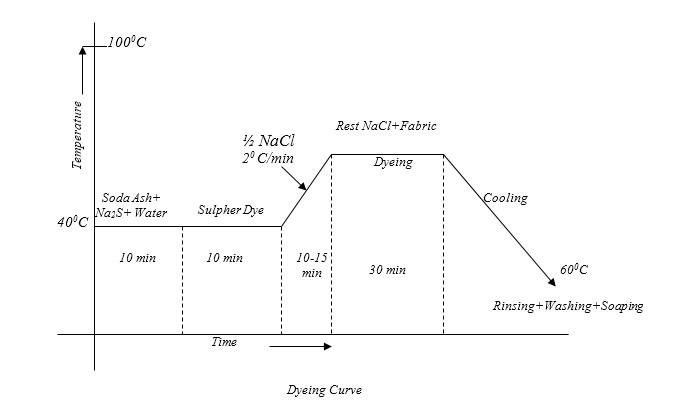
Classification of Sulpher Dyes Part 2
Part 01 :Introduction to Sulfur Dyes | History of Sulfur Dyes | Method of manufacture of Sulfur dye | Trade Names of Sulfur Dyes | Characteristics of Sulfur Dyes | Features of Sulfur Dye | Chemical Structure of Sulfur Dye | Chemical Nature of Sulfur Dyes | Chemistry of dyeing with Sulfur Dye
Part 03 :Defects of sulfur Dyeing | Bronziness of Shades | Causes of Bronziness of Shades | Remedies of Bronziness of Shades | Sulfur Black Tendering | Causes of Sulfur Black Tendering | Remedies of Sulfur Black Tendering | Stripping of Sulfur dyes | Uses of Sulfur Dye | S-Radical in Sulfur dye | Colors/Shades found from Sulfur dyes | Causes for the Popularity of Producing Black Shades with Sulfur Dyes | Comparison between Sulfur & Vat Dyes | Reasons for why so called
Classification of Sulpher Dyes:
Sulpher dyes may be classified in many ways:- But according to their solubility there are essentially 3 classes of Sulpher dyes as below:-
- Conventional or Water insoluble dyes
- Leuco Sulpher dyes (Partially soluble) and
- Solubilised Sulpher dyes.
These in turn are subdivided in to 6 sub classes, depending on the method of application. Namely–
- Method i
- Method ii
- Method iii
- Method iv
- Method v
- Method vi
Method-i:
Conventional Sulpher dyes (i.e. water insoluble Sulpher dyes) are dyed in method i. They have slight affinity to textile fibres of cellulosic origin. Method is as below:-
Dye pasted with cold waterà Add required amount of Na-sulphideà Dissolved by adding boiling waterà Boiled for 100 minutes to complete desolationà Taken in dye bath containing soda ashà Material immersed in dye bathà Raising temperature & adding Glauber’s salt for exhaustion.
Method-ii:
These dyes are also insoluble in water and are called specialized conventional Sulpher dyes. Its application method is as below:-
Pasting of dye with 25-30 times soft water and reducing agent à Dissolved dye added to dye bath (mixture of soda ash & rongalite C) and boiled for sometimeà Material put in dye bath and dyeing carried out for 20 minutes à for exhaustion common salt or Glauber salt is added and dyeing continued for 30-40 minutes.
Method-iii:
This method is used for leuco Sulpher dyes; they have distinct affinity for cellulosic fibres. These Sulpher dyes are dyed as in the case of method –I except that little or no Na-sulphide is required for their volatilization.
Method-iv:
These dyes are soluble in water having substantivity to cellulosic fibres. They are mixture of Sulpher dyes and Na- sulphide. The dyeing method is as below:
Dye pasted with little amount water at 300Cà Diluted with 10-20 times water at same temperatureà Dissolved dye is added to required quantity of water in dye vessel à common or Glauber Salt and soda ash is added in dye bathà Material is put in dye bath and kept at 400-600C for 25-30 minutes.
Method-v:
These dyes are also soluble in water & are substantive to cellulosic fibres. They are dry mixture of the dyes and Rongallite-C. The dyeing method is as below:
Dye pasted with water & dissolved by boiling at 10-20 times soft water à Solution is added to dye bath containing required amount of waterà Temperature is raised to 900 c à material is entered in to the dye bath after 20 minutesà Glauber salt is added & dyeing continued for some times.
Method-vi:
These dyes are solubilized Sulpher dyes. They have no affinity towards cellulosic fibres. Chemically they are thio-sulphuric acid derivatives and are applied either by Na-sulphite method or by Na-Hydrosulphite method.
Some oxidizing and reducing agent
Oxidizing Agent |
Reducing Agent |
Potassium Dichromate(K2Cr2O7) |
Sodium Sulphide (Na2S) |
Acetic Acid(CH3COOH) |
Sodium Hydro sulphide(NaHSO3) |
Sodium Perborate |
Thioglycolic acid |
Sodium per carborate |
Thio Salicylic acid |
Sodium peroxide(NaO2) |
Pseudo thiohydantion |
Hydrozen peroxide(H2O2) |
Reducing Steps of Sulfur Dyes
Reducing step is the most important in the application of Sulpher dyes. Unless the dyes are converted in to the completely soluble form, the full colour value cannot be achieved. The solubility of reduced Sulpher dyes varies appreciably from dye to dyes. For example yellow Sulpher dyes are the last soluble dyes (i.e. most insoluble dyes)
The reducing agents are used for Sulpher dyes are:-
- Na-Sulphide.
- Na-Hydro Sulphide.
- Thioglycolic Acid.
- Pseudo-Thio-Hydantion.
But Na Sulphide is the most widely used reducing agent for dissolving Sulpher dyes. They may be replaced by Na-Hydrosulphide in some cases. But the latter is a more powerful reducing agent. So, over reducing of the dye may take place, leading to a product having lower affinity for cellulosic fibres. Hence lower colour yields are obtained along with wastage of dyestuff. In some cases lower wash fastness results if Na-Hydrosulphide is used. It also decreases the life time of the vessel.
For dissolving the Sulpher dyes, reducing agent is taken according to the weight of dye. In practice, they are taken at same weight. For example, 10 gm dye is mixed with 10 gm reducing agent. Then the mixture is boiled after adding necessary amount of water to get a good solution. For this wooden vessel or enameled iron vessel are used but not iron vessels. Because iron reacts with Sulpher.
Oxidation Step of Sulfur Dye:
After dyeing the reduced water soluble form of the dyes have to be converted in to the original water insoluble form by oxidation. The commonly used oxidizing agents are-
- Potassium dichromate
- Na-Perborate.
- Na-percarborate.
- Na-peroxide.
The method of oxidizing selection plays an important role in the development of correct shades & their optimum fast5ness properties. Rinsing off the dyeing should be done rapidly to remove as much as Na-Sulphide as possible. If even after washing some Na-sulphide or Soda-ash stays on fabric, we use CH3-COOH to neutralize them. Using of different oxidizing agents may give following results-
- Use of perborate or percartborate in presence of acetic acid gives brighter shade.
- Treating dyed material with dichromate without rinsing reduces colour losses but causes dull shade.
The chemistry of oxidization is as below:-
Dyeing of Cellulosic Fibres with Sulfur Dyes:
The sequence of dyeing with Sulpher dyes is as following:
Goods Preparation
↓
Dye Solution preparation
↓
Dyeing
↓
Oxidation
↓
After treatment
↓
Dyed Goods
Typical Recipe for sulfur dyeing:
The Typical recipe for dyeing is as below:-
Sulpher Dye : 10% (On the weight of the fabric)
Na2S (Reducing Agent) : 1.5%(on the weight of the Dye)
Salt : 8 gm/litre(NaCl)
Soda Ash (NaCO3) : 7 gm/litre
Temperature : 1000C
Time : 90 minutes
Material: Liquor : 1:20
Sometimes a chelating agent EDTA is added to chelate any metal salt extracted from the cotton goods & effectively remove these ions from the dye bath. This is necessary to prevent a harsh texture forming on a textile.
Good Preparation:
Only normal pretreated fabric (scoured, bleached) is required. Mercerized cotton goods causes an increased colour yield of 30-40%, But goods bleached by Na-Hypochlorite should not be dyed by Sulpher dyes:
Dye solution preparation or Reducing Step:
Required amount of dye, soda ash & Na2S are taken in a beaker and a little amount of cold water is added to make a paste. In a separate vessel the rest of the water is boiled and the paste is added to it. Then the mixture is boiled for 5 minutes to make the dye completely reduced.
Dyeing:
At first dye solution is taken in a dye bath & the fabric is immersed in that solution. Then it is heated for 10-15 minutes. Then half of the total NaCl solution is added and temperature is raised to boil & then the rest amount of NaCl is added. Dyeing at this temperature is continued for about 30 minutes. Then the steaming is turned off and the application continued in cooling liquor for a further half hour. This steaming helps to diffuse the dye in to the fabric before fixing. Retained dye liquor should be rinsed out immediately from the surface of the fabric.
Oxidation:
After dyeing the reduced water soluble form of the dye should be make insoluble by oxidation, to fix it on the fabric permanently. For this oxidation, we may use K2Cr2O7, CH3COOH. Na-perborate, Na2O2 etc. The typical recipe of oxidation is as below:
Na-Perborate : 0.5-1 gm/litre
Temperature : 40-500C
Time : 20 minutes.
After treatment:
- The dyed substance is soaped which makes the colour bright and makes shade permanent.
- The light fastness property of Sulpher dyes which is generally good can be improved by after treatment with certain metallic salts. Thus a treatment with CuSO4 & CH3COOH in presence of K2Cr2O7 improves the light fastness. When the dichromate is also present the washing fastness is slightly improved.
The following recipe is used for after treatment:
CuSO4 Solution : 1-2% (on the weight of goods)
CH3COOH (60%) : 1-2%
Temperature : 700C
Time : 20-30 Minutes
Precaution in the dyeing process:
The precautions in the dyeing process with the Sulpher dyes are mentioned below:-
- In the application of Sulpher dye, the dye bath should not contain Ca- Salts. If they are present in the form of insoluble co-compounds with the Sulpher dyes which precipitated easily in closed machines and form sludge when restrict the circulation of the dye liquor.
- The dye should be dissolved with soda.
- Great care should be taken during reduction process because over reduction should lower the affinity of dye towards the fibre. As a result dull shade will appear and a lot of dye stuff will go to waste.
- Fabric must not to expose to air during dyeing to prevent precipitation & oxidation. This will cause uneven dyeing.
- To prevent uneven dyeing in the fabric selvedge more amount of Na2S or NaOH and salt should be added in case of the jigger dyeing machine.
- To prevent the broziness the dye liquor should not be very worm.
- Goods dyed with Sulpher black should be after treated with a solution of K2Cr2O7 followed by rinsing. This will prevent Sulpher black tendering.
Control of Dyeing:
Reduced Sulpher dyes are similar to direct dyes. Because they can also be exhausted by adding common salts (NaCl) or Glauber’s salt (Na2SO4.10H2O) to the dye bath.
Sodium bi sulphite (NaHSO3) and ammonium sulphate {(NH4)2SO4} may also act as exhausting agents. Especially in dyeing combination shades. NaHSO3 is an acidic salt and (NH4)2SO4 is an acid liberating agent. They reduce the pH of dye bath and produce 15-20% deeper shades than common salt, when used as the exhausting agent. But the shades produced in presence of them are less bloomy and dull.
When NaHSO3 is used alone the rate of exhaustion is low but the produced shade is brighter and bloomier than common salt (NaCl) dyeing.
The use of the exhausting agents causes wastage of dye but as the Sulpher dyes are relatively cheap this wastage is not considered. Especially in case of medium & light shades.
Topping of Sulpher Dyes:
Sulpher dyes act as mordents for the basic dyes. The cotton textile materials dyed with Sulpher dyes can be topped with basic dyes for brightening the shades. So, topping of Sulpher dyes is one kind of re dyeing by which required brighter shades are obtained.
For topping of Sulpher dyes, at first dyed materials (dyed with Sulpher dyes) is washed thoroughly to remove the alkali from the fabric. Then the fabric is treated with basic dye in a second dye bath containing acetic acid of alum. In this bath temperature is raised about 600C to control the exhaustion of basic dye.
Improving of Fastness Properties:
The light fastness of the Sulpher dyes which is generally good can be improved by after treatment with certain metallic salts. Thus a treatment with CuSO4 & CH3COOH in presence of K2Cr2O7 or Na2Cr2O7 improves the light fastness. When the dichromate is also present the washing fastness is slightly improved. In actual practice the following after treatments are given: –
CuSO4 Solution : 1-2% (on the weight of goods)
CH3COOH (60%) : 1-2%
Temperature : 700C
Time : 20-30 Minutes
Or
Na2Cr2O7 : 1-1.5 %( on the weight of goods)
CuSO4 Solution : 0.5-1%
CH3COOH (60%) : 1-2%
Temperature : 700C
Time : 20-30 Minutes
The latter one also improves the washing fastness of Sulpher dyed textile materials.
Reference
- Broadbent A D 2001 Basic principles of textile coloration Society of Dyers and Colourists p 566
- Shenai V A Chemistry of Dyes and Principles of dyeing
- Carr C M 1995 Chemistry of the Textiles Industry (Dordrecht: Springer Netherlands)
- Chakraborty J N Fundamentals and Practices in Colouration of Textiles
- John Wiley & Sons Inc 2000 Kirk-Othmer Encyclopedia of Chemical Technology (Hoboken, NJ, USA: John Wiley & Sons, Inc.)
- Ühnel G E R D K, Aktiengesellschaft B, Olff J O W, Ag B, Uppert G Ü R, Aktiengesellschaft B, Chmitt M I S, Aktiengesellschaft B, Etired C H H E I D R, Ag C, Etired M A X H Ü R, Aktiengesellschaft H, Etired H E L E R and Aktiengesellschaft B 2016 Textile Dyeing , 2 . Dyeing of Cellulose Fibers 1–27
- Hunger K 2003 Industrial Dyes: Chemistry, Properties, Applications
- Rahman M M Wet Processing 1
- Iqbal M 2008 Textile Dyes 167
- ARNOLD R. LANG DYES AND PIGMENTS: NEW RESEARCH
(989)