllable and has no risk of weather conditions. On the contrary, this process has adverse effects on environment. The process makes the water highly polluted and requires treatment. The process has almost completely disappeared from Western Europe but is still practiced in China and Egypt.
Fig: Water retting of flax
3 . Rippling or de-seeding
Rippling means separating seeds from the crop. Stalks are pulled and are passed through a comb and the seeds are collected into bags. This is done after two or three weeks of flowering. This process is not practiced in Europe because it makes the fiber less flexible and often leads to low fiber quality. That’s why fibers produced in western Europe has better quality and fetches higher prices.
4 . Bailing and stocking
When the straw is properly retted, the swathes are lifted from the ground by a round bailer and stocked until scotching. The humidity of the straw is kept under 15 percent by covering.
Processing of Flax Fiber :
Scutching process of flax
This consists of a series of mechanical operations through which the flax straw is processed.
- Straw layer preparation : The round bales of straw are placed on an unwinding platform. The weight should be 2 kg per meter. Higher weight will reduce productivity.
- Rippling : The removal of seeds is combined with combing and straightening so that the process can be done uniformly.
- Drafting : The machine used for drafting is usually called divider. Its purpose is to decrease the linear weight of the straw layer so that each stalk can be efficiently processed afterwards. This process is done by five to ten pairs of toothed wheels.
- Breaking : The purpose of this operation is to break the woody matter from the stalks so that it can be removed by scutching turbines afterwards.
- Scutching : Scutching separates the fibers from woody matter of the stalks. The machine consists of two pairs of parallel counter rotating turbines consisting blades over which a pair of belts carry the straw. The pair ofbelts drives the straw through the blades of cylinders, which strikes and thus shiv and tow fall through the machine.
- Sorting and packing : The ‘hands’ of the line flax are graded according to color, cleanliness. They are packed into bundles of 10 kg to 20 kg and later pressed into bales of around 100 kg.
Geographical Distribution of Flax :
Fig: worldwide production of flax and linen
Flax is widely produced in Canada, western Europe, China, Indian sub-continent, USA and Russia. Flax is a plant of thermally cooler regions of the world. In the western Europe, the largest producer is France (at least 5%).
CanadaIn 2014, the worldwide flax production was about 26.5 million tons. The production led by Canada (33% of overall production). Here is a short list of top flax growing countries-
- Russia
- Ukraine
- France
- Argentina
- Italy
- Germany
- UK
- Holland
- Belgium
(1933)