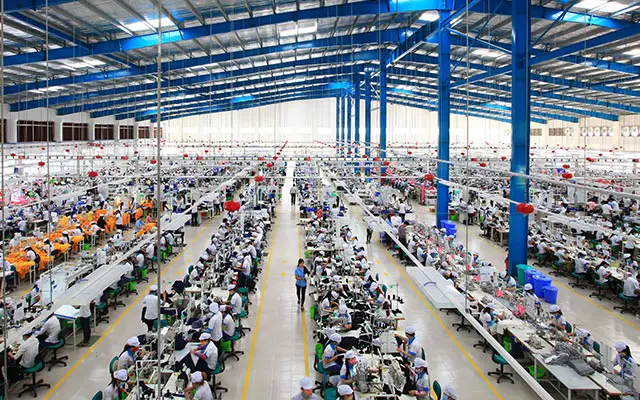
Industrial Engineering | Part 01
Part 02 :Work Study | Parts of Work Study | Method Study | Objectives of Method Study | Steps of Method Study
Part 03 : Line Balancing | How to Balance a Traditional Sewing Line | Tools required for line balancing
Part 04 :Work Place Layout for Garments | Checklist for Work Station Design | Basic Guide to Work Place Layout
Industrial Engineering | Responsibilities of Industrial Engineers (IE) | Working Flow Diagram of I.E Department | Time Study | Time study tools | How to conduct Time Study
Industrial Engineering is the application of engineering method to get optimum output using the existing facilities of integrated systems consists of people, materials, information, and equipment’s energy.
It was just couple of years back that the demand of an Industrial Engineer has increased many times. Reason an Industrial Engineer can do a lot to improve performance of the company.
Without having such tools earlier production managers and line supervisors faced difficulty in measuring work content, garment costing, and production planning correctly, even it was difficult to finalize orders. IE have worked to find out important tasks those are important for an engineer, and needs detailed understanding of production fields, included in the following. Though job profile of an Industrial Engineer varies from company to company, most of the job profile fall under following list.
Responsibilities of Industrial Engineers ( IE ) :
- Knowledge about various sewing production systems.
- Knowledge of all types of Sewing machine necessary for the company.
- Time study (Cycle timing).
- Motion analysis of the operations.
- Operations break down.
- Preparation of OB (Operation bulletin).
- SAM Calculation.
- M/C Layout and Work station layout
- Line Set up.
- Production estimation of a line.
- Work Sampling.
- Method Study (Seeing Movements of an operation).
- WIP Control.
- Line Balancing.
- Capacity study.
- Cost estimation of a garment.
- Developing and Maintaining Skill Matrix.
- Incentives schemes.
- Calculating Thread Consumption.
- Work aids, Guide and Attachment.
- Performance Rating.
Working Flow Diagram of I.E Department :
Get order information or Sample from the merchandising department
Collect a sample from the sample section
Sample analysis
Time study or Follow GSD
Determine SMV
Inform SMV to merchandising & Planning department
Operation Breakdown
Line layout
Capacity study
Method study
Line balancing
Give the line Target
Follow up the production process
Time Study
Time study is a method of measuring work for recording the times of performing a certain specific task or its elements carried out under specified conditions. An operator does same operation (task) throughout the day. Time study help to define how much time is necessary for an operator to carry out the task at a defined rate of performance.
- A stop watch
- Time study format
- One pen or pencil
How to conduct Time Study?
An operation cycle consists of material handling, positioning and aligning parts, sewing, trimming threads and tying and untying a bundle. So in the time study format, divide whole task into various elements according to the motion sequences of the operation. For example, in operation ‘collar run stitch’ task elements may be
- Pick up panel to sew first seam.
- Turn collar to sew second seam.
- Turn collar to sew third seam.
- Check work and dispose Waiting for next pieces.
Step 1: Preparation
- Ready with stationeries like time study format, stop watch (digital one) And pencil
- Select one operation for Time study
- Tell the operator that you are going measure time he/she taking to do the Job.
- Observe the operation carefully and break down operation into elements.
- Fill the basic information in the time study format. Like machine Category, guide or attachment used.
Step 2: Time capturing
Now measure the time taken for completing each elements of the operation cycle by the operator. Time should be captured in seconds. Similarly, capture element timing for consecutive 5 operation cycles. During data capturing only note down reading of the stop watch and later calculate element timing. If you found any abnormal time in any elements record time during time study and later discard that reading. Or you capture time for one more cycle. Abnormal time may be occurred due to bobbin change, thread break, power cut or quality issues.
Step 3: Calculation of Basic time
From the Reading (R) calculate time taken for each element for all five cycles just by deducting previous Reading from elemental reading. Sum up times of five cycles for each element. Note, if
you discard any reading than in that case no. of cycles will be four. Calculate average element times. This average time multiplied by rating of the operator that’s called basic time. Rating given on the basis of following-
- Stillness about the job.
- Encouragement to do the job.
- His/her concentration.
- Physically or mentally fitness for the job.
Step 4: Calculation of Standard time
Now add allowance and bundle handling time with basic time. Bundle handling time refers to tide and untied time of the bundle. Allowance consist following thing-
- Machine allowance = 3% (only for operation).
- Manual allowance = 12% (operator & helper)
- Contingency allowance = 2 % (operator & helper)
Formula used for calculating SMV as follows-
Cycle time = Pick up time + Stitching time + Dispose time
Basic time = Cycle time × Rating
Bundle Handling time = Average Time
SMV =Basic time + Bundle Handling time + Allowance
How to calculate the line efficiency
Like individual operator efficiency, efficiency of a production line or batch or section is important for a factory. Daily line efficiency shows the line performance. To calculate efficiency of a line for a day, we will be needed following data (information) from the line supervisor or line recorder.
1 . Number of operators – how many operators worked in the line in a day.
2 . Working hours (Regular and overtime hours) – how many hours each of the operators worked or how many hours the line run in a day.
3 . Production in pieces – How many pieces are produced or total line output at the end of the day.
4 . Garment SAM – What is exact standard minute of the style ( garment )
Once we have above data you we to calculate following using above information –
1 . Total minutes produced by the line:
To get total produced minutes multiply production pieces by SAM.
2 . Total minutes attended by the all operators in the line:
Multiply number of operators by daily working hours.
Now, calculate line efficiency using following formula:
“Line efficiency = Total minutes produced by the line/total minutes attended by all operators.”
Line efficiency of line 5 was calculated as following:
Produced minute = Output*SMV
=1238*7.72
= 9557.36
Available minute = Manpower*Working hours*60
= 29*8*60
=13920
Therefore,
Line efficiency = (9557.36/13920)*100%
= .69*100%
= 69%
Part 02 :Work Study | Parts of Work Study | Method Study | Objectives of Method Study | Steps of Method Study
Part 03 : Line Balancing | How to Balance a Traditional Sewing Line | Tools required for line balancing
Part 04 :Work Place Layout for Garments | Checklist for Work Station Design | Basic Guide to Work Place Layout
(2633)