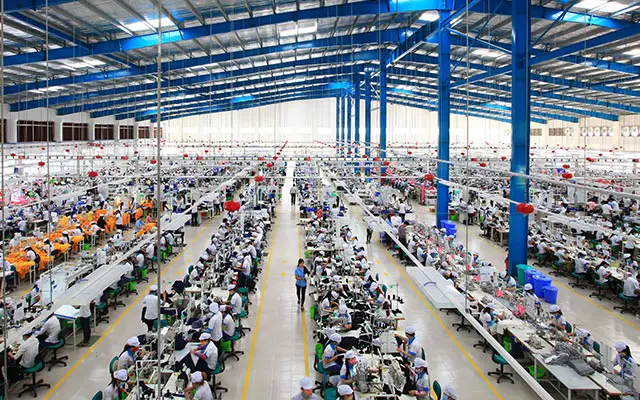
Production Planning | Function of the Planning Department
Production Planning | Function of the Planning Department
Production Planning
Production planning is concerned with deciding in advance what is to be produced, when to be produced, where to be produced and how to be produced. It involves foreseeing every step in the process of production so as to avoid all difficulties and in efficiency in the operation of the plant. Production planning has been defined as the technique of forecasting or picturing ahead every step in along series of separate operations, each step to be taken in the right place, of the right degree, and at the right time, and each operation to be done at maximum efficiency. It determines the requirements for materials, machinery and man-power; establishes the exact sequence of operations for each individual item and lays down the time schedule for its completion.
Factory Production Capacity
Factory production capacity is derived from the available at the manufacturing plant. It is calculated simply by the amount of the machines available and hours per day determined to work to be realistic one has to determine the efficiency level of the operators and incorporate the percentage to determine actual capacity.
Production capacity = No. of machine operative × Available min. in a month × Efficiency (%).
If special machine is required for the special operation its capacity should be considered.
Available min. in a month = (8×60 – 45) * 26 = 11310 minutes per month.
Factors should be considered During Accept an order:
Potential Capacity:
Potential capacity of a plan refers to the maximum capacity adjusted for the efficiency.
Potential Capacity = No. of machine operative × Available min. in a month × Efficiency (%).
Committed Capacity:
Committedcapacityanyplantreferstothetotalhourspreviouslyallocatedfortheproduction during certain period.
Available Capacity:
Availablecapacityofanyfactoryreferstothedifferencebetweenpotentialandcommitted capacity for a certain period of time.
Available Capacity =Potential capacity – Committed capacity.
Required Capacity:
SAM or SAH required producing a specified volume in a certain period of time.
Required Capacity = SAH or SAM per unit item × Number of the item.
Excess Capacity:
Excess capacity of any plant refers to the Difference between potential capacity and required capacity.
Excess Capacity = Potential Capacity- Required Capacity.
Maximum Capacity:
Maximum capacity of any plant refers to the total hours available under normal condition in a given period of time.
Example:
Consider a factory has 10 machines daily working hour 7 average efficiency of the operator 90% bringorder6000unitandgivenleadtime10days.Factoryalreadycommitted300hrs.for10 days period SAM of the item is 5 . Calculate the acceptability o9f the order.
Potential Capacity = 10 * 7 *90% *10
= 630 hrs.
Required Capacity =5*6000
=30000mins.
=500hrs.
Available Capacity = 630 -300
=330 hrs
Acceptability of the order = Available Capacity –Required Capacity
=330 – 500
=170 hrs.
Capacity is not sufficient to accept the order.
What adjustment has to be made to accept the order?
- Require more time from the buyer to accommodate 170 hrs.
- Overtime given.
- Increase the machine and operator
- Find the way to increase the efficiency level to 100%.
- Use creative production technique.
- Try to reduce the idle time
- Asses the performance of the individual operator.
Production Standards are used in production planning to do the following:
- Estimate the rate or time for completion each operation.
- Determine the required capacity for an order style.
- Determine the production start dates and completion dates for orders.
- Plan the daily volume that should have been completed.
- Determine the backup inventory needed to support the workflow.
- Determine how many operator and machines should be performing on each operation.
- Schedule specialized equipment
- Monitor the daily production delays.
Function of the Planning Department :
- Keep relation with merchandising department
- To plan production facilities in the best possible manner along with the proper systematic planning of production activities.
- Providing men, machines, materials etc. of right quality, quantity and also providing the mat the right time forms a very important factor.
- Make production schedule.
- To inform, about the difficulties or the various awkward positions expected to crop up later, to the management beforehand.
- Follow up the production process.
- Collect information about hourly production according to given target.
- Collect required information from the I.E. department i.e. SMV, Line target, No. of work station in each line etc.
- Attend pre-production meeting.
- Find alternatives to complete the production in given lead time
- Response email from other department.
So the functions of production planning and control can be summarized into two categories, which are as follows :
- Regular functions – Involves order preparation, process planning or routing concerns, fixation of method of manufacture, scheduling, dispatching, progressing, expediting etc.
- Optimal functions – Involves cost estimation, work measurement ,subcontracting, capacity planning and demand forecasting etc.
Workflow diagram of planning department :
Get order information or Sample from the merchandising department
⇓
Collect a sample from the sample section
⇓
Sample analysis
⇓
Fabric receiving from Fabric Dept.
⇓
Trims in house
⇓
Collect SMV & others information from I.E.
⇓
Discussion with sample section
⇓
Make production schedule
⇓
Capacity study
⇓
Follow up the production
⇓
Give the line target
⇓
Follow up the production process
Production schedule preparation :
From the above discussion it is clear that to prepare production plan following information are required –
Potential capacity. |
Total production. |
Available capacity. |
Total Efficiency. |
Required capacity. |
Total cost of making. |
Committed capacity. |
Total hours. |
Excess capacity |
Fabric order. |
Maximum capacity. |
Trims in house date. |
Buyer name. |
PP Approval status. |
File number. |
Fabric in house. |
Ship date. |
Pilot cut date. |
Order quantity. |
PP meeting date. |
Allocated quantity. |
Bulk production cutting date. |
SMV and cost of making per garments |
Embellishment. |
EPM (evaluation per minute). |
Probable production start date etc, as per planner requirement |
S/P (single person) TTL. |
Here,
- Allocated quantity = (production/103)*100
- Cost of making per garments = SAM* Minute cost of the labor. EPM = Cost of making per garments / SMV
- S/P (single person) TTL = SMV*Plan.
- Bulk production cutting date = PP meeting date+1
- Embellishment = Bulk production cutting date+6
- Production start date = Embellishment +1
(413)