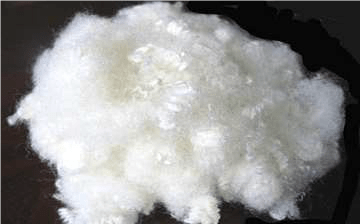
Viscose Fiber | Viscose Rayon Production | Properties of Viscose Rayon
Viscose Fiber | Viscose Rayon Production | Flow Chart of Viscose Rayon Manufacturing | Properties of Viscose Rayon | Trade Name of Viscose | End Use of Viscose Rayon
Viscose is a man-made, natural polymeric cellulose or regenerated cellulose filament or staple fiber. Viscose regenerated cellulose is obtained by the viscoseprocess. The name viscose was derived from the word ‘viscous’ which describe the liquid state of the spinning solution. A viscose solution is as thick as honey.
Regenerated Fiber:
The fiber which we get by regeneration from its main origin is termed as regenerated fiber. The regenerated fibers are divided into the following four groups-
- Cellulosic fibers- viscose rayon, cupro, modal etc.
- Cellulosic esters- acetate, tri-acetate
- Protein fibers- casein, Zeir, Azlon
- Miscellaneous– Alginate, Rubber
Why Viscose Rayon is Called Regenerated Fiber ?
Cell-OH + NaOH Cell-ONa(soda cellulose) + H2O
Cell-ONa + CS2 Cell-O-CS-SNa (sodium cellulose xanthate)
Cell-O-CS-SNa + H2SO4 Cell-OH(reg. cellulose) + Na2SO4 + CS2
So, viscose rayon is a regenerated fiber.
Chemical Reaction for Viscose Rayon Production: Regeneration Reaction
- The cellulose is treated with 17.5% solution of NaOH which converts it into soda-cellulose.
Cell-OH + NaOH Cell-ONa + H2O
- The soda-cellulose reacts with carbon disulphide to form sodium cellulose xanthate.
Cell-ONa + CS2 Cell-O-CS-SNa (sodium cellulose xanthate)
- Sodium cellulose xanthate as dissolved in a dilute solution of caustic soda. It is extruded into sulphuric acid which regenerates the cellulosenow in the form of long filaments (viscose rayon)
Cell-O-CS-SNa + H2SO4 Cell-OH + Na2SO4 + CS2
Flow Chart of Viscose Rayon Manufacturing:
Flow Chart |
Preparation of the wood pulp ( separation of cellulose from lignin) |
Steeping & pressing (formation of soda cellulose) |
Shredding ( in two or three hours, formation of crumbs) |
Ageing ( in atmospheric oxygen, D.P falls) |
Churning (formation of sodium cellulose xanthate) |
Mixing (reaction with NaOH for proper mixing) |
Ripening ( formation of reg. cellulose & stored for 4/5 days at 10~18®C |
Spinning (extrusion through spinneret) |
Description of Viscose Rayon Manufacturing:
1 . Preparation of the wood pulp: viscose rayon is produced from special variety of wood. But wood contains lignin other than cellulose. There the first stage for producing viscose rayon is to purify cellulose from wood. Here the barks are removed and Woods are chipped into pieces & treated with Ca(HSO3)2. Then these treated chips are cooked with steam under pressure for 14 hour.
2 . Steeping & pressing: This prepared wood pulps contain about 90 to 94% of pure cellulose. They are first conditioned by storing in a room at a definite humidity and temperature. The pulps are then soaked in a 17.5% solution of NaOH for 1 to 4 hrs.
3 . Shredding: The shredding m/c consists of a drum inside which revolve a pair of blades with serrated edges. In 2 or 3 hrs they break it up into fine ‘crumbs’( break into very small pieces).
4 . Ageing: After shredding, the crumbs are aged. They are contained in a galvanized vessel with a lid and through oxidation with atmospheric oxygen, degradative changes set in. some depolymerisation occurs and the degree of polymerization falls from about 5000 to 350 in this process. The higher the temp. the more rapidly does ageing.
5 . Churning: After ageing, the soda cellulose crumbs are introduced into rotating air-tight hexagonal churns. About 10% of their own (crumbs) weight of CS2 is added and the crumbs and CS2 are churned up together. As a result, a deep orange gelatinous sodium cellulose xanthate is formed.
6 . Mixing: In the mixers, the sodium cellulose xanthate is stirred with dilute caustic soda(NaOH) solution for 4 to 5 yrs, the vessel being cooled. The xanthate dissolves to a clear-brown viscous liquid similar in appearance to honey. This liquid is known as viscose but is still too impure, too young to spin.
7 . Ripening: The sodium cellulose xanthate reacts with H2SO4 & form regenerated cellulose. The viscose solution is stored for 4 to 5 days at 10-18®C and during storage it ripens. During the ripening the viscosity at first falls and then rises, so that by the time the solution is ready to spin, the viscosity has risen almost to its original value.
8 . Spinning: when the viscose solution is ripe, it is forced to be fed in the spinneret of a spinning unit with additives to form viscose.
The Polymer System of Viscose Rayon:
The polymer system of viscose is rather similar to that of cotton. However, there are some differences. The viscose polymer system is very amorphous, being about 35% crystalline and about 65% amorphous. Its relatively short polymers make it difficult to achieve a more crystalline polymer system.
Physical Properties of Viscose Rayon:
- Moisture absorption: viscose rayon absorbs moisture than cotton. The very amorphous polymer system of viscose as well as its polar polymers make viscose the most absorbent fiber in common use. Under standard conditions (65% R.H and 70®F) the moisture regain% of viscose rayon is 12-14%.
- Tenacity: Its tenacity is about 2.6 gms/denier in dry state. The wet strength of viscose rayon is about 1.4 gms/denier.
- Elongation at break: The elongation at break of viscose rayon is about 20%.
- Elasticity: The elasticity of viscose rayon is not high. If stretched and then released from strain it does not return quite to its original length. In general, elasticity of viscose rayon is less than 2~3% after which creep develops.
- Density: The specific gravity of viscose rayon is 1.52.
- Heat conductivity: viscose rayon has a lower heat resistance and poorer heat conductivity than cotton. The reason for this is its amorphousness of polymer which enables it to absorb water molecules very readily. It tends to break a significant number of hydrogen bonds. Broken hydrogen bonds prevent the retention of any heat-set.
Chemical Properties of Viscose Rayon:
- Effect of acid: Acids attack viscose rayon more quickly than they do cotton. Here temperature is a factor. Cold solutions of acids and short time of treatment do not usually weaken the fiber. But viscose rayon is attacked by hot dilute or cold concentrated mineral acids which weaken and disintegrate the fiber.
- Effect of alkali: Concentrated alkali will cause swelling and reduce strength. But weak alkali does not damage viscose.
- Effect of bleaching: viscose rayon can withstand both oxidizing and reducing bleaches but attacked by strong oxidizing bleaches. Sodium hypochlorite is the most satisfactory bleach for viscose rayon.
- Effect of solvent: Good resistance to organic solvents.
- Biological resistance: Microorganisms like moulds, mildew, bacteria etc. discolor and weaken viscose rayon.
- Resistance to light: Prolonged exposure to sunlight forms photocellulose and thus weakens viscose rayon.
Trade Name of Viscose:
- Zantral – USA
- Avril – USA
- Fibro HSO – USA
- Grasim – India
End Uses of Viscose Rayon:
- Viscose rayon is suitable for all normal textile needs but it’s not suitable for such purposes as sea-ropes, fishing lines, fishing nets, insect netting or materials subjects to chemical contact.
- Hose, underwear and dress-goods are made from viscose rayon
- Linings are particularly good in viscose rayon
- Curtains, chair coverings, transport furnishings, table cloths, cushions, bedspreads, quilt covers, lace, fine fabrics for bridal and evening gowns, day and afternoon dresses, beach and sportswear and underwear.
Some Regenerated Cellulose Fibers:
- Cupro or cupprammonium rayon, n=250
- Tancel/lyocel, n=280
- Polynosic/modal, n=300
- Viscose rayon, n=175
The name of some high tenacity viscose rayons are-
- Tensco – Durafil
- Cordura – forfisan
(4491)