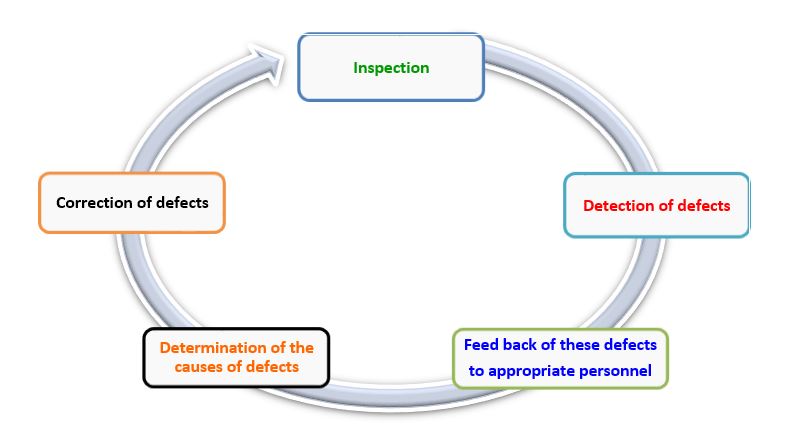
Inspection | Steps in Garments Inspection
Inspection | Steps in Garments Inspection
Inspection
Inspection can be defined, in the apparel industry, as the visual examination or review of raw materials (such as fabric, Buttons, Zippers, Sewing threads, Trims etc) partially finished components of the garments and completely finished garments in relation to some standards, specifications or requirements, as well as measuring the garments if they meet the required measurements.
For inspection, to be effective, the entire inspection loop must be completed.
Steps in garments inspection:
In garments industry, the desired or expected quality parameters are controlled by inspection. This inspection can be done in three steps:
- Raw material inspection
- In process inspection
- Final inspection
Raw materials inspection:
- Fabric inspection: 4-point system
- Sewing threads Inspection:
- Construction
- Yarn count
- Yarn ply
- Number of twists per unit length (TPI or TPM)
- Twist balance
- Yarn strength (tenacity)
- Yarn elongation
- Sew ability
- Finish
- Color
- Yardage
- Winding
- Package density
Fabric Inspection :
4 Point Inspection :
Fabric Quality is specified on the basis of 4-points system. Here is the point distribution for different kinds fault in this system
Fault | Point |
Slub | 1 Point |
Any Hole | 4 Point |
Needle/Sinker Line | 4 Point |
Needle Breakage | 4 Point |
Press Of | 4 Point |
Penalty Points Calculation:
Defective length | Penalty Points |
Upto 3” | 1 |
3” to 6” | 2 |
6” to9” | 3 |
Over 9” | 4 |
For Holes | |
Upto 1” | 2 |
Above 1” | 4 |
During quality inspection Quality Inspectors keep records of defect they found in check sheet.
Quality Points / per 100 square Yard
= ( Total Penalty Point x 36 x 1000 ) / ( Total Length Inspected in Yards x Fabric Width )
Quality Classification :
Case 1 | Case 2 | Case 3 |
<20 | 20-40 | 40> |
OK | ASK | REJECT |
Zipper Inspection:
-
- Dimension: Tape width, tape extensions, and overall useable length of zipper should be as specified.
- Top and bottom stoppers should be fastened securely.
- Zipper tape should be uniform in color.
- Zipper should not cause wrinkling and puckering after sewn into garments
- Puller or pull tab should be affixed firmly to the slider body.
- Slider should ride freely but must not be so free that it is loose on the chain.
- Slider should be locked securely.
- Zipper should be perfect and washing and / or dry cleaning and will not fade.
- Zipper should not deform under pressing and ironing.
- Zipper should be well-matched with garments design.
- Zipper should be AZO-free, nickel free,non-magnetic and nontoxic painting.
Button Inspection:
-
- Button holes should be large, clean, and free from flash, so that it will not cut the thread.
- Button holes should be located properly.
- Button thickness should be uniform.
- Button shade should be within tolerance.
- Button should be able to withstand laundering, dry cleaning, and pressing without any change or deform
- Button size should be as specified.
- In case of any special requirements button should have all.
In process Inspection:
From the starting point of manufacturing upto garments ready to shipment, the inspection done is called in process inspection. At least 65 to 80% faults can be checked and controlled through in process inspection.
Benefits or results of in process inspection:
- Reduction of major ‘surprises’ from the customers due to bad quality.
- Decrease in labor cost due to decrease in repair rates.
In process Inspection includes:
Sewing inspection/defects:
-
- Sewing defects
- Seam defects
- Assembly defects
- Finishing inspection /defects
Final Inspection:
Final inspection consists of inspecting finished garments from the buyer’s point of view; size measurements, formfitting (putting garments on the proper size dummy to see if they properly fit labeled sizes) ;and live modeling if necessary ( again to see if the garments properly fit the labeled sizes ). Final inspection may occur before or after garments are packed in poly bags and cartons . If it is done after garments packed , then proper size and style markings on the package can also be checked.
Total Acceptable Product (TAP) &Acceptable Quality Limit (AQL):
TAP means the number of acceptable products in a lot. On the other hand, AQL means maximum acceptable capability or rejected % of products in a lot.
Example:
10,000 dozen T-Shirts have AQL of 4%. Then find out TAP of that lot. Here,
100 dozens T-Shirts have acceptable limit = 4 dozens
1 dozen T-Shirts has acceptable limit = 4/100 dozen
10,000 dozens T-Shirts have acceptable limit = (4/100) * 10,000 dozens
=400 dozens
Therefore,
TAP = (10,000 – 400) dozens
=9600 dozens
Generally in garment industries, inspections are made 1%, 1.5%, 2.5%, 4%, 6.5%, 10%, etc.
This depends on the buyer’s requirements.
(456)