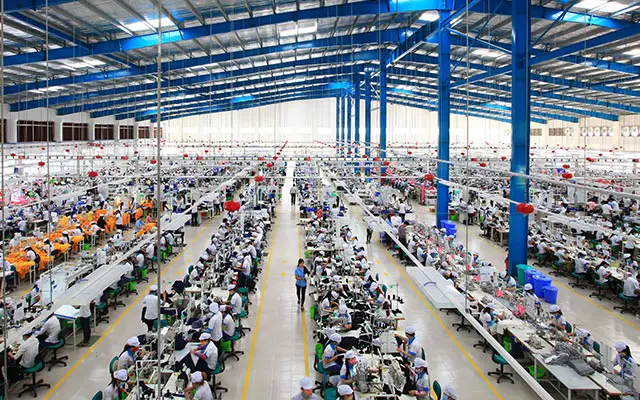
Work Place Layout for Garments | Part 04
Part 01 :Industrial Engineering | Responsibilities of Industrial Engineers (IE) | Working Flow Diagram of I.E Dept.
Part 02 :Work Study | Parts of Work Study | Method Study | Objectives of Method Study | Steps of Method Study
Part 03 : Line Balancing | How to Balance a Traditional Sewing Line | Tools required for line balancing
Work Place Layout for Garments | Checklist for Work Station Design Features | Work Aid
Work Place Layout :
This is the physical arrangement of all of the equipment’s, tools, raw materials and finished garments that are part of the workers workplace. Before beginning the design of any workplace it is important to decide what operations and different styles the workplace will be used for.
There two types of work place are as follows-
- Conventional Work place.
- Specialized Work Place.
Conventional Work place :
- Highly precise and repetitive operations
- Limited variations
- Principles of motion economy
- Limited for any other use
Specialized Work place :
Should be as close as a conventional work station as possible.
Example: Button sewing and buttonhole can be specialized without creating too many difficulties between styles.
Checklist for Work Station Design Features :
Pickup Location :
- What range of sizes and shapes are to be worked on?
- How are these to be handling, to be close enough and ensure correct grasps?
- Are locations allowing for simultaneous and symmetrical pickup and dispose?
- Is the height convenient throughout the handle?
Dispose :
- What is the size and range of shapes to be disposed?
- Is the location convent to the needle allowing disposal to be continuous after sew off?
- Will the disposal stack be set enough and correctly aligned for the next operator?
- Will the stack maintain its shape throughout the bundle?
Positioning :
- Is the area between pick up the needle enough for easy alignment without extra movements?
- Is it too large or too far to one side?
Work Aid :
- Can a guide of folder be employed to simplify guiding and alignment and improve quality.
- If so, would it be better attached to the machine plate or pressure foot? Should it be fixed or moveable.
- Can hand motions be eliminated through use of equipment such as needle position, thread trimmers, dispensers, foot lifters etc?
- Can some of the devices be tied together to operate simultaneously or automatically in sequence?
- Should a simply designed device to aid in separation of piles or pickup be utilized?
Work Aid content :
- Can parts be propositioned to achieve two elemental steps simultaneously?
- Would an inverted “V” or other holder design allow simultaneous one handed pick up and alignment of collar, cuffs etc.?
- Can lose threads trail be covered in a startup seam via positioning it with an air jet?
- Can measuring, marking or notching within an operator be accomplished by use of mounted gauge or utilizing a pneumatically control marker.
Basic Guide to Work Place Layout :
- Positioning of operator
- Comfort of the operator
- Machine at correct height
- Work should be done in normal working area
- Chair should be at the correct at the correct height
Consideration Factor :
- Purpose of the operator
- Product design
- Materials / size
- Safety and inspection
- Materials handling
- Space related
- Operator related
- Working conditions
- Methods
- Miscellaneous
- Who When Where How What
Part 01 :Industrial Engineering | Responsibilities of Industrial Engineers (IE) | Working Flow Diagram of I.E Dept.
Part 02 :Work Study | Parts of Work Study | Method Study | Objectives of Method Study | Steps of Method Study
Part 03 : Line Balancing | How to Balance a Traditional Sewing Line | Tools required for line balancing
(1328)