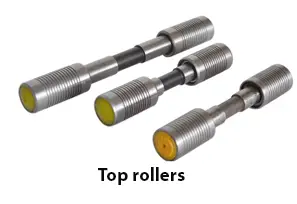
Speed Frame Machine Components
Speed Frame Machine Components
The important parts of speed frame are given as follows:
❶ Bottom rollers
❷ Rubber-covered top online rollers
❸ Top arm
❹ Aprons (top and bottom)
❺ Spacer
❻ Condenser (inlet and floating)
❼ Top arm
❽ Flyer
❾ Spindle
❿ Pressure arm
Top Rollers
Top rollers are held strictly parallel to and in perfect alignment with bottom rollers.
Top rollers covered with rubber cots play a significant role in the control of drafting irregularities.
The hardness of top rollers is between 80° and 85° Shore, but the rollers over which the apron runs often have a hardness only slightly above 60° Shore. This permits better enclosure and guidance of the fiber strand during drafting.
The top rollers must be pressed with relatively high force against the lower rollers to ensure guidance of the fibers. 100- 300 N per roller is normally applied depending on raw material and volume of fibers.
The fiber or dust accumulation in the top roller neck should be cleaned frequently using picker gun.
Bottom Rollers
Bottom rollers are made of steel
The bottom rollers of speed frame exercise immense influence on the quality of roving.
Precise concentricity of a bottom roller is a function of improved roving quality (evenness and strength).
Bottom rollers having narrow tolerances of dimensions B, p, and T (Figure) produce fault-free roving.
Eccentric or damaged bottom rollers, especially front bottom rollers, are the most common cause of unnecessary roving faults and excessive roller laps.
Top Arm
Spring loaded top arms are normally adopted in speed frame to get optimum pressure on top rollers to achieve required quality and performance. The top arm pressure and roller setting influence the roving quality and subsequently yarn quality.
Aprons
Aprons are one of the most effective means to support the floating fibers and drastically reduce the drafting wave. Apron wear is accelerated by high drafts and sliver linear density.
It is essential that the aprons should extend as closely as possible to the nip line of the front rollers.
The top apron is short and made of synthetic rubber that has a thickness of about 1 mm. Bottom apron is larger and made of the same material as the upper one.
Basically, synthetic aprons are made in an endless tubular form whereas leather aprons are made in open strips that are subsequently glued together to form an apron.
The advantage of tubular construction is seamless and uniform along its circumference.
The length of the aprons also called as the cradle length is kept approximately equal to the staple length of the fibers. The cradles for different staple length are shown in Figure.
Cradle lengths according to the fiber length
Spacer
The distance between top and bottom aprons is maintained by a small component called “cradle spacer” or “spacer,” which is inserted between the nose bar of the bottom apron and the cradle edge of top apron. The selection of spacer for a process depends on the hank of the sliver, break draft, and roving hank.
Spacer size of different roving hanks
Advantages and disadvantages of reducing the spacer size
Condenser
Condensers placed in the drafting zone help to prevent the fiber strand from spreading apart during drafting.
Condensers can be classified as feed (or inlet) condenser, middle condenser, and delivery (or floating) condenser (Figure).
Feed condenser is used just before the back pair of drafting rollers. The middle condenser is used near the nip of the middle pair of rollers and the third one is used just before the front pair of rollers.
The main function of the feed condenser is to lead the sliver properly into the drafting arrangement.
The main function of the last two guides is to bring back the fiber mass into a strand that tends to tear apart because of the drafting action.
The size of condensers should be selected according to the volume of the fiber sliver (Table).
Condenser size and color for different sliver hanks
Flyer
The flyer is a special component of the roving frame that helps to insert twist in the roving. The flyer speeds employed normally range from about 1000 to 1400 rpm. The flyers’ special shape offers less air resistance, preventing roving breakages. The features of a good flyer are summarized as follows:
It should improve the quality of twisting by inserting false twist.
The flyer should produce balanced running condition, especially at higher speed.
The design and quality of the metal of flyer should be such that there is no chance of spreading of flyer.
There should be provision for slight changes in roving tension.
There should be facility for easy and simple doffing operation.
It should be maintenance friendly.
Spindle
A spindle is a long vertical cylindrical shaft on which the flyer is mounted at the top. The spindle is mounted at its lower end in a bearing and the bobbin tube acts as neck bearing. Flyer through spindle is driven by a set of gears housed in the spindle rail, which is stationary. Spindle speed and flyer speed are same. The arrangement of a spindle and a flyer is shown below:
The Presser Arm
Presser arm is attached to the lower end of the flyer”s hollow leg. The arm has to guide the roving from the exit of flyer leg to the package. The presser arm maintains certain tension on the roving which is necessary for proper compact winding. The number of turns around the preset arm determines the roving tension and package hardness. If it is high, then a compact package is obtained. The number of turns depends upon the fiber type and twist in the roving.
(4849)