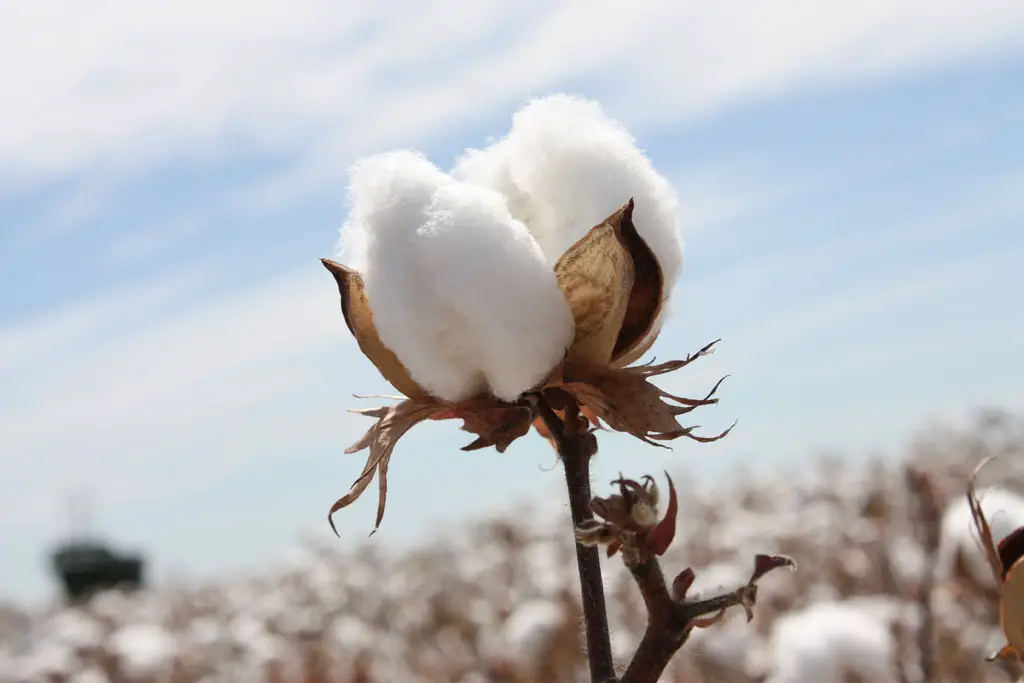
Properties of Cotton Fibers
Properties of Cotton Fibers Considered by Cotton Spinners
Spinning Technology for Cotton Fibre:
Flow chart of carded yarn production:
Input |
Machine |
Output |
Bale |
Blow Room |
Card mat |
Card mat |
Carding |
Card sliver |
Card sliver |
Breaker draw frame |
Drawn sliver |
Drawn sliver |
Finisher draw frame |
Drawn sliver |
Drawn sliver |
Simplex |
Roving |
Roving |
Ring |
Yarn |
Flow chart of combed yarn production:
Input |
Machine |
Output |
Bale |
Blow Room |
Card mat |
Card mat |
Carding |
Card sliver |
Card sliver |
Breaker draw frame |
Drawn sliver |
Drawn sliver |
Lap former |
Lap |
Lap |
Comber |
Combed sliver |
Combed sliver |
Finisher draw frame |
Drawn sliver |
Drawn sliver |
Simplex |
Roving |
Roving |
Ring |
Yarn |
Properties of cotton fibers considered by cotton spinners:
1 . Fiber fineness: Fiber fineness is measured in Micronaire value (MIC). The higher the micronaire value of fiber the coarser the fiber.
Rating of MIC value-
MIC |
Description |
Less than 3.0 |
Very fine |
3.0~3.6 |
Fine |
3.7~4.7 |
Medium |
4.8~5.4 |
Coarse |
5.5 to above |
Very coarse |
Fiber fineness influences the number of fibers in the cross section of yarn. The finer the fiber the higher the number of fiber in yarn cross section.
2 . Maturity: The maturity of cotton is defined in terms of the development of cell wall. A fully mature fiber has a well developed thick cell wall. On the other hand, an immature fiber has a very thin cell wall.
M.R. = | 0.85 | Good fiber |
M.R. = | 0.75 | Average fiber |
M.R = | 0.65 | Poor fiber |
Immature fiber leads to :
- Nepping
- Loss of yarn strength
- Varying dye ability
- High proportion of short fibers
3 . Fiber length: The average length of spinnable fiber is called staple length. The quality, count, strength etc. depend on the staple length of fiber. Normally the higher the staple length of fiber the higher the yarn quality.
Staple length |
Category |
1” or less |
Short staple |
1 ” to 1 ” |
Medium staple |
1 ” to 1 ” |
Long staple |
4 . Fiber strength: The higher the fiber strength the higher the yarn and fabric strength. Very weak cottons tend to rupture during processing both in blow room and carding, creating short fibers and consequently deteriorate yarn strength and uniformity. Minimum strength for a textile fiber is approximately 6 CN/tex.
Some significant breaking strength of fibers are:
Polyester | 35~60 CN/tex |
Cotton | 15~40 CN/tex |
Wool | 12~18 CN/tex |
5 . Fiber cleanness: In addition to usable fibers, cotton stock contain foreign matter of various kinds:
Vegetable matter – Husk portions, seed fragments, stem fragments, leaf fragments wood fragments.
Mineral material – sand, dust, coal.
Other foreign matters – metal fragments cloth fragments, packing materials.
Accepted the range of foreign materials to the bale:
Up to 1.2% | Very clean |
1.2% to 2.0% | clean |
2.0% to 4.0% | Medium |
4.0% to 7.0% | Dirty |
7.0% to above | very dirty |
According to the international committee for cotton testing methods the following types are to be distinguished:
Trash | above 500 µm |
Dust | (50~500)µm |
Micro dust | (15~50)µm |
Breathable | below 15 µm |
6 . Fiber color: color is particularly important as a measure of how well a yarn or fabric will dye or bleach. Instrumental techniques for determining the color of the sample have only now reached the industry, HVI measurement of color provides reasonably accurate results of average reflectance and yellowness in a sample.
7 . Fiber elongation: Elongation is specified as a percentage of the starting length. The greater crease-resistance of wool compared with cotton arises
for example from the difference in their elongations, cotton-6~10%, wool-25~45%
(2308)