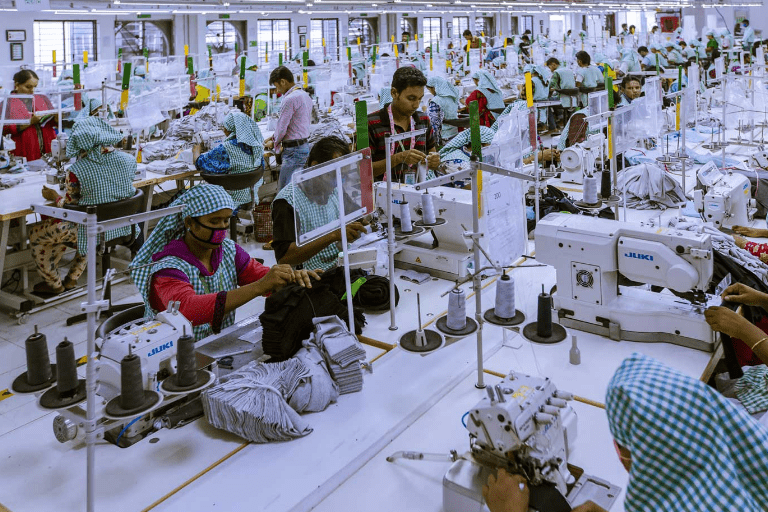
Progressive Bundle System
Part 1: Garment Production System | Apparel Production System
Part 2: Progressive Bundle System
Part 3: Unit Production System | Overhead Production System | Hanger Production System
Part 4: Modular Production System | Cellular Garment Manufacturing | Toyota Sewing System
Progressive Bundle System (PBS)
The progressive bundle system is a traditional production system that has been widely used in the apparel industries for many decades and still is today. In this system bundles of garments parts are moved in sequence from one sewing machine operator to the next. Each worker receives a bundle of unfinished garments and performs a single operation on each garment in the bundle. After finished of his/her work on a bundle, they are re-tied the bundle and passed on to the next operator. Each PBS task is given a target time or “SAM” (Standard Allowed Minutes). Time study engineers calculate the SAM for an entire garment for an experienced worker as the sum of the number of minutes required for each operation in the production process, including allowances for worker fatigue, rest periods, personal time and so on. The success of PBS depends on how the production system is set up and used in a plant.
In the cutting section cut components of one style and in one size are clubbed and bundled using ties. Bundle sizes could vary from 2 to 100 pieces according to the requirement of the production plant. Each bundle contains pieces of the same style and same size only. A ticket number will be allotted to each bundle which represents style, size, shade of the garments and number of cut pieces etc.
The bundles of cut parts are transported to the sewing section and given to the operators scheduled to finished the operation. Thus bundles may be handled from one sewing station to another in various form such as tied bundles, bags, pocketed bags, bundle trucks, boxes and baskets etc.
Fig: Progressive Bundle System (Courtesy: Plummy Fashion)
Features of progressive bundle System
Sewing operations are laid out in sequence.
Each operator receives a bundle, does his work, reties the bundle and passes it to
the next operator.
The garments are gradually assembled as they move through successive sub-assembly and main assembly operations in bundle form.
There is a storage facility such as rack, bin or table for storing the inter-process
work between each operation.
The work is routed by means of tickets.
The use of the system decrease as firms seeks more flexibility.
Machines and operations are organized into sections according to basic functions,
which produce subcomponents.
Within each section, works are balanced according to the time required for each sub-function.
The amount of machinery for each operation is determined by the output required.
This system is the most widely used system in the garment industry today.
It is used in shirt factories, jeans factories, jacket factories, etc.
Advantages and Disadvantages of Progressive Bundle System
Advantages
It allows high productivity.
A high level of labour utilization can be achieved and helps in reducing time and cost.
An uniform high quality of work can be ensured by in-process control.
Labourers of all levels (unskilled, skilled, semi-skilled labours) are involved in this system where the operations are broken into simple operation. Hence the cost of labour is very cheap.
Individual performances can be monitored and incentives offered.
Due to bundle system, less chance to lot mix-up, size and shade variation of cut garment pieces.
Tracking of bundles is possible, so identifying and solving the problems becomes easy.
An efficient production control system and quality control system could be implemented.
Small bundles allow faster throughput unless there are bottlenecks and extensive waiting between operations.
Disadvantages
Time-consuming due to assembling, moving, tying and untying of bundles.
Line balancing becomes difficult most of the time and this problem is solved by effective production supervisor and IE Engineers.
Slow processing, absenteeism, and equipment failure may also cause major bottlenecks within the system.
Large inventory, extra handling and difficulty in controlling inventory.
Inventory cost will be high due to higher WIP in each.
Proper planning is required for each batch and for each style, which takes lot of time.
Variety of styles and less quantity is not effective in this system.
Part 1: Garment Production System | Apparel Production System
Part 2: Progressive Bundle System
Part 3: Unit Production System | Overhead Production System | Hanger Production System
Part 4: Modular Production System | Cellular Garment Manufacturing | Toyota Sewing System
(9074)