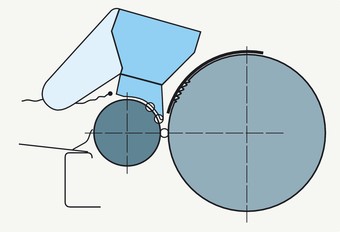
Auto Leveling in Carding | Part 04
Part 01 | Carding Introduction | | Part 02 | Carding Action
Part 03 |Card Clothing | Types of card clothing | | Part 04 | Auto Leveling in Carding
Part 05 | Measuring Devices in Carding | | Part 06 | Characteristics of Card Sliver
Auto Leveling in Carding | Classification of Auto Leveling
Auto Leveling in Carding: In the spinning mill, the card is the effective start of the process, since the first intermediate product, the sliver, is produced here. A relatively high degree of evenness is required in this product. For various reasons, the card cannot always operate absolutely evenly, for example, owing to uneven material feed. Spinning mills are therefore forced to use auto leveling equipment under highly varying circumstances. Different principles for auto leveling can be selected depending upon the quality requirements and the operating conditions in the individual mill.
Classification of Auto Leveling in Carding:
- Short term auto leveling
- Medium term auto leveling
- Long term auto leveling
Fig: auto leveling system of carding m/c.
Irregularities can actually be compensated:
- in the material supply system;
- at the feed;
- at the delivery
The material supply should operate with the greatest possible degree of accuracy in any case, since this has a direct effect on sliver evenness. The main regulating position is the feed; adjusting the feed roller speed, usually performs auto leveling. A distinction should also be drawn between:
- Short-term leveling systems, regulating lengths of product from 10 – 12 cm (rarely used in carding);
- Medium-term leveling systems, for lengths above about 3 m;
- Long-term leveling, for lengths above about 20 m (maintaining count).
In addition, regulating can be performed by open-loop or closed-loop control systems .
I . Principle of short term auto leveling:
Regulation at the delivery:
If this is used, it calls for a drafting arrangement before coiling.
In the open-loop control system illustrated in figure, a measuring point (2) is provided upstream from this drafting arrangement to sense the volume of the incoming sliver and transmit corresponding pulse signals to an electronic control unit. The control signal generated by this unit is passed to a regulating device that can be of various design, and which adapts the speed of the delivery drafting rollers to the measured sliver volume. If the measuring point is located downstream from the drafting arrangement, or if the delivery roller pair itself provides the measuring point, then the system is operating on the closed-loop control principle. If the open-loop principle is used in a short-term auto leveler, short lengths can certainly be made even, but it is not always possible to hold the average sliver count constant. On the other hand, closed-loop control is not suited for regulating short-wave variation because of the dead time inherent in the system. Finally, the drive to the delivery can present problems, since in this system the delivery speed must be continually varied, and in very small ranges. There are two possible applications for assemblies of this type, namely in processing comber noil and where card sliver is fed directly to the rotor spinning machine.
Auto leveling in the in feed:
Reiter card leveling operates as medium-term to long-term leveling (closed-loop, produced by a proportional-integral regulator) and is performed by a microprocessor. In the feed of the card the feed measuring device records the fluctuations in the cross-section of the batt feed. The speed of the feed roller of the card is changed electronically so that these fluctuations in the cross-section are leveled out. The chute is also included in the control loop. However, the filling level is not used for regulating the feed rollers in the chute but is considered as an additional control parameter. In the delivery of the card a pair of disc rollers scans the cross-section of the carded sliver as it emerges. These readings are compared electronically with the preselected set value. Deviations in the set value are corrected electronically by altering the speed of the feed roller in the card.
Fig: Auto leveling with sensing at the feed roller
II . The principle of medium-term auto leveling:
In former Zellweger equipment a medium-term auto leveler was provided as an addition to the long-term auto leveler. An optical measuring device () detects relative variations in the cross-section of the fiber layer on the main cylinder over the whole width of the cylinder. The measuring device is built into the protective cover above the doffer. The device measures reflection of infrared light from the fibers.
After comparison with the set value, a difference signal is generated and passed to an electronic regulating unit. This operates via a regulating drive to adjust the in feed speed of the card so that the depth of the fiber layer on the main cylinder is held constant.
Fig: Medium-term leveling (Zellweger, Uster)
III . The principle of long-term leveling:
This is the most commonly used principle of card auto leveling and serves to keep the sliver count constant. Measuring is performed by a sensor in the delivery (at the delivery roller). The pulses derived in this way are processed electronically so that the speed of the in feed roller can be adapted to the delivered sliver weight via mechanical or electronic regulating devices.
Long-term auto leveling is an integral part of modern cards, and in any case used in production of carded yarns and in the rotor spinning mill.
Fig: Long-term leveling (Zellweger, Uster)
Part 01 | Carding Introduction | | Part 02 | Carding Action
Part 03 |Card Clothing | Types of card clothing | | Part 04 | Auto Leveling in Carding
Part 05 | Measuring Devices in Carding | | Part 06 | Characteristics of Card Sliver
(4529)