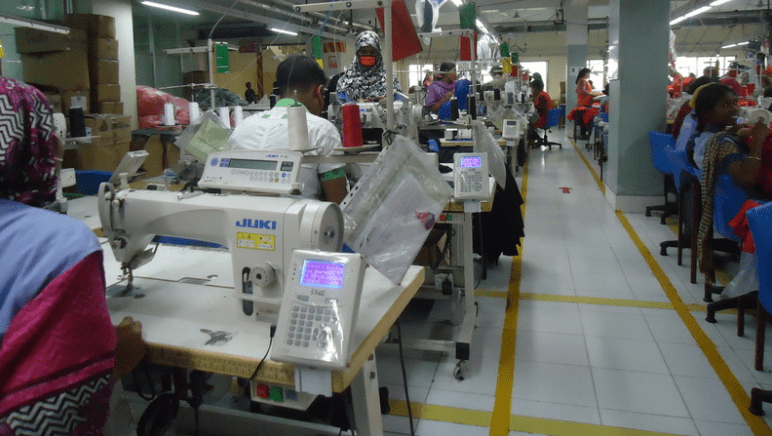
Line Balancing | Part 03
Part 01 :Industrial Engineering | Responsibilities of Industrial Engineers (IE) | Working Flow Diagram of I.E Dept. | How to conduct Time Study
Part 03 : Line Balancing | How to Balance a Traditional Sewing Line | Tools required for line balancing
Part 04 :Work Place Layout for Garments | Checklist for Work Station Design | Basic Guide to Work Place Layout
Line Balancing | How to Balance a Traditional Sewing Line | Tools required for line balancing
Line Balancing
The Line Balancing is to design a smooth production flow by allotting processes to workers so as to allow each worker to complete
the allotted workload within an even time. It is a system where you meet the production expectations and you can find the same amount of work in process in every operation at any point in the day.
How to Balance a Traditional Sewing Line
Line balancing means allocation of sewing machine according to design. A sequence of operations is involved in making a garment. In bulk garment production, generally a team workin an assembly line (Progressive Bundle system) and each operator do one operation and give it other operator to do next operation. In this way garment reached to end of the line as a completed garment. In the assembly line after some time of the line setting, it is found that at some places in the line, work is started to pile up and few operators sit idle due to unavailability of work.
When this situation happens in the line it is called an imbalanced line.
Normally it happens due to two main reasons –
- Variation in work content (time needed to do an operation) in different operations.
- Operator’s performance level. To meet the production target, maintaining smoothwork flow in the line is very important. So it is very important to know basics of quick line balancing.
How to balance an imbalanced line has been explained in the following. The main job in line balancing is to eliminate or reduce WIP (work in process) at bottleneck operations. To do that you have to know which operations are bottleneck in the line. Through capacity study and target setting you will find existing bottlenecks in the line.
Tools required for line balancing :
- Stop watches
- Spread sheet or Calculator
Step 1: Capacity study:
List down all operations (with operator name) as per operation sequence in a paper. Using stop watch cycle time (time study) for each operation for five consecutive cycles. With average cycle time calculate hourly capacity of the operators. (i.e. operation cycle time 30 seconds and total allowances is 20% then capacity is 100 pieces per hour). Draw a line graph with per hour capacity data.
Step 2: Target setting:
With the above capacity data set your target output per hour from one line. Generally it is calculated using following formula (Target per hour= Total no of operators X 60 /garment SAM). Check current hourly operator production report. Draw a straight line with target output data on the line graph.
Step 3: Identification of bottleneck areas:
Now go to the capacity study table and compare each operator’s capacity with the target capacity. Each individual operator whose capacity is
Less than the target output is bottleneck operation for the line. It is impossible to improve imbalanceline’s output without improving output of the bottleneck operations. A bottleneck operation is like a weak link chain.
Step 4: Eliminate bottlenecks from the line:
Now to eliminate bottleneck areas use following methods which suites best to your situation but don’t jump without trying initial steps-
- Club operations where possible. Where there is higher capacity than the target output, give that operator another operation with less work content. Considering machine type and sewing thread colors.
- Shuffle operators. Operations that have low work content use low performer there. And where work content is higher use high performers.
- Reduce cycle time using work aids and attachments. To assist the operator in handling parts during sewing, positioning cutting and disposing finished task, work aids, guides or attachment can be used. Think of that if possible provide operator with aids. It will reduce operation cycle time.
- Improve workstation layout and improve methods. Most important area for improving output from a particular operation is using best workstation layout and best method of work. There is always a chance that though improving method of bottleneck operations you can do line balancing.
- Add more operators at bottleneck operations. Adding one additional machine in easy task than others. Before adding one more machine compare the cost-benefits of putting additional machine into the line. It can be simple compared by estimating machine productivity in both cases.
- Do extra work at bottleneck operations. At lunch break and Tea break when each operator of the line goes for break, bottleneck operator can continue work to feed next to his operator. Later he can take break. At the end of the day tell this operator to work for one hour extra to reduce the WIP.
Example of line balancing :
- Machine layout according to style:
Process-1: Production 40 pcs by 1 machine, End production 40 pcs.
Process-2: Production 45 pcs by 1 machine, End production 40 pcs.
Process-3: Production 75 pcs by 1 machine, End production 40 pcs.
Process-4: Production 80 pcs by 1 machine, End production 40 pcs.
Process-5: Production 50 pcs by 1 machine, End production 40 pcs.
Production of this line is 40 pcs/hours.
- Line Balancing:
Process-1:Production 80 pcs by End production 40 pcs
Process-2:Production 90 pcs by End production 80 pcs
Process-3:Production 75 pcs by End production 75 pcs.
Process-4: Production 80 pcs by End production 75 pcs.
Process-5: Production 100 pcs by End production 75 pcs
Production of this line 75 pcs/hour
Action Plan for development:
Replace skill operator for process no-3, then production will be increased. When production is 80 pcs/ hour, then set target 90 pcs for process no-1, 3 & 4 and research on it, How production can be increased.
The following action can be done—
- Utilized SMV (Method motion & time study).
- Change the machine, if machine is not good.
- Appoint helper for the operator.
- Incentive can be given.
- At last overtime (OT) can be given
# Note:Line development or line balancing is continuous process. There if no end of it.
Part 01 :Industrial Engineering | Responsibilities of Industrial Engineers (IE) | Working Flow Diagram of I.E Dept. | How to conduct Time Study
Part 03 : Line Balancing | How to Balance a Traditional Sewing Line | Tools required for line balancing
Part 04 :Work Place Layout for Garments | Checklist for Work Station Design | Basic Guide to Work Place Layout
(1744)