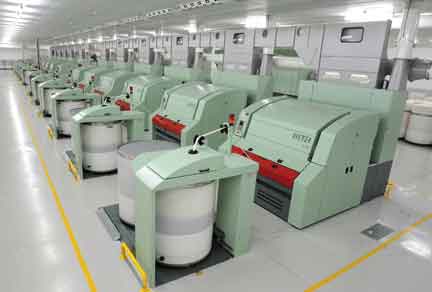
Characteristics of Card Sliver | Part 06
Part 01 | Carding Introduction | | Part 02 | Carding Action
Part 03 |Card Clothing | Types of card clothing | | Part 04 | Auto Leveling in Carding
Part 05 | Measuring Devices in Carding | | Part 06 | Characteristics of Card Sliver
Characteristics of Card Sliver | General Faults in Carding Machine
Carding: Carding is a mechanical process that disentangles, cleans and intermix fibers s to produce a continuous web or sliver suitable for subsequent processing. In this process fibers are opened, parallelized & removes dust, impurities, short fibers to produce continuous strand of sliver. This is achieved by passing the fibers between differentially moving surfaces covered with card clothing. The word is derived from the Latin “CARDUUS” meaning thistle or teasel, as dried vegetable teasels were first used to comb the raw wool.
Card clothing: The pin which is used to cover the surface of carding roller such as taker in, cylinder, doffer and are of fine in diameter, spaced closely and bended in shape is defined as card clothing.
Types of card clothing:
- Flexible card clothing
- Semi-rigid card clothing
- Metallic card clothing
Card Clothing Manufacturers:
- Graf
- Trutzschler
- Lakshmi
- ICC (Indian card clothing)
- ECC (English card clothing)
Card Wire Specification:
P-2040S×0.4–B8R
- Where, 20 = height of wire in mm
- 40= angle of wire in degree
- 4= thickness of wire in mm
Effectiveness of Clothing iInfluenced by Following Factors:
- The quality of wire
- The gauge of wire (distance between two wire)
- The insertion angle of wire in the foundation
- The grinding of the wire points
- The density of the wires
- The height of the wires
General Faults in Carding Machine:
- Lower NRE%: If neps are not removed as standard level therefore, card sliver contain higher neps/gm. This fault is created due to:
- Improper setting between different card surfaces
- Incorrect point density of carding wire
- Damaged carding wire
- Improper geometry of card cloth
- Incorrect speed setting of different carding surfaces
- Higher sliver CVm%: If sliver mass variation is high in card sliver, then CVm% is high. This type of fault is produced due to malfunctioning of card auto leveler.
- Sliver breakage: sliver breaks due to disruption in material inflow and incorrect calendar roller pressure.
- Poor web structure: damaged doffer wire or improper stripping roller function.
- Out of leveling limit: If control limit of leveling is exceeded then machine stops. This type of fault is produced due to disruption in material inflow from blow room or jamming in chute device.
- Roller lapping: calendar roller, coiler calendar roller lapping take place due to improper working ambient condition. (RH%, temp.)
Development in Carding Machine:
- Fire detector
- Continuous suction
- Chute feed system
- Electronic control system
- Each section is driven by separate motion
- Auto leveling
Characteristics of Card Sliver:
- Not proper uniform
- per unit length = 65-80 gr/yd
- Draft = 90-120
- More short fibers present
- More fibers are projected out of the slivers
- Production/hr = (50-100) kg
- Hook is present
- Carded sliver are oriented in different direction
- No of flats 80-116
- No of flats in working position is 30-50
- Can size: (920mm*1200mm)-(1000mm*1220mm)
- No of sliver produced: 1
- Sliver fineness: 0.1-0.2 Ne
- Power required: 5.5-12.5 Kw
- Air required: 1500-300 Nm3
- Automatic Can change
Part 01 | Carding Introduction | | Part 02 | Carding Action
Part 03 |Card Clothing | Types of card clothing | | Part 04 | Auto Leveling in Carding
Part 05 | Measuring Devices in Carding | | Part 06 | Characteristics of Card Sliver
(1553)